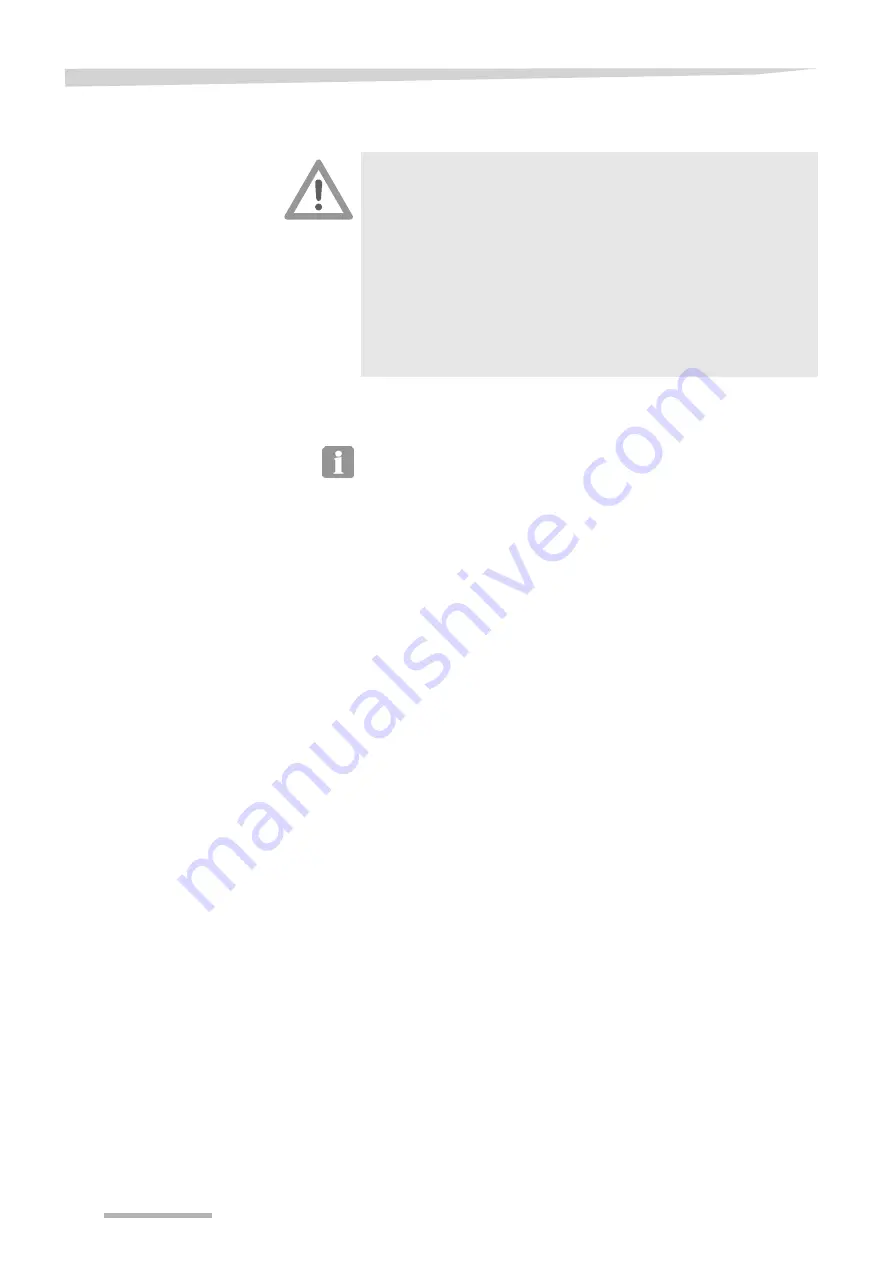
Security
28
Security
Uncoupling
Hydraulic system
The hydraulic system is pressurised.
When connecting the hydraulic system:
Ensure that the tractor/machine assembly are not pressurised.
Connect the hydraulic system, following the instructions in the user
manual.
Colour code sockets, so as to prevent incorrect connections
(inverting functions could cause an accident).
Before any intervention on the hydraulic system
Block the folding extensions hydraulically controlled accessories in
their rest position.
Reduce the pressure.
Stop the tractor engine.
Other instructions
Follow instructions
In addition to the instructions listed above, always obey:
•
Accident prevention regulations
•
generally recognised safety regulations, occupational health
requirements and road traffic regulations,
•
the notes that can be found in the user manual,
•
instructions for use, maintenance and servicing.
High risk of injury when uncoupling the machine.
Therefore :
Immobilise the tractor,
Never position yourself between the tractor and the machine
during uncoupling.
Slowly and carefully actuate the tractor’s hydraulic lift.
Make sure that the machine is on flat and sufficiently stable
ground.
Connect or disconnect hydraulic tubes, only if there is no
pressure in the tractor’s and machine’s hydraulic system.