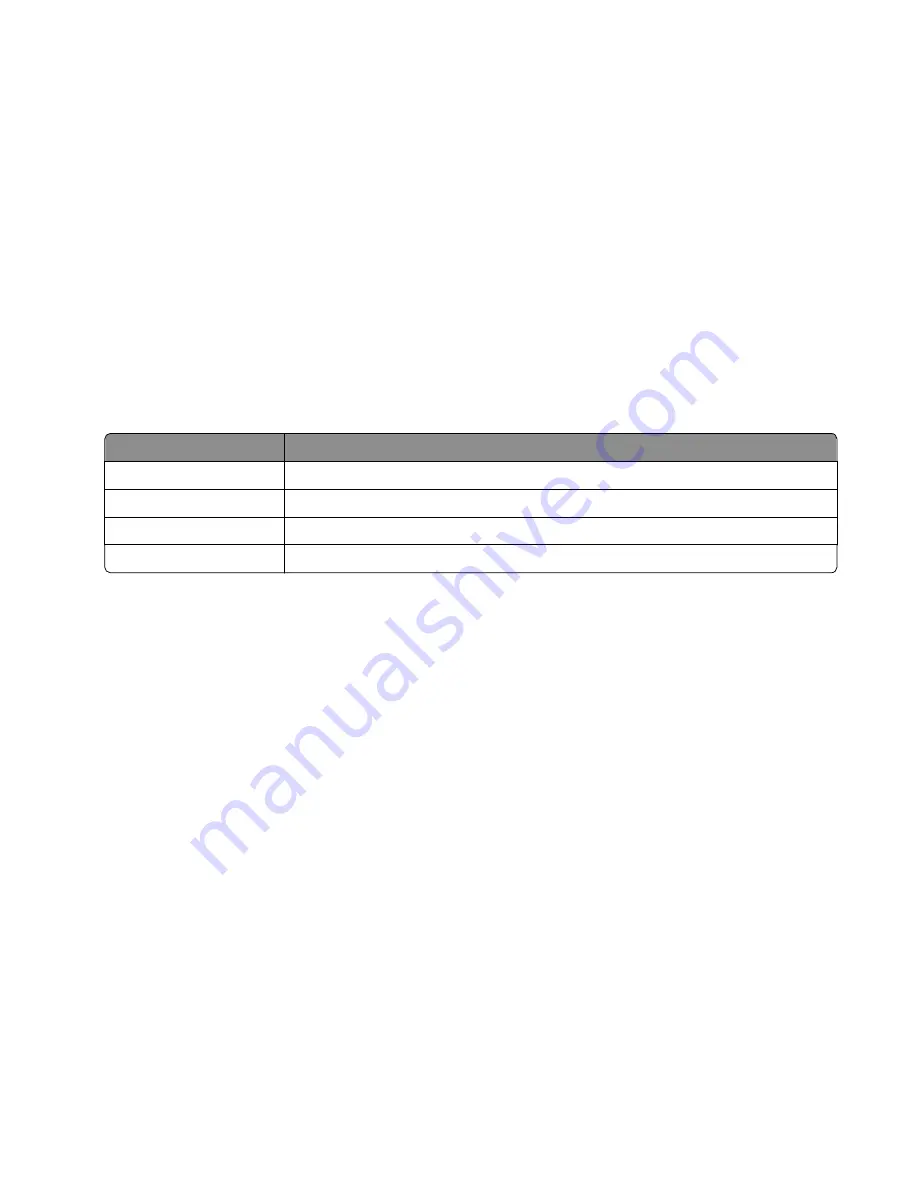
Alignment Menu
Use the alignment menu to align the image on the page for cyan, yellow, and magenta. The black image should be
aligned using REGISTRATION before the individual colors are aligned.
Warning—Potential Damage:
Read the instructions for the alignment carefully.
Setting alignment for color
1
From the Diagnostics menu, touch
Alignment Menu
.
2
Select
CYAN
,
YELLOW
, or
MAGENTA
.
3
Touch
Quick Test
. You may need to scroll to the next page.
A two-page instruction sheet prints.
The printer prints the test page from the default paper source, however if the default source only supports
envelopes, then the page prints from Tray 1. Print on A4 or letter paper for the best results.
4
Determine which settings to change and follow the instructions on the printed sheets to determine the adjustment.
Description
Range
Top Margin
-128 to +127
Left Margin
-2500 to +2500 (-1000 to +1000 for Yellow)
Right Margin
-2500 to +2500 (-1000 to +1000 for Yellow)
Linearity
Linearity has a separate Quick Test sheet and adjustment instructions.
5
Touch (
-
) to decrease the value or (
+
) to increase the value. After the value appears, touch to save the value or
Back
to cancel.
6
Reprint the Quick Test to evaluate the changes. Continue until each adjustment is correct.
7
Repeat steps 4 through 6 as needed.
8
Continue until all three colors are aligned. A separate Quick Test prints for each color.
9
Touch
Back
to exit the Alignment Menu
Scanner calibration
This diagnostic test is used to calibrate both the Black and white values for the ADF and the flatbed. The following values
can be adjusted using this menu item:
•
Flatbed Black – Values are -10 to 10. The default value is 0.
•
ADF Front Black – Values are -10 to 10. The default value is 0.
•
ADF Back Black – Values are -10 to 10. The default value is 0.
•
Flatbed White – Values are -10 to 10. The default value is 0.
•
ADF Front White – Values are -10 to 10. The default value is 0.
•
ADF Back White – Values are -10 to 10. The default value is 0.
7527
Service menus
196
Summary of Contents for XC2132
Page 18: ...7527 18 ...
Page 22: ...7527 22 ...
Page 34: ...7527 34 ...
Page 54: ...2 Open the top door 7527 Diagnostic information 54 ...
Page 184: ...7527 184 ...
Page 226: ...7527 226 ...
Page 314: ...5 Disconnect the belt C 6 Disconnect the fan and remove 7527 Repair information 314 ...
Page 345: ...Component locations Controller board CX310 models 7527 Component locations 345 ...
Page 346: ...CX410 models 7527 Component locations 346 ...
Page 352: ...7527 352 ...
Page 359: ...7527 359 ...
Page 361: ...Assembly 1 Covers 7527 Parts catalog 361 ...
Page 363: ...Assembly 2 Scanner 7527 Parts catalog 363 ...
Page 365: ...Assembly 3 Paperpath 7527 Parts catalog 365 ...
Page 368: ...7527 Parts catalog 368 ...
Page 369: ...Assembly 4 Operator panels 7527 Parts catalog 369 ...
Page 372: ...7527 Parts catalog 372 ...
Page 373: ...Assembly 5 Electronics 7527 Parts catalog 373 ...
Page 376: ...7527 Parts catalog 376 ...
Page 377: ...Assembly 6 Cables and sensors 7527 Parts catalog 377 ...
Page 379: ...Assembly 7 Media drawers and trays 7527 Parts catalog 379 ...
Page 382: ...7527 382 ...
Page 390: ...7527 390 ...
Page 404: ...7527 404 ...
Page 422: ...7527 Part number index 422 ...
Page 428: ...7527 Part name index 428 ...