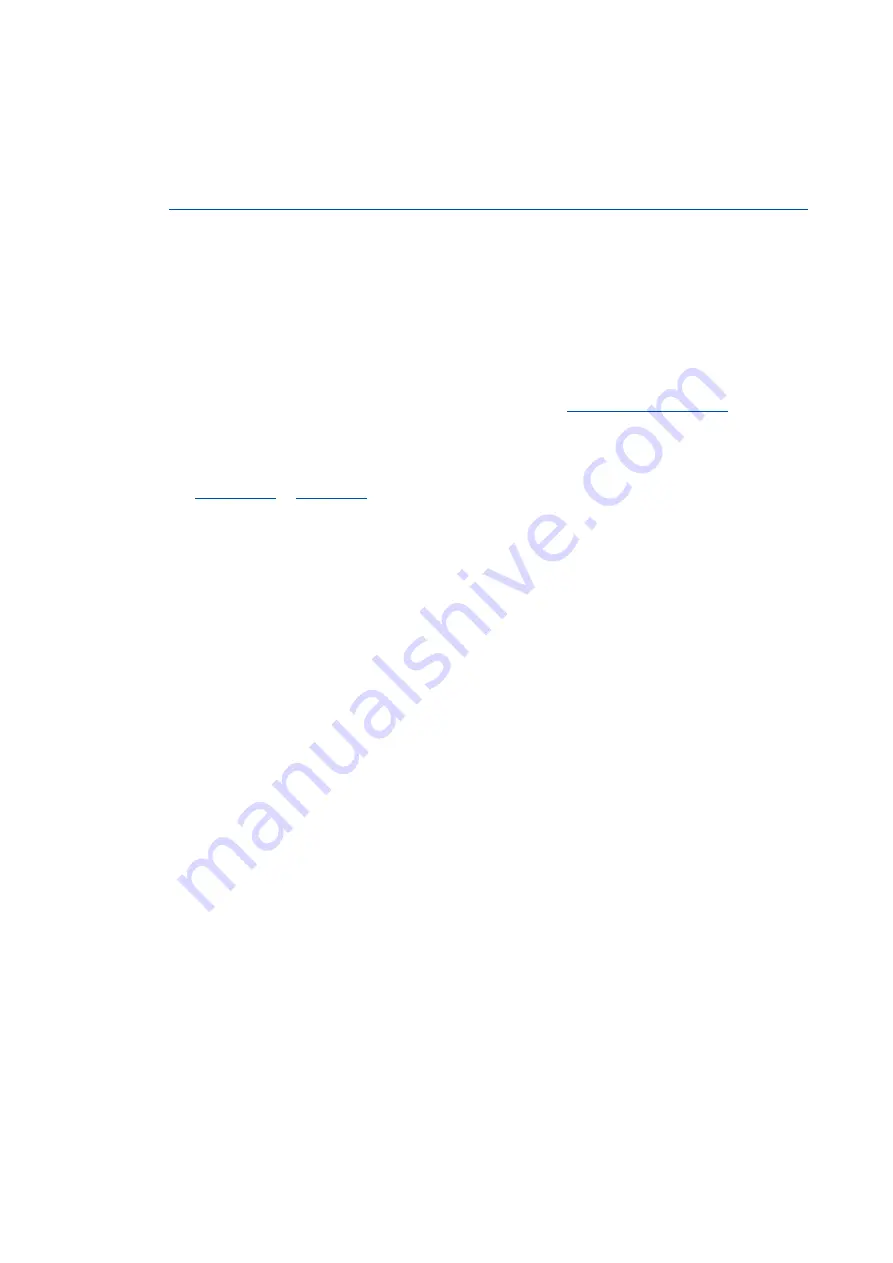
8
Basic drive functions (MCK)
8.4
Basic settings
546
Lenze · 8400 HighLine · Reference manual · DMS 12.0 EN · 06/2017 · TD23
_ _ _ _ _ _ _ _ _ _ _ _ _ _ _ _ _ _ _ _ _ _ _ _ _ _ _ _ _ _ _ _ _ _ _ _ _ _ _ _ _ _ _ _ _ _ _ _ _ _ _ _ _ _ _ _ _ _ _ _ _ _ _ _
8.4.7
Setpoint holdback for bus runtime compensation
This function extension is available from version 12.00.00!
Basics of the "setpoint holdback" function
In case of a master/slave application in which a slave drive must follow a master drive with a precise
angle, the data coupling from axis to axis is mostly effected via real-time capable fieldbuses (e.g.
CAN).
• Here, the data is always transferred in a time-controlled way. The axes are synchronised, i.e. the
reading of the process data and its internal processing are effected at the same time.
During a synchronous run between a master and several slaves, mostly a position and speed
setpoint generated by the master are transferred to the slaves.
• The setpoints are generated in the master, usually by the
system
block.
• The setpoints are transferred to the slaves via PDOs.
• The output to the respective fieldbus is effected via the corresponding port blocks (e.g.
).
Due to the bus cycle time (e.g. 1 ms or 2 ... 4 ms for buses with a higher load) and the telegram
runtimes (approx. 260
μ
s per PDO @500 kbits), the setpoints generated by the master arrive in the
slave axes with a delay. At this time, the master has already transferred the setpoints to the control
loops of the motor control. This offset causes an error in the synchronism of the axes.
• In case of a mechanical coupling, e.g. a portal feed with two drives, an inclination of the two feed
drives is caused.
• This behaviour is more or less distinctive for all serial bus systems depending on the
transmission speed and cycle time.
A further delay between the reading of the received data and the forwarding to the control loops is
caused by the internal cycle time of the inverters (1 ms for the 8400 device series).