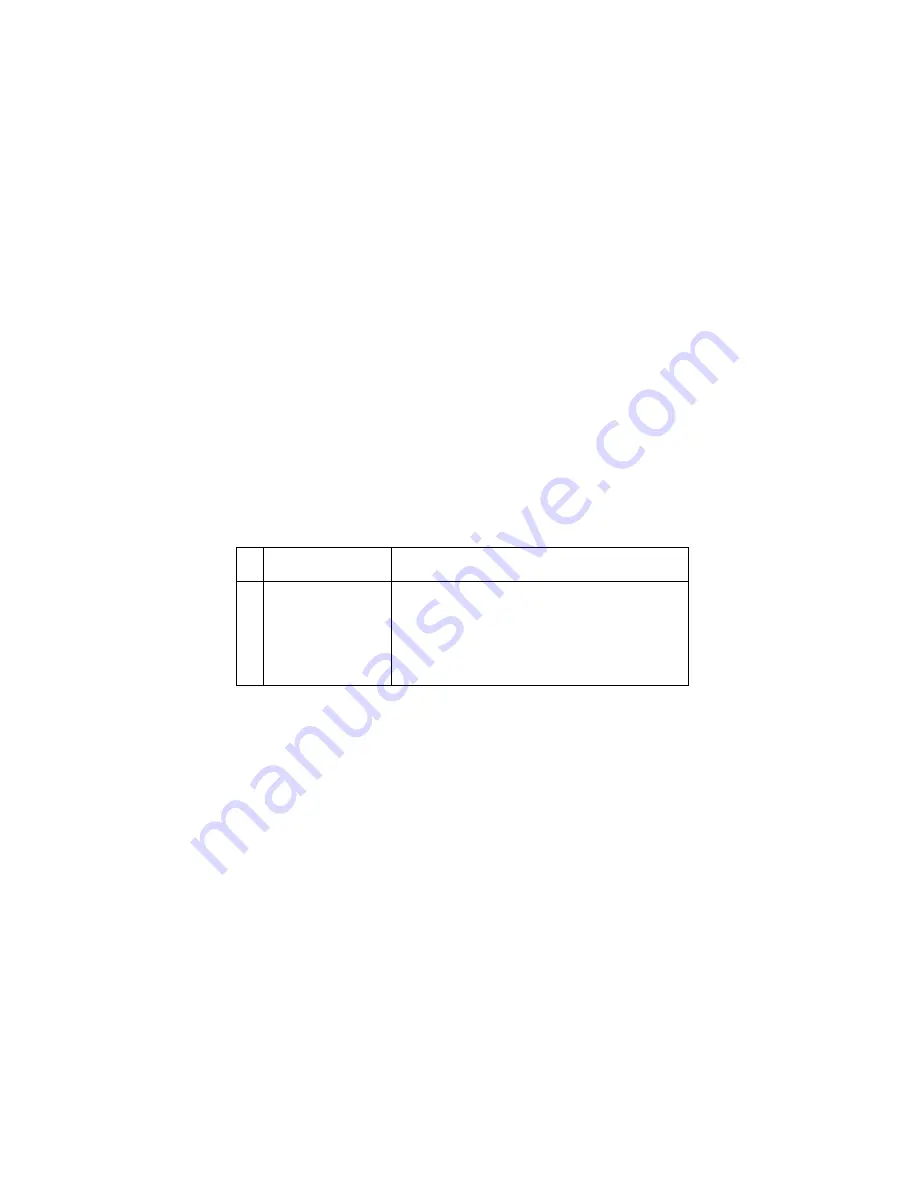
2-32
4227-100
Tractor 2 Service Check
The Tractor 2 sensor opens during installation, when its actuator
touches the printer cover. The home sensor detects the position of
the slider.
•
When Tractor 2 is selected, the motor-driven Tractor 2 slider
pushes the printer sub slider cam lever to engage the printer
gear train which drives the Tractor 2 tractors.
•
When the Tractor 2 is deselected, the motor retracts the slider,
disengaging the Tractor 2 gear drive and reengaging the printer
tractors.
63D Tractor2 HP Error
The Tractor 2 home sensor was never initialized after turning the printer off
and then on, or made at the wrong time.
(The same error indication is used for carrier home failure.)
FRU
Action
1
Tractor 2
Home Sensor
Remove the Tractor 2 and turn the printer off
and then on again to determine if the fault is in
the printer or Tractor 2.
If the gear teeth chatter just before the error is
displayed, replace the home sensor.
Summary of Contents for 4227-100
Page 10: ...x 4227 100 Korean Safety Information...
Page 101: ...Connector Locations 5 1 4227 100 5 Connector Locations...
Page 105: ...Connector Locations 5 5 4227 100 Component Location Illustrations...
Page 106: ...5 6 4227 100 Component Location Illustrations Continued...
Page 114: ...5 14 4227 100 Connector Block Diagram...
Page 119: ...Parts Catalog 7 2 Assembly 1 Covers and Operator Panel...
Page 121: ...Parts Catalog 7 4 Assembly 2 Paper Feed...
Page 123: ...Parts Catalog 7 6 Assembly 3 Carrier...
Page 125: ...Parts Catalog 7 8 Assembly 4 Base and Electronics...
Page 127: ...Parts Catalog 7 10 Assembly 5 ASF Side Frame Covers...
Page 129: ...Parts Catalog 7 12 Assembly 6 ASF Roller Support...
Page 131: ...Parts Catalog 7 14 Assembly 7 Tractor 2 Option...