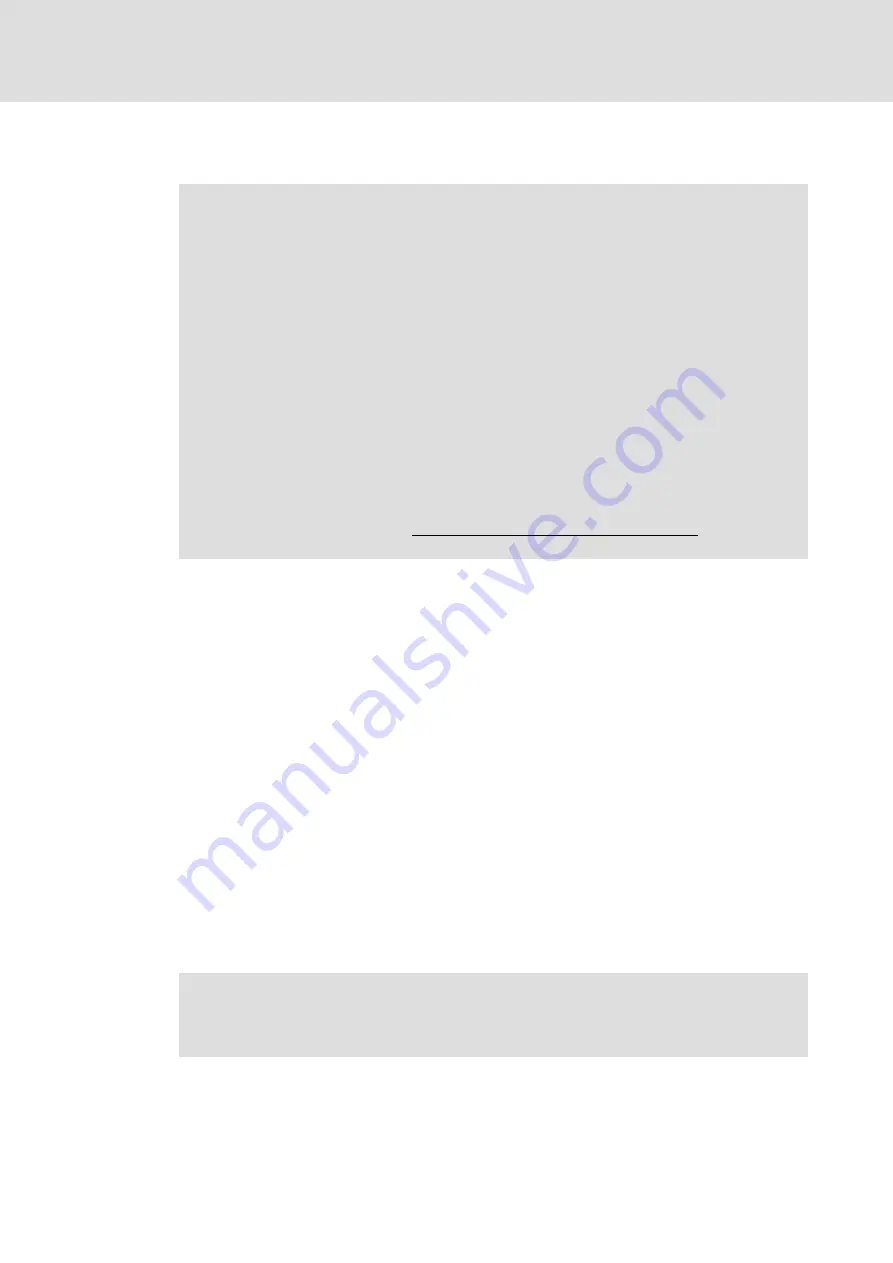
Electrical installation
Wiring of the feedback system
Encoder connection
88
EDBCSXS064 EN 4.0
5.6.2
Encoder connection
Danger!
Valid when using an operating software up to and including V7.0:
When absolute value encoders are used, uncontrolled movements of the drive
are possible!
If an
absolute value encoder
is disconnected from the axis module during
operation, the fault OH3−TRIP occurs. If the
absolute value encoder
now is
connected to X8 again and a TRIP−RESET is carried out, the drive may start up in
an uncontrolled manner with a high speed and a high torque. A SD8−TRIP will
not occur, as would be expected.
Possible consequences:
ƒ
Death or severe injuries
ƒ
Destruction or damage of the machine/drive
Protective measures:
ƒ
If a fault (trip) occurs during commissioning when an
absolute value
encoder
is used, check the history buffer C0168. If an Sd8−TRIP is at the
second or third place, a reinitialisation is absolutely necessary. For this
purpose, switch off and on again the 24−V supply of the control electronics.
Via the 9−pole Sub−D−plug X8, you can connect the following encoders:
ƒ
Incremental encoder (TTL encoder)
– with two 5 V complementary signals (RS−422) that are electrically shifted by 90°.
– with zero track that can be connected optionally.
ƒ
Sin/cos encoder (singleturn or multiturn rotary transducer)
– with supply voltage (5 ... 8 V).
– with serial communication.
The initialisation time of the axis module is extended to approx. 2 s.
The controller supplies the encoder with voltage.
Use C0421 to set the supply voltage V
CC
(5 ... 8 V) to compensate, if required, the voltage
drop [
D
V] on the encoder cable:
D
U
^
2
@
L
L
[m]
@
R
ń
m[
W
ń
m]
@
I
G
[A]
D
V
Voltage drop on the encoder cable [V]
L
L
Cable length [m]
R/m
Ohmic resistance per meter of cable length [
W
/m]
I
G
Encoder current [A]
Stop!
Observe the permissible supply voltage of the encoder used. If the values in
C0421 are set too high, the encoder can be destroyed!