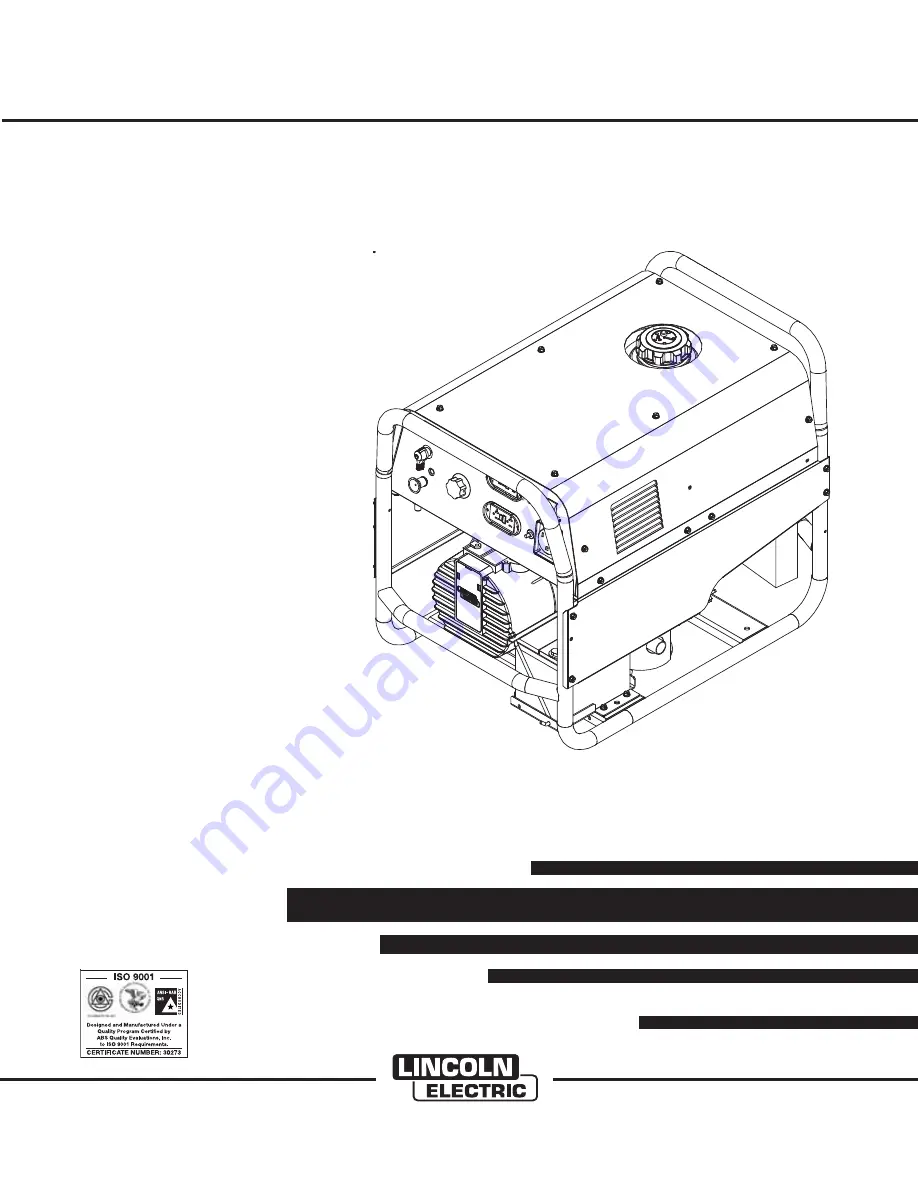
®
• Sales and Service through Subsidiaries and Distributors Worldwide •
Cleveland, Ohio 44117-1199 U.S.A. TEL: 216.481.8100 FAX: 216.486.1751 WEB SITE: www.lincolnelectric.com
• World's Leader in Welding and Cutting Products •
OUTBACK 185
™
OPERATORʼS MANUAL
IM972
September, 2010
Safety Depends on You
Lincoln arc welding and cutting
equipment is designed and built
with safety in mind. However,
your overall safety can be
increased by proper installation
... and thoughtful operation on
your part.
DO NOT INSTALL,
OPERATE OR REPAIR THIS
EQUIPMENT WITHOUT READ-
ING THIS MANUAL AND THE
SAFETY PRECAUTIONS CON-
TAINED THROUGHOUT.
And,
most importantly, think before
you act and be careful.
For use with machines having Code Numbers:
11516
Copyright © Lincoln Global Inc.
Summary of Contents for outback 185
Page 32: ...NOTES OUTBACK 185 ...