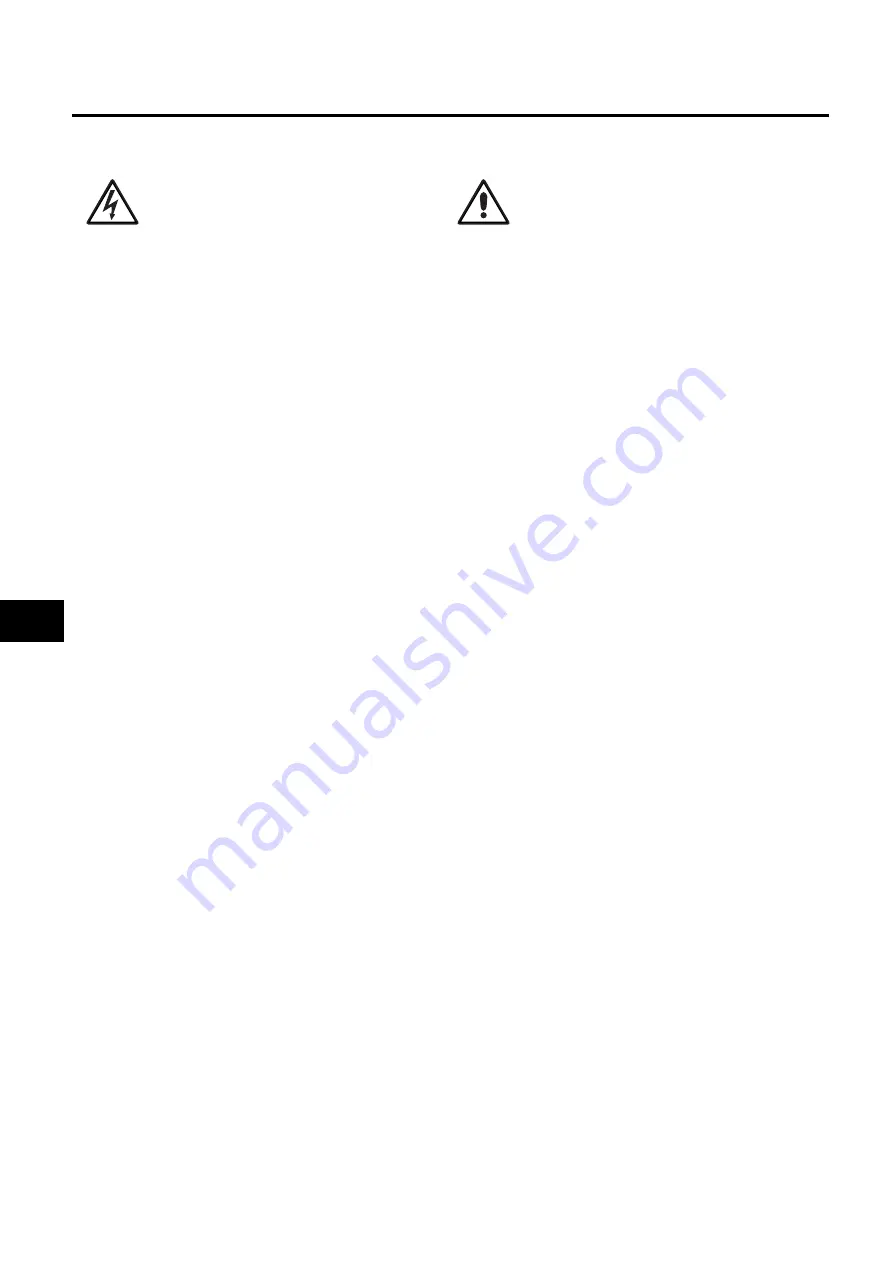
4
| HPI Combi Flow User Guide |
Version 3.11
www.lafert.com
1. Introduction
1.1. Important Safety Information
Please read the IMPORTANT SAFETY INFORMATION below, and all Warning and Caution information elsewhere.
Danger: Indicates a risk of electric shock, which,
if not avoided, could result in damage to the
equipment and possible injury or death.
