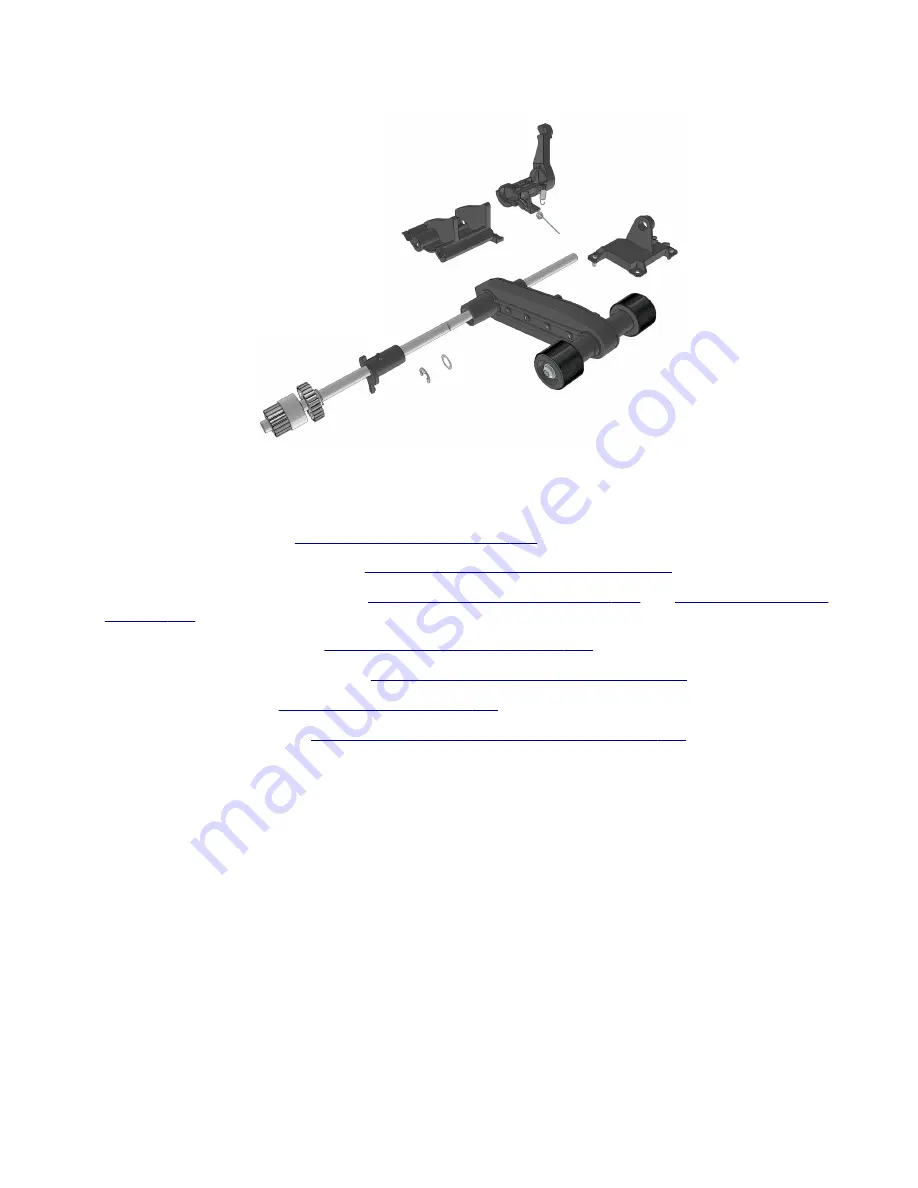
Below is the ACM assembly.
ACM assembly (MX310, MX410) removal
1
Remove the left cover. See
“Left cover removal” on page 279
.
2
Remove the main drive gearbox. See
“Main drive gearbox removal” on page 281
3
Remove the rear door and cover. See
“Rear exit door removal” on page 369
.
4
Remove the power supply. See
“Power supply removal” on page 339
.
5
Remove the power supply shield. See
“Power supply shield removal” on page 340
6
Remove the duplex. See
7
Remove the ACM clutch. See
“ACM clutch removal (MX310, MX410)” on page 289
.
Warning—Potential Damage:
Do not cut the cable (leave the ACM clutch hanging).
7015
Parts removal
361
Summary of Contents for XM1135
Page 214: ...7015 214 ...
Page 238: ...D ADF cover open E Flatbed cover open F paper feed sensor 7015 Service menus 238 ...
Page 308: ...4 Remove the four screws B and then remove the right front mount B 7015 Parts removal 308 ...
Page 323: ...4 Remove the ground shield 5 Remove the display 7015 Parts removal 323 ...
Page 352: ...c Bring the cable in front of the two cable holders near the ACM shaft 7015 Parts removal 352 ...
Page 356: ...9 Remove the two screws C Below are the cam release and bracket 7015 Parts removal 356 ...
Page 362: ...8 Remove the screw A and then detach the trailing edge sensor A 7015 Parts removal 362 ...
Page 363: ...9 Disconnect the two springs B B 7015 Parts removal 363 ...
Page 407: ...3 Swing the right cover backward to remove 4 Remove the screw D D 7015 Parts removal 407 ...
Page 417: ...Power supply PCN1 PCN2 PCN3 PCN5 PCN4 7015 Component locations 417 ...
Page 418: ...7015 418 ...
Page 425: ...Assembly 1 Covers 7015 Parts catalog 425 ...
Page 427: ...Assembly 2 Imaging 7015 Parts catalog 427 ...
Page 430: ...7015 Parts catalog 430 ...
Page 431: ...Assembly 3 Control panel MX41x MX51x XM1140 and XM1145 2 1 3 7015 Parts catalog 431 ...
Page 433: ...Assembly 4 Control panel MX31x 3 2 1 7015 Parts catalog 433 ...
Page 435: ...Assembly 5 Electronics 1 MX31x MX41x and XM1140 1 2 3 4 8 9 5 7 6 7015 Parts catalog 435 ...
Page 438: ...7015 Parts catalog 438 ...
Page 439: ...Assembly 6 Electronics 1 MX51x and XM1145 1 2 9 10 8 7 3 4 5 6 7015 Parts catalog 439 ...
Page 442: ...7015 Parts catalog 442 ...
Page 443: ...Assembly 7 Electronics 2 MX31x MX41x and XM1140 4 3 2 1 6 5 7015 Parts catalog 443 ...
Page 445: ...Assembly 8 Electronics 2 MX51x and XM1145 4 3 2 1 5 6 8 9 7 7015 Parts catalog 445 ...
Page 450: ...7015 Parts catalog 450 ...
Page 451: ...7015 Parts catalog 451 ...
Page 452: ...Assembly 10 Frame MX51x and XM1145 10 11 12 14 13 9 1 5 4 7 8 16 6 2 3 7015 Parts catalog 452 ...
Page 454: ...7015 Parts catalog 454 ...
Page 455: ...Assembly 11 Option trays 3 4 5 6 1 2 7015 Parts catalog 455 ...
Page 458: ...7015 Parts catalog 458 ...
Page 460: ...7015 Parts catalog 460 ...
Page 468: ...7015 468 ...
Page 470: ...7015 470 ...
Page 484: ...7015 484 ...
Page 496: ...7015 Index 496 ...