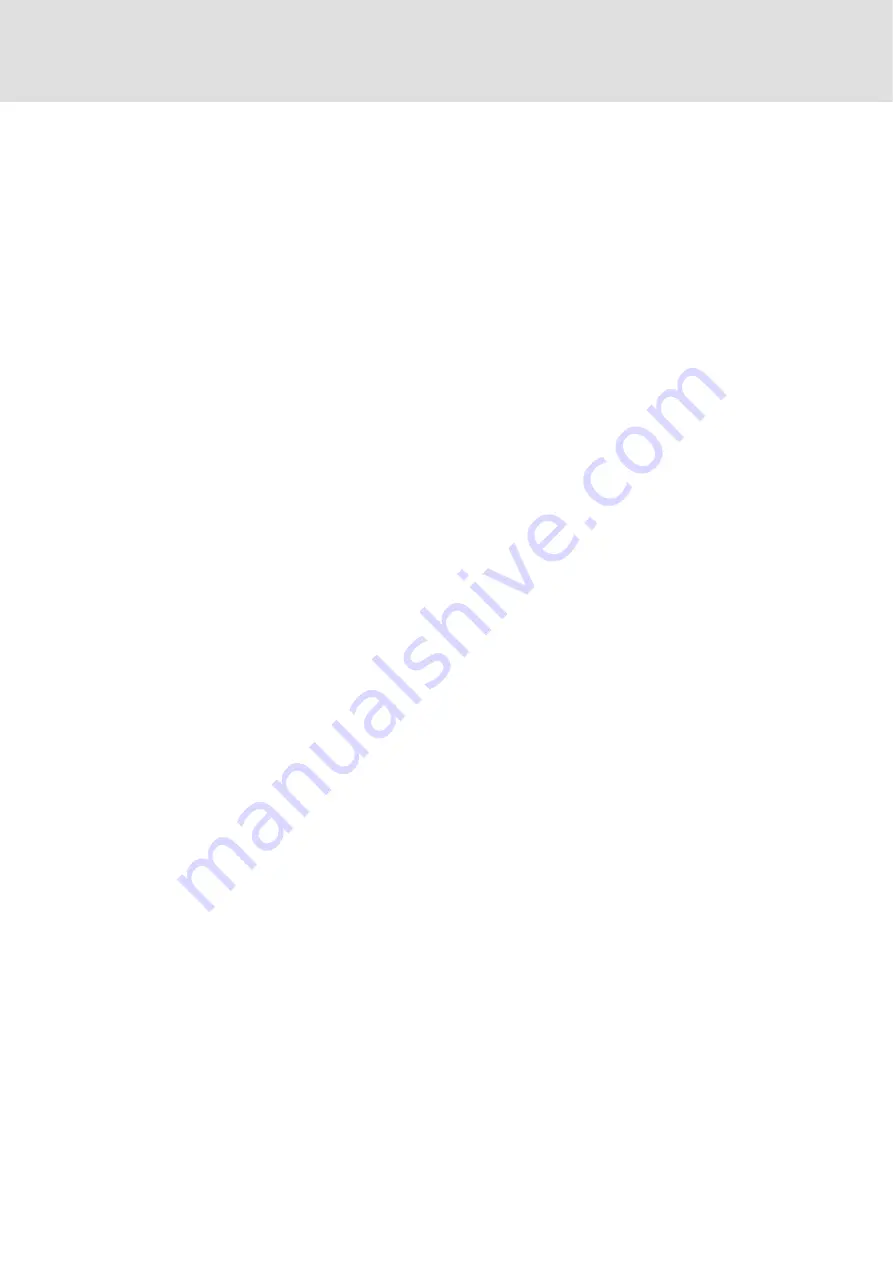
CANopen communication
About CANopen
User data
5
17
KHB 13.0003-EN
2.0
5.1.4
User data
The master and the drive controller communicate with each other by exchanging data
telegrams via the CAN bus.
The user data range of the CAN telegram contains network management data, parameter
data or process data:
ƒ
Network management data (NMT data)
Network service: E.g. all CAN nodes can be influenced at the same time.
ƒ
Process data (PDO, process data objects)
– Process data is transferred via the process data channel.
– Process data can be used to control the drive controller.
– The master can directly access the process data. The data is, for instance, directly
assigned to the I/O area of the master. It is necessary that the control and the drive
controller can exchange data within a very short time interval. For this purpose,
small amounts of data can be transferred cyclically.
– Process data is not stored in the drive controller.
– Process data is transferred between the master and the drive controllers to ensure
a continuous exchange of current input and output data.
– Examples for process data are, for instance, setpoints and actual values.
ƒ
Parameter data (SDO, service data objects)
– Parameters are set, for instance, for the initial system set-up during
commissioning or when the material is changed on a production machine.
– Parameter data is transferred by means of so-called SDOs via the parameter data
channel. The transfer is acknowledged by the receiver, i.e. the sender gets a
feedback about the transfer being successful or not.
– The parameter data channel enables the access to all CANopen indexes.
– In general, the transfer of parameters is not time-critical.
– Examples for parameter data are, for instance, operating parameters, diagnostic
information and motor data.