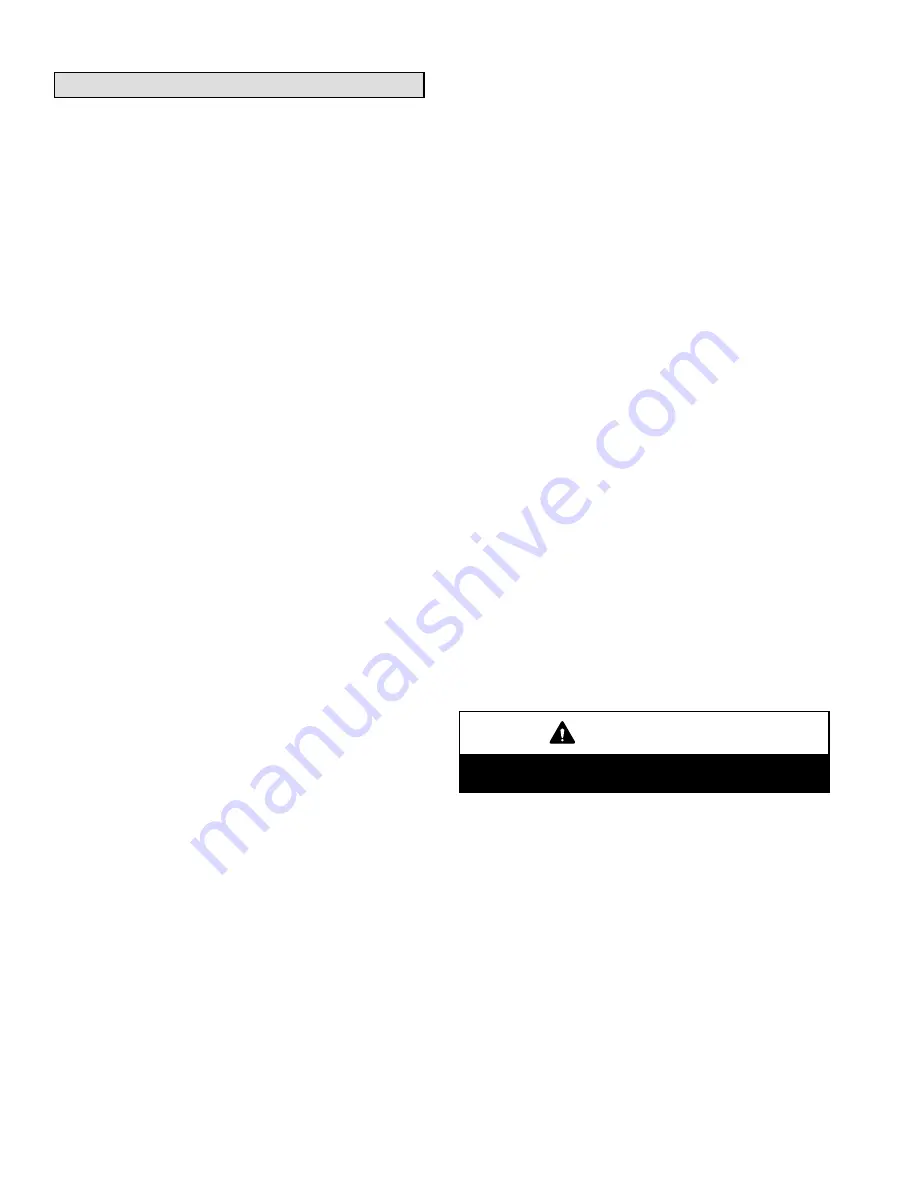
Page 19
508117-01 2/2021
Cooling Start-Up
IMPORTANT-The crankcase heater must be energized
for 24 hours before attempting to start compressor. Set
thermostat so there is no demand to prevent
compressors from cycling. Apply power to unit.
NOTE - These units must not be used as a “construction
heater” at any time during any phase of construction. Very
low return air temperatures, harmful vapors and
misplacement of the filters will damage the unit and its
efficiency. Additionally, a unit which will be subject to cold
temperatures when not in operation must have a vapor
barrier installed to seal the duct connections. Failure to
protect the unit from moisture laden air or harmful vapors
(generated from the construction process and temporary
combustion heating equipment) will cause corrosive
condensation within the unit. Failure to properly protect
the unit in this situation will cause electrical and electronic
component failure and could affect the unit warranty
status.
A-Preliminary Checks
1- Make sure that unit is installed in accordance with the
installation instructions and applicable codes.
2- Inspect all electrical wiring, both field‐ and
factory‐installed, for loose connections. Tighten as
required.
3- Check to ensure that refrigerant lines do not rub against
the cabinet or against other refrigerant lines.
4- Check voltage at disconnect switch. Voltage must be
within range listed on nameplate. If not, consult
power company and have voltage condition
corrected before starting unit.
5- Make sure filters are in place before start‐up.
B-Start-Up
Supply Air Staged Blower - Refer to the Multi-Staged Air
Volume Start-Up section.
1- Initiate first and second stage cooling demands using
this mobile service app menu path:
SERVICE > TEST > COOLING > COOL4
Instructions provided with the thermostat may also be
used to initiate cooling.
2- First-stage thermostat demand will energize indoor
blower in Low Cooling CFM. Second-stage
thermostat demand will energize indoor blower in
High Cooling CFM. Both demands energize
compressor 1 (variable speed compressor). The
remaining compressors will be energized to
modulate the discharge air temperature.
3-
156, 180 -
Units contain three refrigerant circuits or systems.
See figure 20.
210, 240, 300 -
Units contain four refrigerant circuits or systems. See
figure 21.
4- Each refrigerant circuit is separately charged with
R410A refrigerant. See unit rating plate for correct
amount of charge.
5- Refer to the
Refrigerant Check and Charge
section to
check refrigerant charge.
C-R410A Refrigerant
Units charged with R410A refrigerant operate at much
higher pressures than R22. The expansion valve and
liquid line drier provided with the unit are approved for use
with R410A. Do not replace them with components
designed for use with R22.
R410A refrigerant is stored in a pink cylinder.
IMPORTANT
Mineral oils are not compatible with R410A. If oil
must be added, it must be a polyol ester oil.
Manifold gauge sets used with systems charged with
R410A refrigerant must be capable of handling the higher
system operating pressures. The gauges should be rated
for use with pressures of 0-800 on the high side and a low
side of 30” vacuum to 250 psi with dampened speed to
500 psi. Gauge hoses must be rated for use at up to 800
psi of pressure with a 4000 psi burst rating.