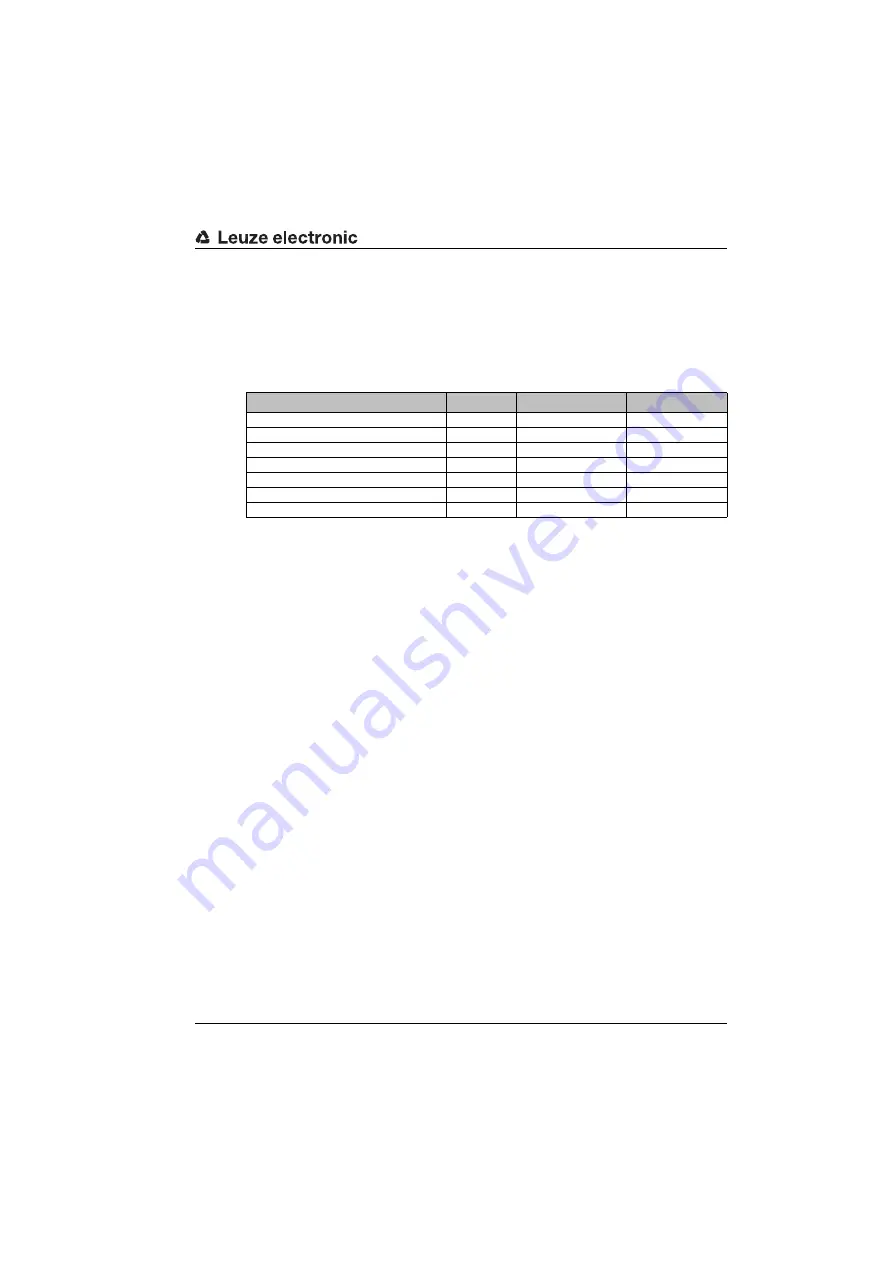
Electrical connection
Leuze electronic
LES 36
43
TNT
35/7-2
4
V
6.2
Shielding and line lengths
The Light section sensors of the 36/36HI series are equipped with modern electronics devel-
oped for industrial applications. In industrial environments, a number of sources of interfer-
ence may affect the sensors. In the following, information is provided on EMC-compliant
wiring of the sensors and of the other components in the switch cabinet and on the machine.
Observe the following maximum line lengths:
Shielding:
1.
Ground the LES housing
:
Connect the housing of the LES via the functional earth (FE) screw provided for this
purpose (see Figure 6.3, devices produced after April 2011) with the protective con-
ductor on the machine star point. The cable should have an impedance as low as pos-
sible for high-frequency signals, i.e., be as short as possible and have a large cross-
sectional area (grounding strip, …).
If the LES does not yet have an FE screw of its own, please use one of the M4 holes
on the dovetail.
Important
: Place a lock washer underneath and check the penetration of the anodized
coating of the LES housing by measuring the electrical connection from FE star point
to the connector sleeves without connected sensor cables so that other FE interrup-
tions can be detected on the machine base and profile rails as well.
2.
Shield all connection cables to the LES
:
Apply the shield to FE on both sides. On the LES end, this is ensured if the LES housing
is connected to FE (PE) as described under 1. (shield fitted over the connector sleeves
to the housing).
In the switch cabinet, clamp the shield flat to FE. To do this, use special
shielding
clamps
(e.g., Wago, Weidmüller, …).
Keep the length of the shieldless cable end as short as possible.
The shield should not be connected at a terminal in a twisted fashion (no "RF braid").
3.
Disconnect power and control cables
:
Lay the cables for the power components (motor cables, lifting magnets, frequency
inverters, …) as far from the sensor cables as possible (distance > 30cm). Avoid laying
power and sensor cables parallel to one another.
Cable crossings should be laid as perpendicular as possible.
4.
Lay cables close to grounded metal surfaces
:
This measure reduces interference coupling in the cables.
Connection to sensor
Interface
Max. cable length
Shielding
Power supply unit
X1
50m
required
Activation / cascading / trigger
X1
50m
required
PC/Host
X2
50m
required
Encoder
X3
50m
required
Switching inputs/outputs
X3
10 m
required
Analog output voltage/current
X4
10 m
required
PROFIBUS DP
X4
10 m
required
Table 6.2:
Cable lengths and shielding