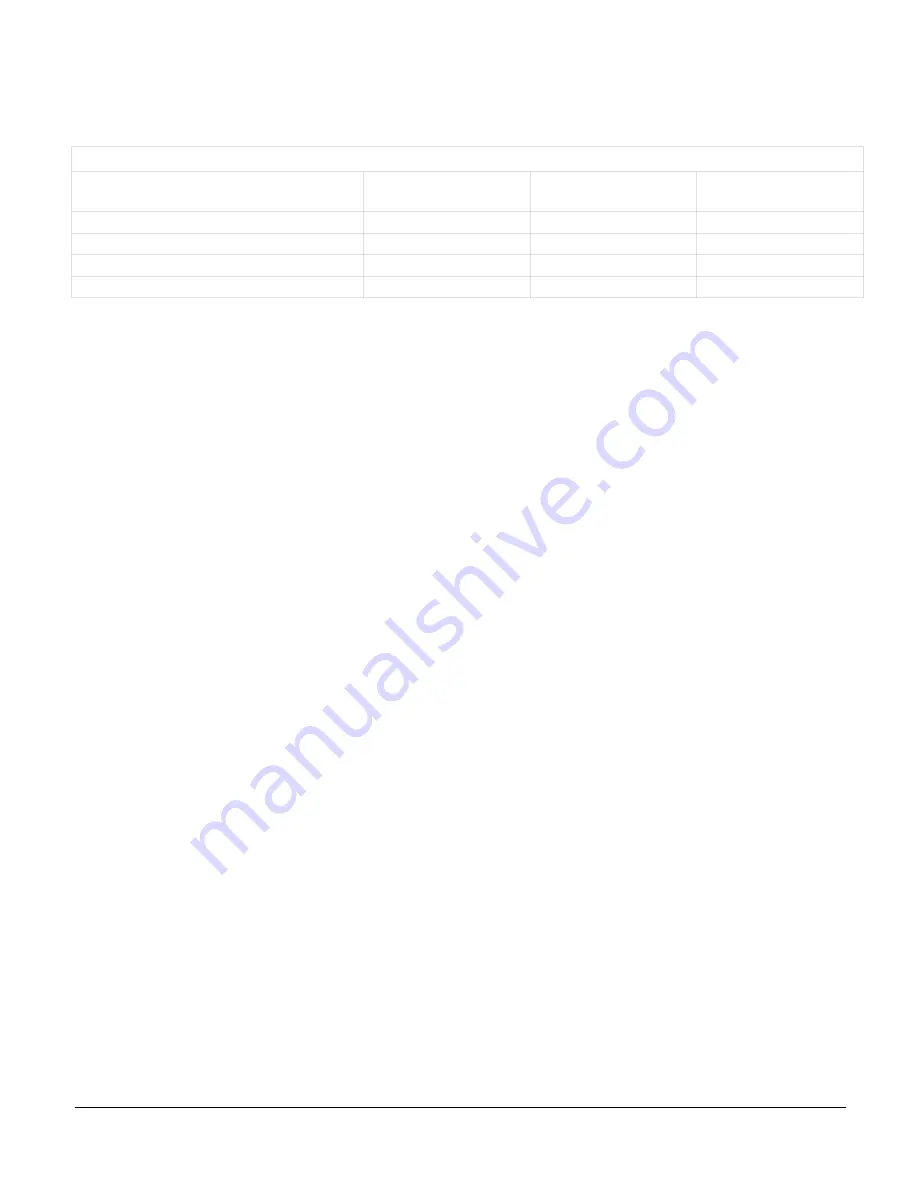
58
13.5.2.5.
Tuning
In the event that the PID loop requires tuning, the following two methods are recommended depending on the severity of
the problem:
1. In most cases the parameters will only need a small adjustment. In that case use the following table as a basic guide.
Table 39. Tuning
Change Desired
Parameter 31
PID P
Parameter 32
PID I
Parameter 33
PID D
Reduce Response time
Increase
Decrease
Decrease
Reduce Overshoot
Decrease
Increase
Increase
Reduce Settling Time
Decrease
Decrease
Reduce Offset (steady state error)
Increase
Decrease
2. If method 1 adjustment does not stabilize the system, you may use the following tuning method:
NOTE
: To use this method the system must be allowed to operate at the manual reset value (% output) without damaging
the system.
A
Set the parameters 31, 32 and 33 blower PID constants to 0 (OFF).
B
Start system. Analog output value will be at the parameter 41 (SUPPLY MANUAL RESET) value (%).
C
Monitor system. System should be stable. If system is not stable at this point check for other problems. Adjusting
the PID parameters will not solve this problem.
D
If system is stable, gradually increase the parameter 31 (SUPPLY PID P CONST) until system starts oscillating
(moving above and below set point, continuously).
E
Reduce the parameter 31 (SUPPLY PID P CONST) to 4070% of the value set in step D.
F
Gradually start adding some parameter 32 (SUPPLY PID I CONST) by setting to 127 and reduce setting until the
steady state error (offset) is reduced to an acceptable level.
G
If necessary, increase the parameter 33 (SUPPLY PID D CONST) to reduce overshoot. Use of parameter 33 (D)
can increase settling time and/or lead to instability.
NOTE
: It is recommend that in most cases it is best not to use any parameter 33 (SUPPLY PID D CONST).