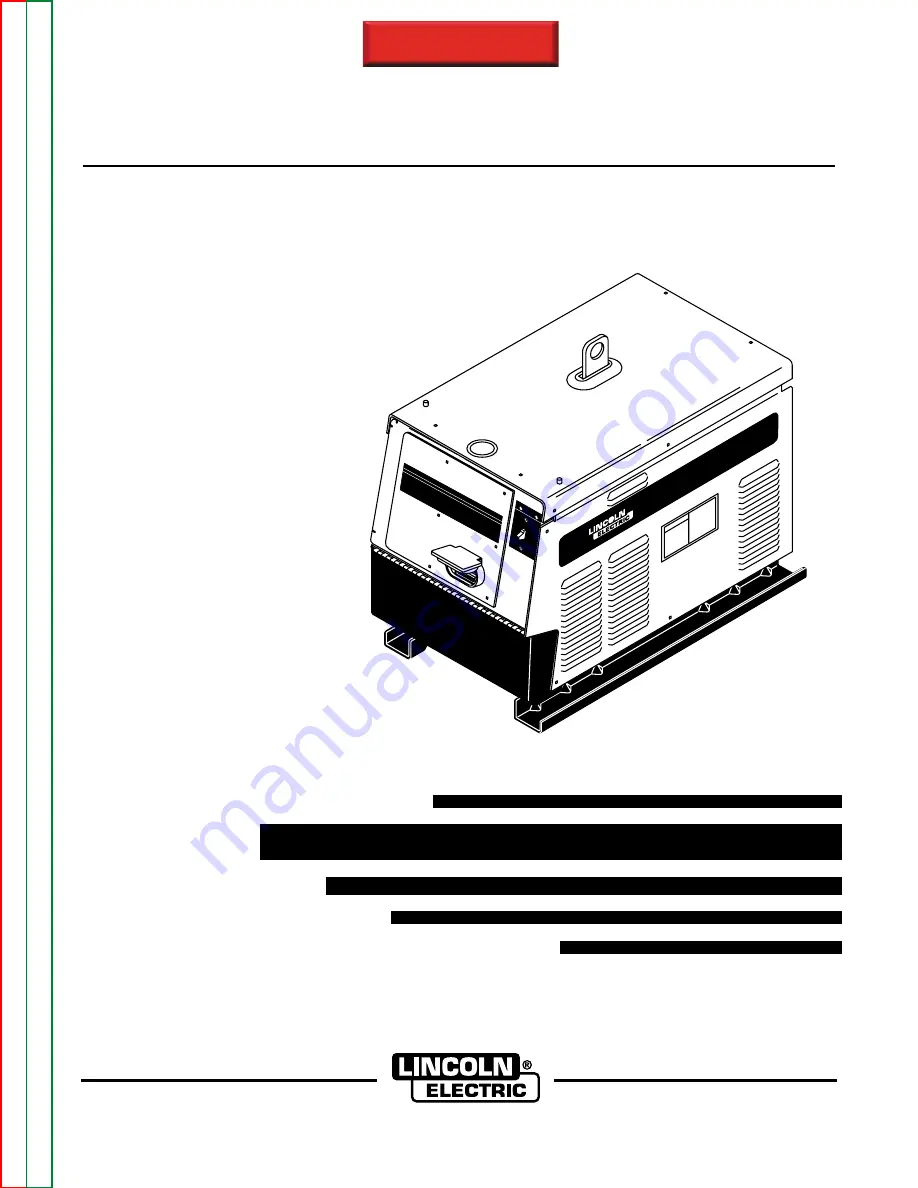
SVM156-A
October, 2001
Safety Depends on You
Lincoln arc welding and cutting
equipment is designed and built
with safety in mind. However,
your overall safety can be in-
creased by proper installation . . .
and thoughtful operation on
your part. DO NOT INSTALL,
OPERATE OR REPAIR THIS
EQUIPMENT WITHOUT
READING THIS MANUAL AND
THE SAFETY PRECAUTIONS
CONTAINED THROUGHOUT.
And, most importantly, think
before you act and be careful.
SERVICE MANUAL
For use with machines having Code Numbers: 10675
10676
POWER WAVE 455/R
TM
Retur
n to Master TOC
Retur
n to Master TOC
Retur
n to Master TOC
Retur
n to Master TOC
V
iew Safety Info
V
iew Safety Info
V
iew Safety Info
V
iew Safety Info
POWER
WA
VE 455/R
I O
N
O O
FF
POWER
WA
VE 455/R
• Sales and Service through Subsidiaries and Distributors Worldwide •
Cleveland, Ohio 44117-1199 U.S.A. TEL: 216.481.8100 FAX: 216.486.1751 WEB SITE: www.lincolnelectric.com
• World's Leader in Welding and Cutting Products •
Copyright © 2001 Lincoln Global Inc.
IEC 60974-1
RETURN TO MAIN MENU