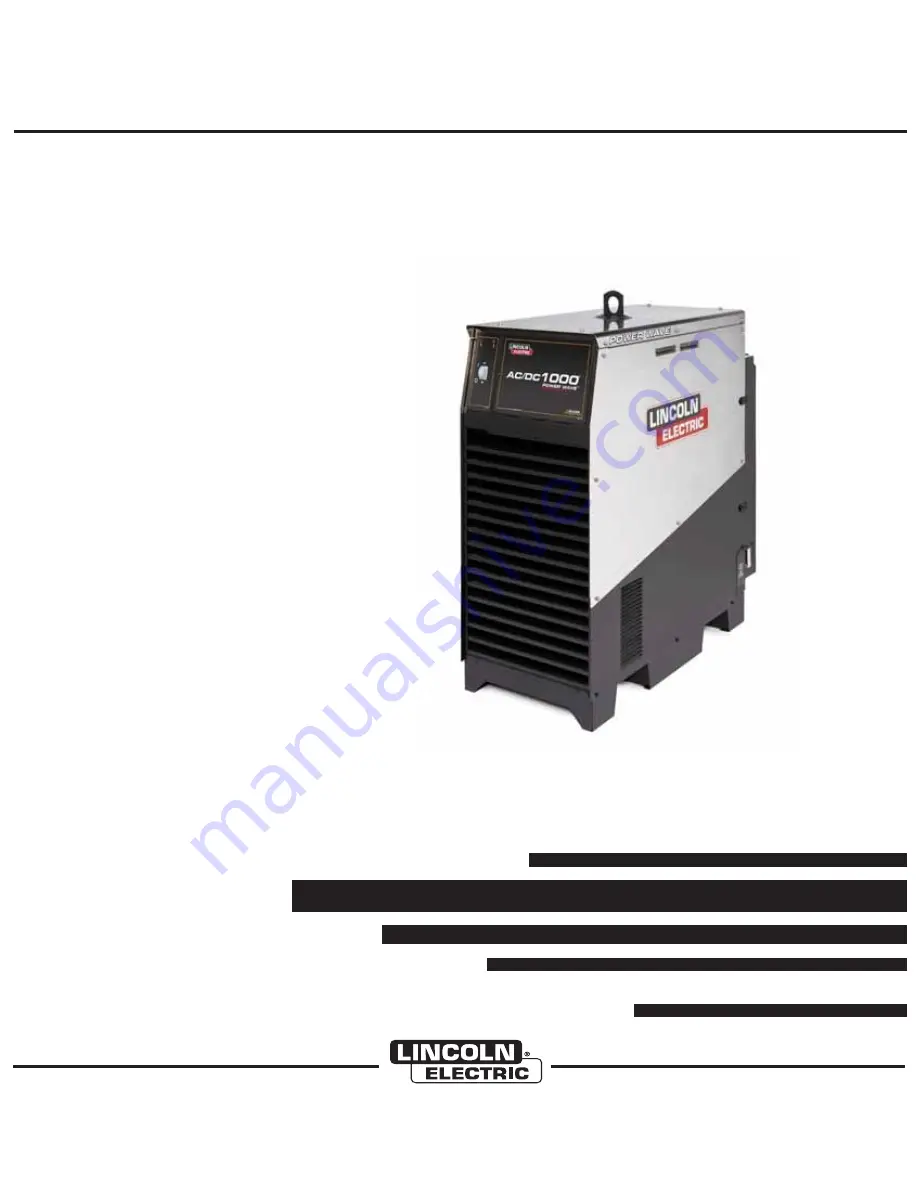
P
POWER WAVE AC/DC 1000 SD
OPERATOR
ʼ
S
MANUAL
IM10022-C
November, 2012
For use with machines having Code Numbers:
11592, 11881, 11918
IP 23
Safety Depends on You
Lincoln arc welding and cutting
equipment is designed and built
with safety in mind. However,
your overall safety can be
increased by proper installation
... and thoughtful operation on
your part.
DO NOT INSTALL,
OPERATE OR REPAIR THIS
EQUIPMENT WITHOUT READ-
ING THIS MANUAL AND THE
SAFETY PRECAUTIONS CON-
TAINED THROUGHOUT.
And,
most importantly, think before
you act and be careful.
®
®
Cleveland, Ohio 44117-1199 U.S.A. TEL: 1.216.481.8100 For Service in U.S. and Canada: Call 1.888.935.3877
FAX: 1.216.486.1751 WEB SITE: lincolnelectric.com For Non-U.S. Service: Email [email protected]
• World's Leader in Welding and Cutting Products • • Sales and Service through Subsidiaries and Distributors Worldwide •
Copyright © Lincoln Global Inc.
Summary of Contents for power wave ac/dc 1000 sd
Page 51: ...NOTES POWER WAVE AC DC 1000 SD...