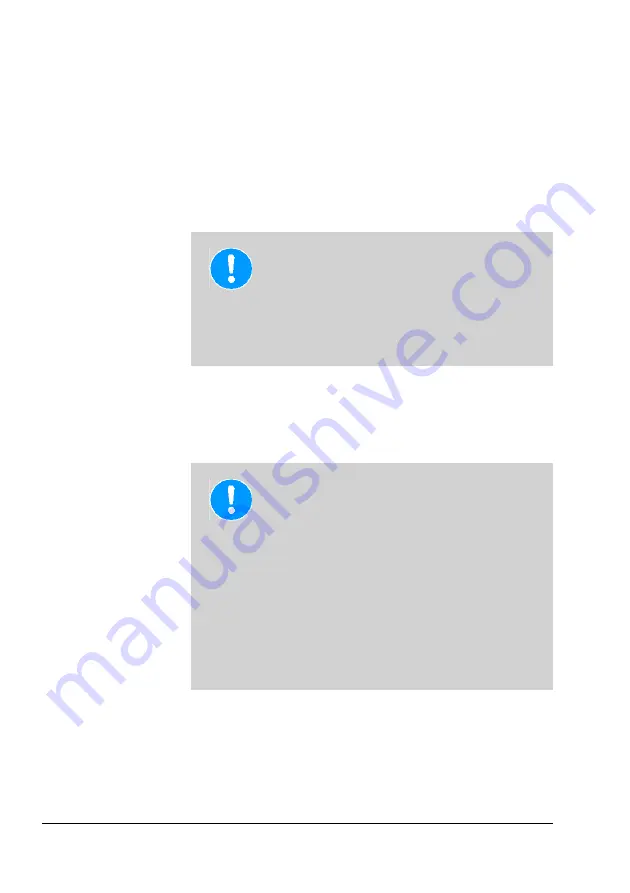
Assembly
36
30.11.12
6.7 Required Tools
•
Torque driver (centric operating)
•
Clean, lint-free cloth
•
Purifier (e.g. ethanol)
6.8 Remove Transport Locking
The positioning system is fixed with a transport locking
(red bracket) to protect it from shipping damage.
NOTICE
Risk of property damage caused by
improper cleaning!
Improper cleaning may lead to
significant property damage.
•
Keep purifier free from live parts.
NOTICE
Risk of property damage caused by
improper handling!
Improper handling may lead to
significant property damage.
•
Remove transport locking before
switching on power supply.
•
Save the transport locking.
•
Insert transport locking before
every transport.