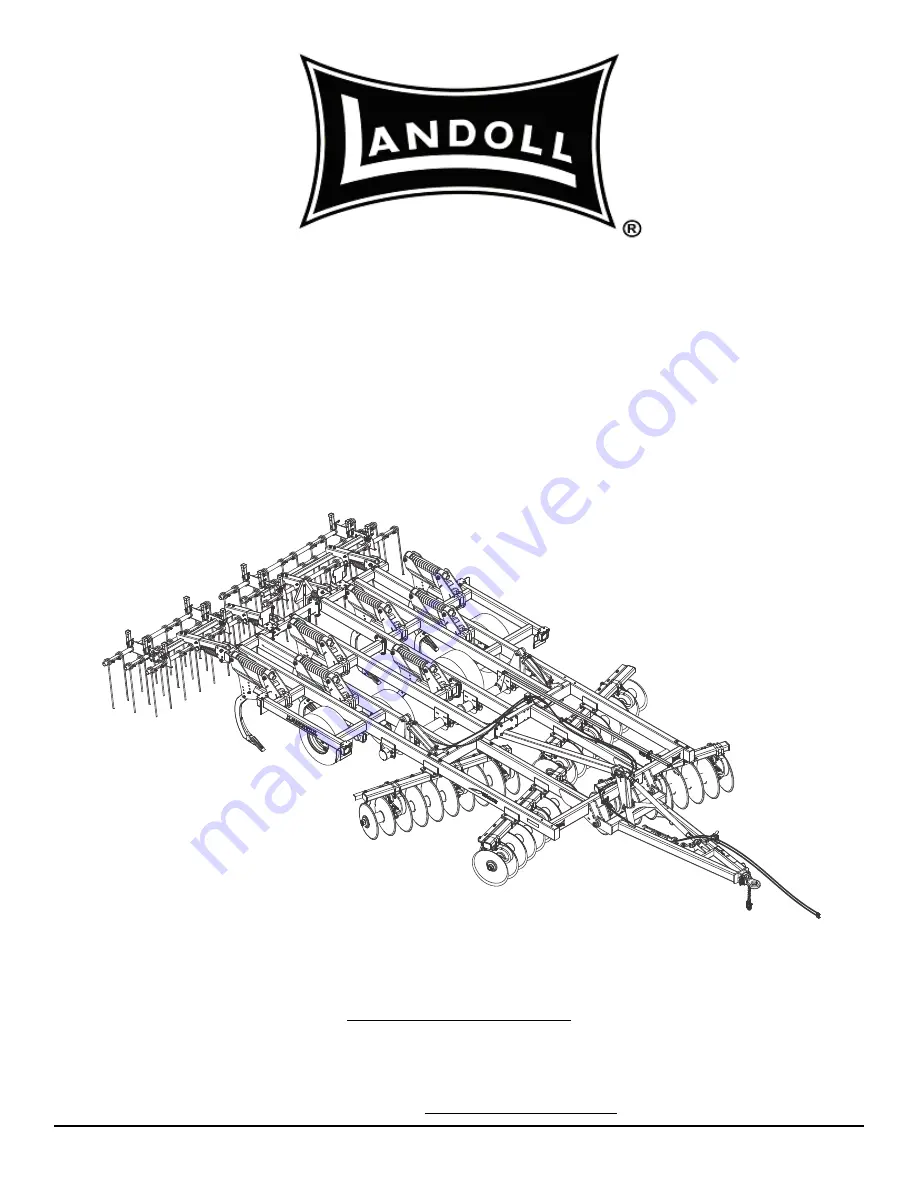
F-620-0912
09/2012
LANDOLL CORPORATION
1900 North Street
Marysville, Kansas 66508
(785) 562-5381
800-428-5655 ~ WWW.LANDOLL.COM
Model 2410
Weatherproofer I
Operator’s Manual
Summary of Contents for Weatherproofer I 2410
Page 2: ......
Page 18: ...2 12 F 620 0912 Edition STANDARD SPECIFICATIONS...
Page 58: ...3 40 F 620 0912 Edition ASSEMBLY INSTRUCTIONS Notes...
Page 69: ...OPERATION AND MAINTENANCE 4 11 Notes...
Page 70: ...4 12 F 620 0912 Edition OPERATION AND MAINTENANCE Page Intentionally Blank...
Page 72: ...5 2 F 620 0912 Edition TROUBLESHOOTING GUIDE Notes...
Page 73: ......