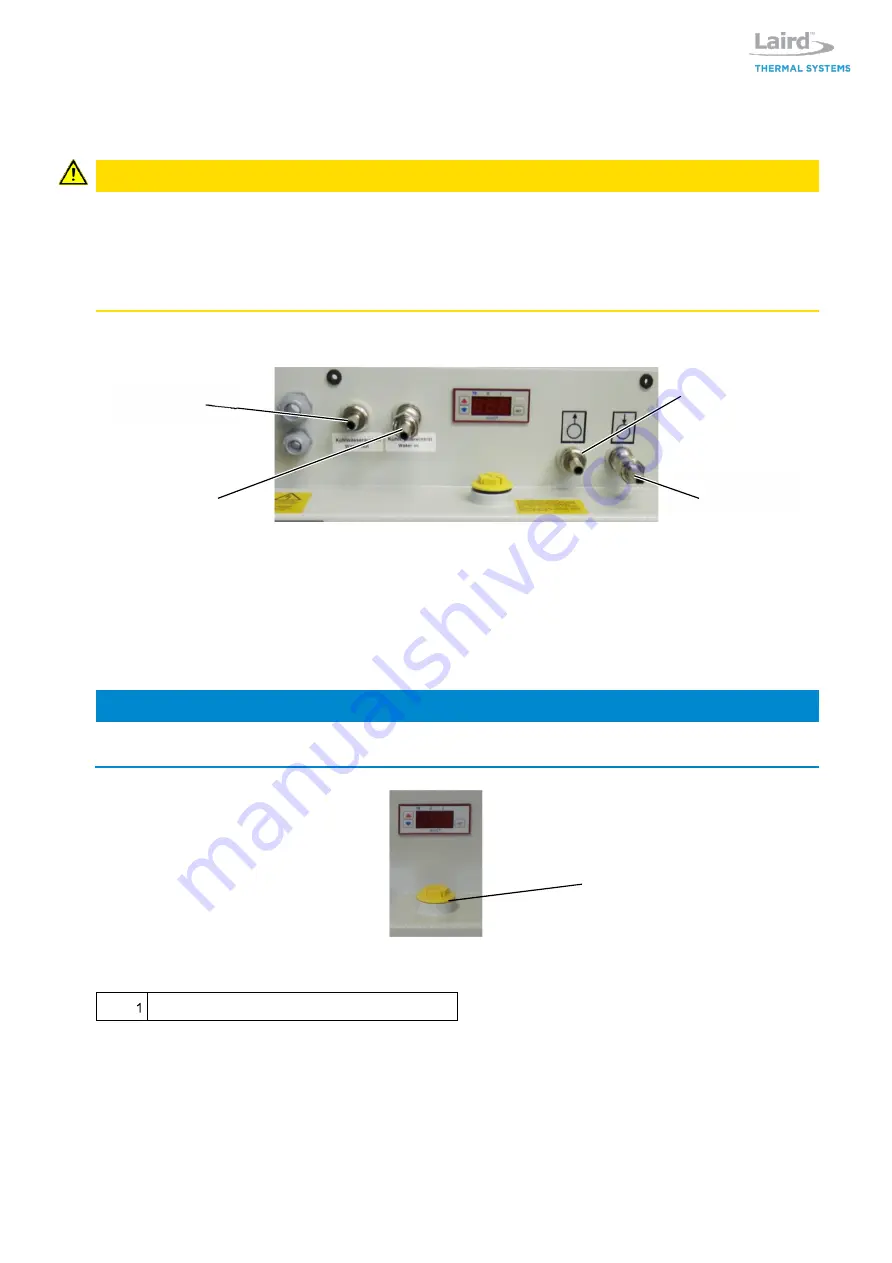
21
6.2.2
Cooling Circuit Connection and Filling
Risk of damage by using improper cooling hoses!
This may lead to damage to persons, damage to the unit or corrosion damage!
•
When choosing cooling hoses pay attention to sufficient burst strength and compatibility with coolant!
•
Only use cooling hoses without any signs of damage!
•
In case pure water is being used as coolant, ensure that non-transparent hoses are used to prevent the
growth of algae in the water. Otherwise appropriate additives must be used.
The cooling hoses with an internal diameter of 9 mm are connected to the unit by means of hose nipples.
Water outlet and water inlet are indicated with respective symbols.
Fig. 8:
Labelling of water inlet and water outlet
1)
Connect a suitable hose to the hose nipples for cooling water inlet and cooling water outlet and secure it
with a clamp, respectively.
2)
Connect a suitable hose to the hose nipples for coolant inlet and coolant outlet and secure it with a
clamp, respectively.
3)
Connect the hoses to the corresponding nipples of the device to be cooled.
When connecting the cooling hoses pay attention to flow direction. Follow the documentation released by
the manufacturer of the device to be cooled.
Fig. 9:
Cap of coolant container
CAUTION
Water supply
outlet
Coolant outlet
Water supply
inlet
Coolant inlet
PLEASE NOTE
1
Cap (version for transport is shown)