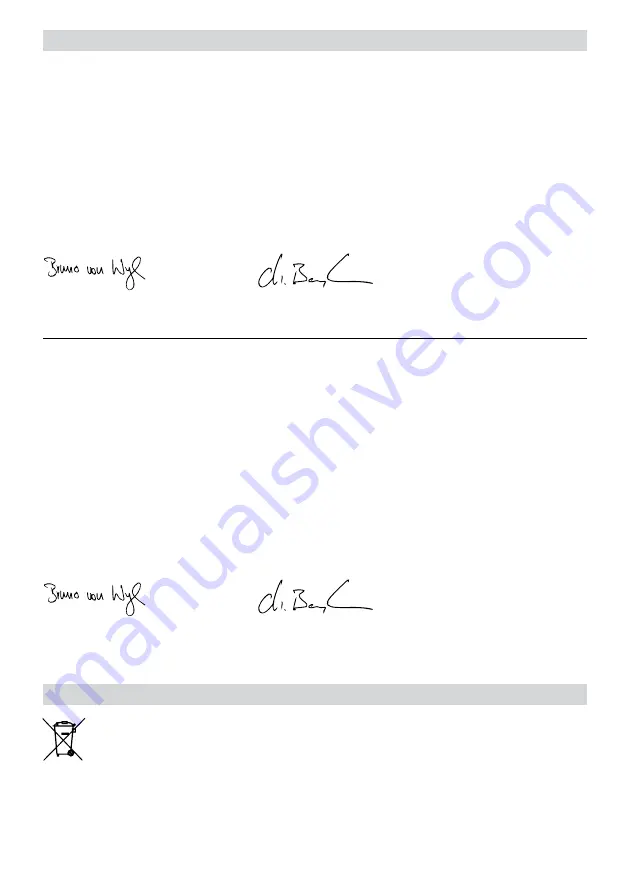
58
EU Declaration of Conformity
Leister Technologies AG, Galileo-Strasse 10, 6056 Kaegiswil, Switzerland
confirms that this product fulfills
the requirements of the following EU Guidelines in the models that we have made available for purchase.
Directives:
2006/42/EC, 2014/30/EU, 2014/53/EU, 2011/65/EU
Harmonized
EN ISO 12100, EN 60335-1, EN 60335-2-45, EN 55014-1, EN 55014-2,
standards:
EN 61000-3-2, EN 61000-3-3, EN 61000-3-11, EN 61000-6-2, ETSI EN 300 328,
EN IEC 63000
Name of authorized representative for documentation: Thomas Schäfer, Manager Product Conformity
Kaegiswil, 04/14/2021
Bruno von Wyl, CTO
Christoph Baumgartner, GM
UK Declaration of Conformity
Leister Technologies AG, Galileo-Strasse 10, 6056 Kaegiswil, Switzerland
confirms that these products, in the
versions as brought into circulation through us, fulfil the requirements of the following UK Statutory Instruments.
UK Statutory
Instruments:
2008 No. 1597, 2016 No. 1091, 2017 No. 1206, 2012 No. 3032
Designated
BS EN ISO 12100, BS EN 60335-1, BS EN 60335-2-45, BS EN 55014-1, BS EN 55014-2,
Standards:
BS EN 61000-3-2, BS EN 61000-3-3, BS EN 61000-3-11, BS EN 61000-6-2,
ETSI EN 300 328, BS EN IEC 63000
Name of authorized representative for documentation: Thomas Schäfer, Manager Product Conformity
Kaegiswil, 03/31/2021
Bruno von Wyl, CTO
Christoph Baumgartner, GM
23. Declaration of Conformity
Do not dispose of electrical tools in household waste.
Electrical equipment, accessories and packaging should be recycled in an environmentally friendly
manner.
24. Disposal
Summary of Contents for UNIROOF 300
Page 28: ...28 Switching off Target and Actual Value Display see 10 4 Switching on ECO Mode see 10 5...
Page 29: ...29 Switching off Data Recording see 10 6 Switching on Advanced Mode see 10 7...
Page 37: ...37 10 7 Advanced mode settings Example Activate WLAN Press 4 times...
Page 38: ...38 Switch on Info Mode Example Setting the time...
Page 39: ...39 General information Reset distance counter...