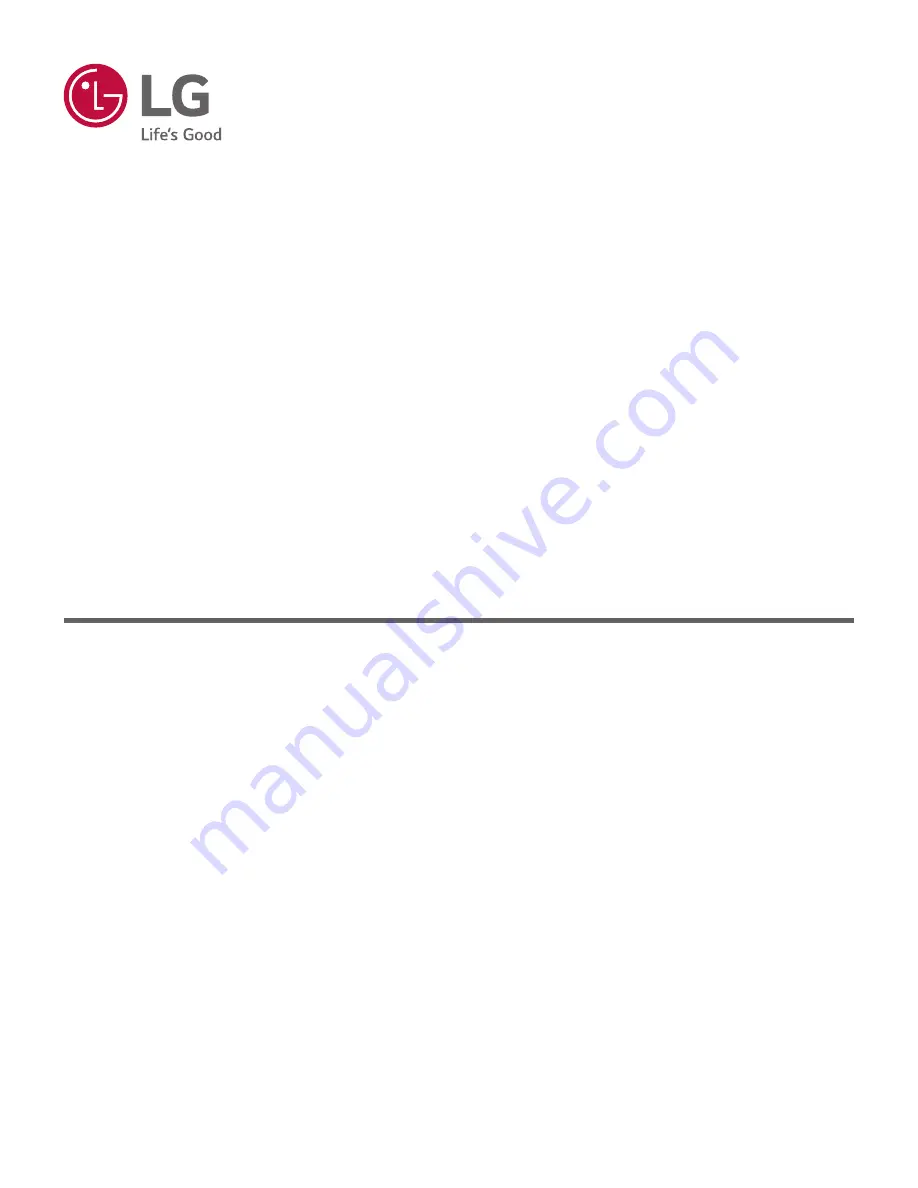
Confidential
MFL71688303_Rev00. 05112020
30" FREESTANDING
ELECTRIC RANGE
SERVICE MANUAL
CAUTION
BEFORE SERVICING THE UNIT, READ THE SAFETY PRECAUTIONS IN THIS MANUAL.
MODEL: LREL6323*
Any reproduction, duplication, distribution (including by way of email, facsimile or other electronic means), publication,
modification, copying or transmission of this Service Manual is STRICTLY PROHIBITED unless you have obtained the
prior written consent of the LG Electronics entity from which you received this Service Manual.
The material covered by this prohibition includes, without limitation, any text, graphics or logos in this Service Manual.
Copyright © 2020 LG Electronics Inc. All rights reserved. Only training and service purposes
Summary of Contents for LREL6323 Series
Page 73: ......