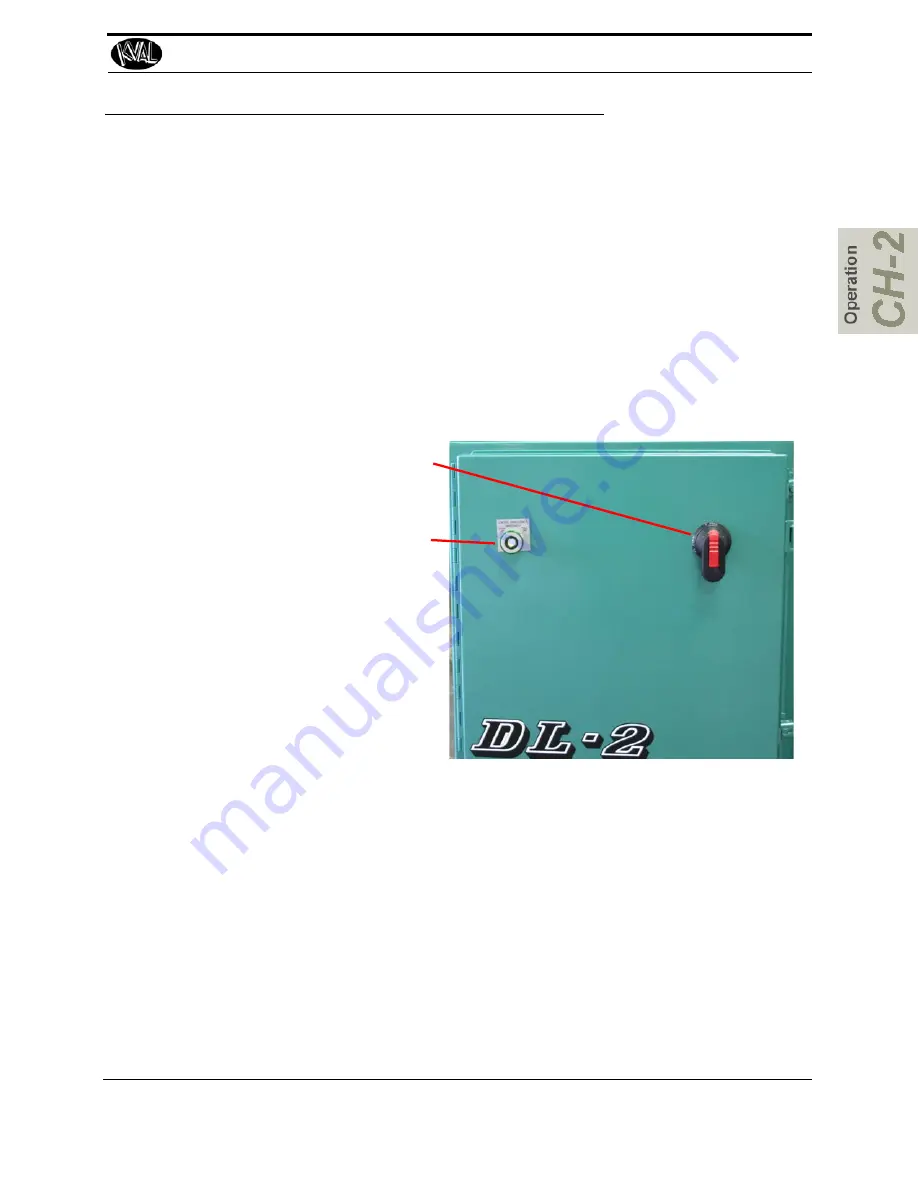
Powering Up and Down the DL-2
2-7
KVAL DL-2 Series Operation/Service Manual
Powering Up and Down the DL-2
This section describes how to power up and to power down the DL-2
Powering up the system includes:
• Applying power to the entire system.
• Starting the Control Circuit.
Powering down the system includes:
• Turning off the computer.
• Shutting down the control power.
• Removing power from the entire system.
To Power Up the DL-2
1.
Make sure the electrical discon-
nect the electrical cabinet is
turned to the ON position.
2.
Pull out the
CONTROL TRANS-
FORMER
switch.It should light
up along with the Control Power
light and the Overload Relay
light
The DL-2 is now ready for work.
Powering Down the DL-2
1.
Push in the CONTROL TRANSFORMER switch.
2.
. Kval also recommends that you turn the disconnect switch to OFF; this helps
reduce possible damage resulting from power surges from electrical storms.
Summary of Contents for DL-2
Page 4: ...KVAL DL 2 Operation Service Manual ...
Page 8: ...DL 2 Door Light Machine ...
Page 26: ...Safety Sign Off Sheet KVAL DL 2 Series Operation Service Manual 1 18 ...
Page 51: ...Using Templates 2 25 KVAL DL 2 Series Operation Service Manual ...
Page 62: ...Adjusting Drill Unit 3 11 KVAL DL 2 Series Operation Service Manual ...
Page 75: ...Troubleshooting with the Status Light Panel 4 13 KVAL DL 2 Series Operation Service Manual ...
Page 78: ...Notes ...
Page 79: ......