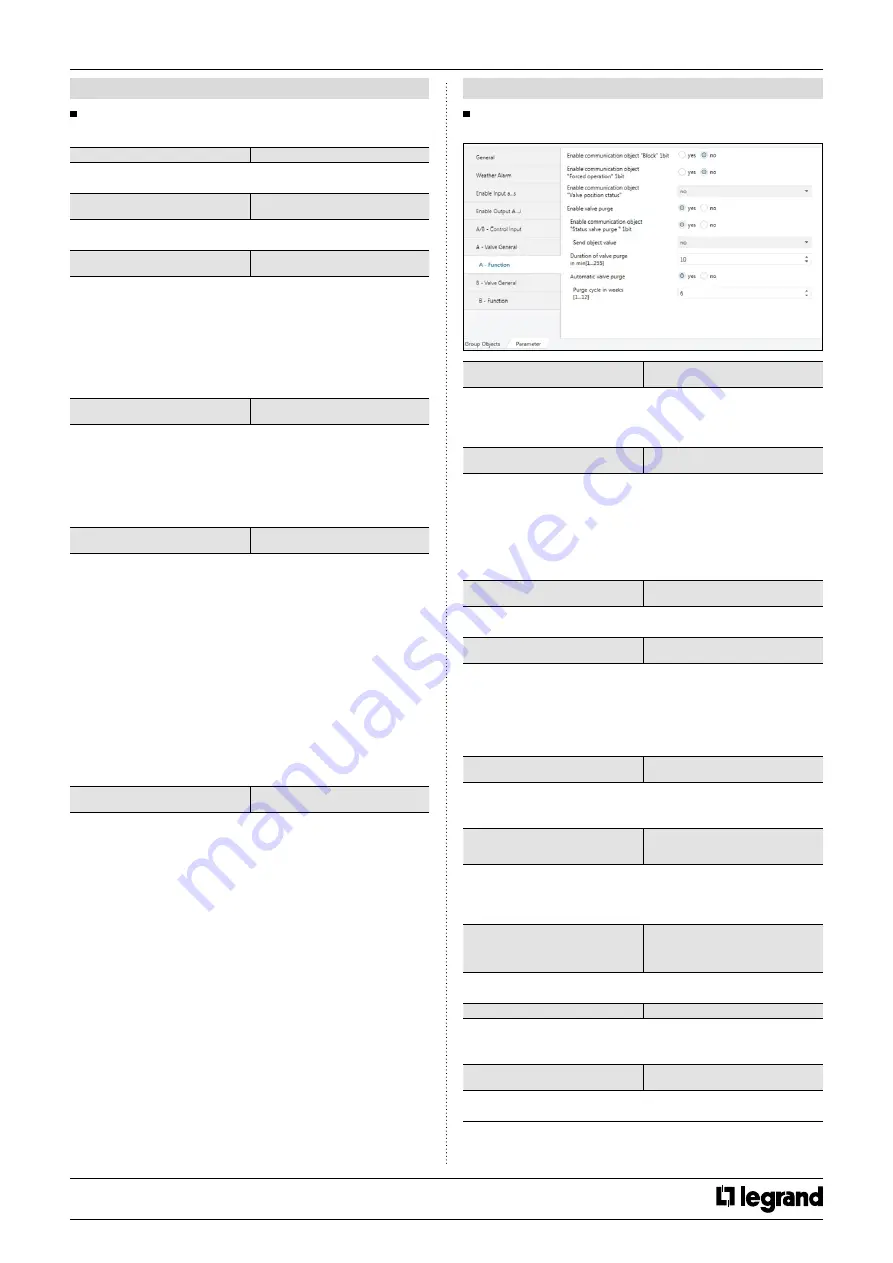
22/29
Technical data sheet: S000114123EN-1
Updated:
Created: 18/01/2021
Cat. No(s): 0 026 72/73/74/76/78/79
KNX controller multi-application DIN
7 . COMMUNICATION OBJECTS (continued)
7 .9 "Valve Control" parameter (continued)
7 .9 .2 "A – Valve General" parameter (continued)
Valve position [0…100]%
*0
…100
This parameters are configured the blind height and slat position.