This variable speed drive product (HP Combi Flow) is
intended for professional incorporation into complete
equipment or systems as part of a fixed installation. If
installed incorrectly it may present a safety hazard. The
HP Combi Flow uses high voltages and currents, carries a
high level of stored electrical energy, and is used to control
mechanical plant that may cause injury. Close attention
is required to system design and electrical installation to
avoid hazards in either normal operation or in the event
of equipment malfunction. Only qualified electricians are
allowed to install and maintain this product.
System design, installation, commissioning and
maintenance must be carried out only by personnel who
have the necessary training and experience. They must
carefully read this safety information and the instructions in
this Guide and follow all information regarding transport,
storage, installation and use of the HP Combi Flow,
including the specified environmental limitations.
Do not perform any flash test or voltage withstand test
on the HP Combi Flow. Any electrical measurements
required should be carried out with the HP Combi Flow
disconnected. Internal surge arrestors are fitted, intended
to protect against damage due to mains borne spikes,
which will result in the product failing the flash test.
Electric shock hazard! Disconnect and ISOLATE the HP
Combi Flow before attempting any work on it. High
voltages are present at the terminals and within the drive
for up to 10 minutes after disconnection of the electrical
supply. Always ensure by using a suitable multimeter that
no voltage is present on any drive power terminals prior to
commencing any work.
Where supply to the drive is through a plug and socket
connector, do not disconnect until 10 minutes have elapsed
after turning off the supply.
Ensure correct earthing connections and cable selection as
per defined by local legislation or codes. The drive may
have a leakage current of greater than 3.5mA; furthermore
the earth cable must be sufficient to carry the maximum
supply fault current which normally will be limited by the
fuses or MCB. Suitably rated fuses or MCB should be
fitted in the mains supply to the drive, according to any
local legislation or codes.
Do not carry out any work on the drive control cables
whilst power is applied to the drive or to the external
control circuits.
Danger: Indicates a potentially hazardous situation
other than electrical, which if not avoided, could
result in damage to property.
Within the European Union, all machinery in which this product is
used must comply with Directive 98/37/EC, Safety of Machinery.
In particular, the machine manufacturer is responsible for providing
a main switch and ensuring the electrical equipment complies with
EN60204-1.
The level of integrity offered by the HP Combi Flow control input
functions – for example stop/start, forward/reverse and maximum
speed, is not sufficient for use in safety-critical applications without
independent channels of protection. All applications where
malfunction could cause injury or loss of life must be subject to a risk
assessment and further protection provided where needed.
The driven motor can start at power up if the enable input signal is
present.
The STOP function does not remove potentially lethal high
voltages. ISOLATE the drive and wait 10 minutes before starting
any work on it. Never carry out any work on the Drive, Motor or
Motor cable whilst the input power is still applied.
Do not activate the automatic fault reset function on any systems
whereby this may cause a potentially dangerous situation.
IP55 drives can be installed in a pollution degree 2 environment.
IP66 outdoor drives can be installed in a pollution degree 4
environment.
HP Combi Flows are intended for indoor use only, useless
specifically stated as being suitable for installation outdoors and
installed in accordance with the Manufacturers guidelines.
When mounting the drive, ensure that sufficient cooling is provided.
Do not carry out drilling operations with the drive in place, dust
and swarf from drilling may lead to damage.
The entry of conductive or flammable foreign bodies should be
prevented. Flammable material should not be placed close to
the drive.
Relative humidity must be less than 95% (non-condensing).
Ensure that the supply voltage, frequency and 3 Phase Voltage
corresponds to the rating of the HP Combi Flow.
Never connect the mains power supply to the Output terminals U, V, W.
Do not install any type of automatic switchgear between the drive
and the motor. This may cause the drive protection to activate,
resulting in a trip and loss of operation.
Wherever control cabling is close to power cabling, maintain a
minimum separation of 100 mm and arrange crossings at 90 degrees.
Ensure that all terminals are tightened to the appropriate torque setting.
Do not attempt to carry out any repair of the HP Combi Flow. In
the case of suspected fault or malfunction, contact the Lafert Group
Technical Department for further assistance.
1
Intr
oduc
tion