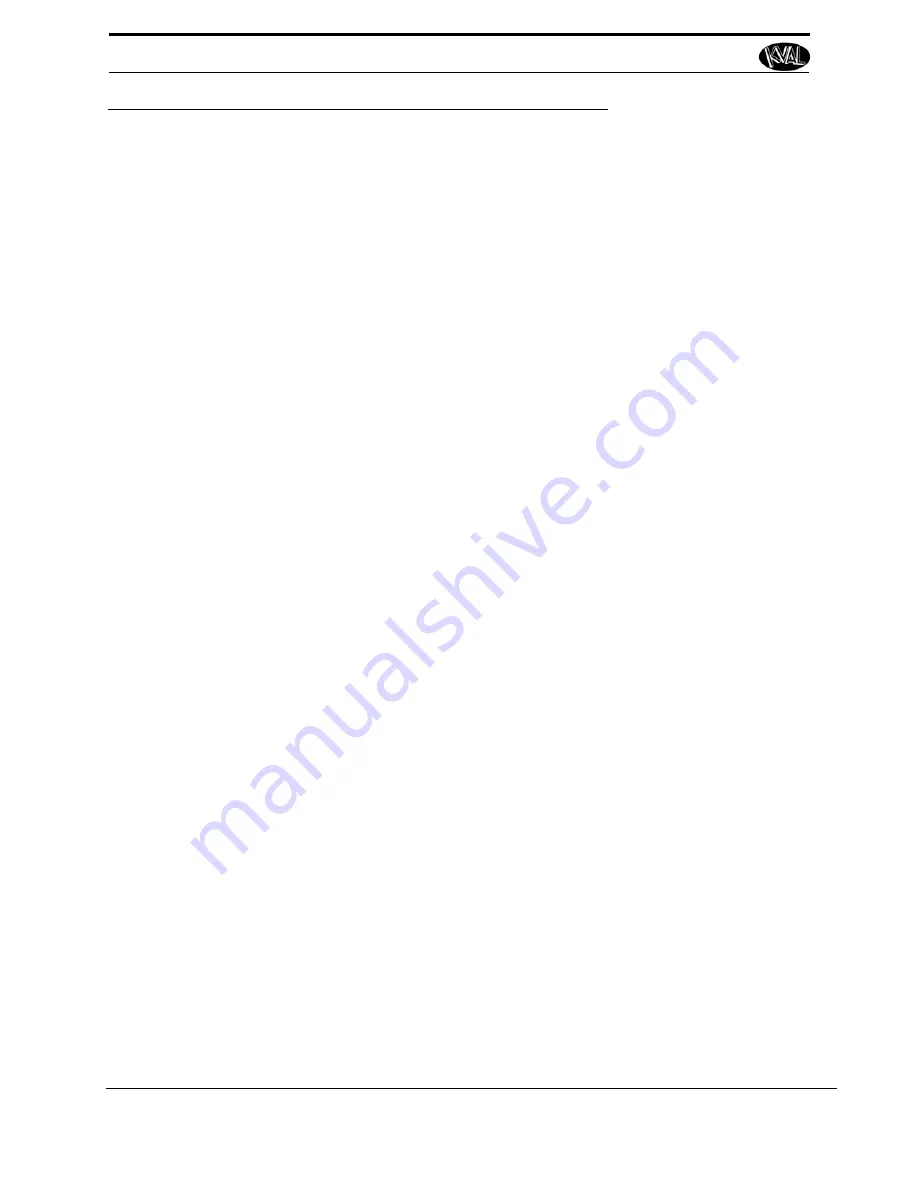
Zero-Energy to Start-Up
1-10
KVAL EP-1 Operation/Service Manual
Zero-Energy to Start-Up
Zero-Energy State to Start-Up to Operating State
Starting the equipment properly is just as important as the lockout/tagout guidelines in terms of
safety.
Start-up Guidelines
The following guidelines below should be followed to start the equipment.
Inspect
The equipment must be inspected for proper adjustment before starting equipment.
Clean Up
All materials and debris must be cleaned up. Any combustible materials or old parts
used during repairs must be cleaned up and/or properly disposed of.
Replace Guards
Replace all equipment guards. If part of equipment cannot be properly adjusted after
start-up with guard on, contact the KVAL Service team. See “Contacting KVAL” on
page 1-2.
Check Controls
Confirm that all switches are in the “OFF” position. Please be advised that some com-
ponents of the machine may start automatically when energy is restored.
Remove Locks
Each operator must remove his or her own lock and tag. This will ensure that all oper-
ators are in a safe place when the equipment is started.
Perform Visual Checks
If the equipment is too large to see all around it, station personnel around the area and
sound the personnel alarm before starting the equipment. If your operation is more
complex, your company’s comprehensive safety procedure may involve additional
steps. You will need to ask your supervisor about these procedures. The company’s
lockout procedure should be posted at each machine. On larger or long-term mainte-
nance or installation projects, the company’s procedures must be explained to all new
operators and a copy of the company’s procedures should be posted on-site for the
duration of the work.
The Company’s procedures should also include provisions for safely handling shift
changes and changes in operators or new operators.Comprehensive lockout/tagout
Summary of Contents for EP-1
Page 4: ...KVAL EP 1 Operation Service Manual ...
Page 20: ...Getting Help from KVAL 1 14 KVAL EP 1 Operation Service Manual Page Intentionally Left Blank ...
Page 22: ...Safety Sign Off Sheet 1 16 KVAL EP 1 Operation Service Manual ...
Page 38: ...How to Power Down the EP 1 2 16 KVAL EP 1 Operation Service Manual ...
Page 56: ...Troubleshooting the Air Cylinders 4 12 KVAL EP 1 Operation Service Manual ...