Valve contact type
*normally open
normally closed
This parameter is used to select reaction after bus voltage recovery.
Value control duration from 0…100% in s
[10…6000]
0…
*180
…6000
With this parameter, a time is set in seconds that the connected valve
requires to move from position 0 % (valve closed) to position 100 %
(valve fully open). If the valve control parameter is selected three point
open/close, this parameter is visible.
For example, the time is 180s, the current valve position is at 20%, the
target position is 60%, and then the travel time of the valve will need
72s from 20% to 60%.
Automatically adjust valve position in s
[10…6000]
*no
yes
This function is mainly used to correct the valve position, for example,
the valve is not fully opened or closed after long working hours due
to various reasons lead to the valve position slight inaccuracies, such
temperature, aging of the device etc. So it needs to be repositioned
via the function. If the valve control parameter is selected three point
open/close, this parameter is visible.
Number of valve control up to adjustment
[1…65535]
1…
*100
…65535
This parameter is selected automatic adjustment threshold
which automatic adjustment is undertaken. Assuming that the
parameterized value is 100, when the number of valve controls arrived
to 100, if the valve is adjusted to the opening direction on the 101st
adjustment, then the automatic adjustment is not executed, if to the
closing direction, the automatic adjustment will be executed, and
the valve is adjusted to the position 0%, and then adjusted to the
target position. For example, on the 100st the valve position is 50%,
if the 101st the valve position is 60%, the valve position is adjusted
directly to 60% and do not execute an automatic adjustment until a
reversal control value is received. If the 101st the valve position is 40%,
an automatic adjustment is undertaken and the valve is adjusted to
the position 0%, and then adjusted to the target position 40%. The
automatic adjustment is exceeded the closing position by % 5 of the
total travel time. This time is maximum one minute.
Valve limitation
yes
*no
The limitation of the control value limits the height of the control
value. The limitation is activated, when a value is chosen which
is smaller/higher than the possible value for the control value, so
minimum larger than 0 or maximum smaller than 1.If an input signal is
out of the adjusted limitation, it will be decreased or increased.
Example:
At the heating mode, the maximum limit is chosen as
70% and the minimum limit is chosen as 10%. The valve opening is
adjusted as 10min. If a control value is sent as 100% for the input, the
channel takes the maximum limit of 70% and calculates from this
value the on-pulse as 7min. A control value in the limitations works
normal, so a control value of 50% creates an on-pulse of 5min
7 . COMMUNICATION OBJECTS (continued)
7 .9 "Valve Control" parameter (continued)
7 .9 .3 "A – Function" parameter
Enable communication object “Block” 1 bit
yes
*no
A channel can be blocked for further operations by its blocking object.
While valve is moving, block object is activated the valve finished its
move.
Block on object value
*1
0
1
: The blocking is triggered by sending a logical “
1
” at the belonging
block object. Only through sending a logical “
0
”, the channel is
unblocked again.
0
: The blocking is triggered by sending a logical “
0
” at the belonging
block object. Only through sending a logical “
1
”, the channel is
unblocked again.
Enable communication object “Forced
operation” 1 bit
yes
*no
The forced position drives the control value to a fixed position.
Forced operation on obj value
*1
0
1
: A logical “
1
” activates the forced position. By sending a logical “
0
”,
the forced position is deactivated
0
: A logical “
1
” activates the forced position. By sending a logical “
0
”,
the forced position is deactivated and the channel goes back to its last
value or the last received telegram for the control value.
Value position on forced operation In %
[0…100]
0…
*30
…100
This parameter determines the valve position after forced operation
activates.
Enable communication object “Valve
position status”
*no
1 bit
1 byte
This parameter is select sends/responds the actual value of the valve
percentage. The valve status object is sent as soon as possible after
the control value is received.
Send object value
*no
after a change
after request
after change or request
The parameter is selected object send type.
Duration of valve purge In min [1…255]
1…
*10
…255
If the valve purge is activated, the actuator opens the corresponding
valve for a period.
Automatic valve purge
yes
*no
Automatic control can be enabled with this parameter.
CONTENTS