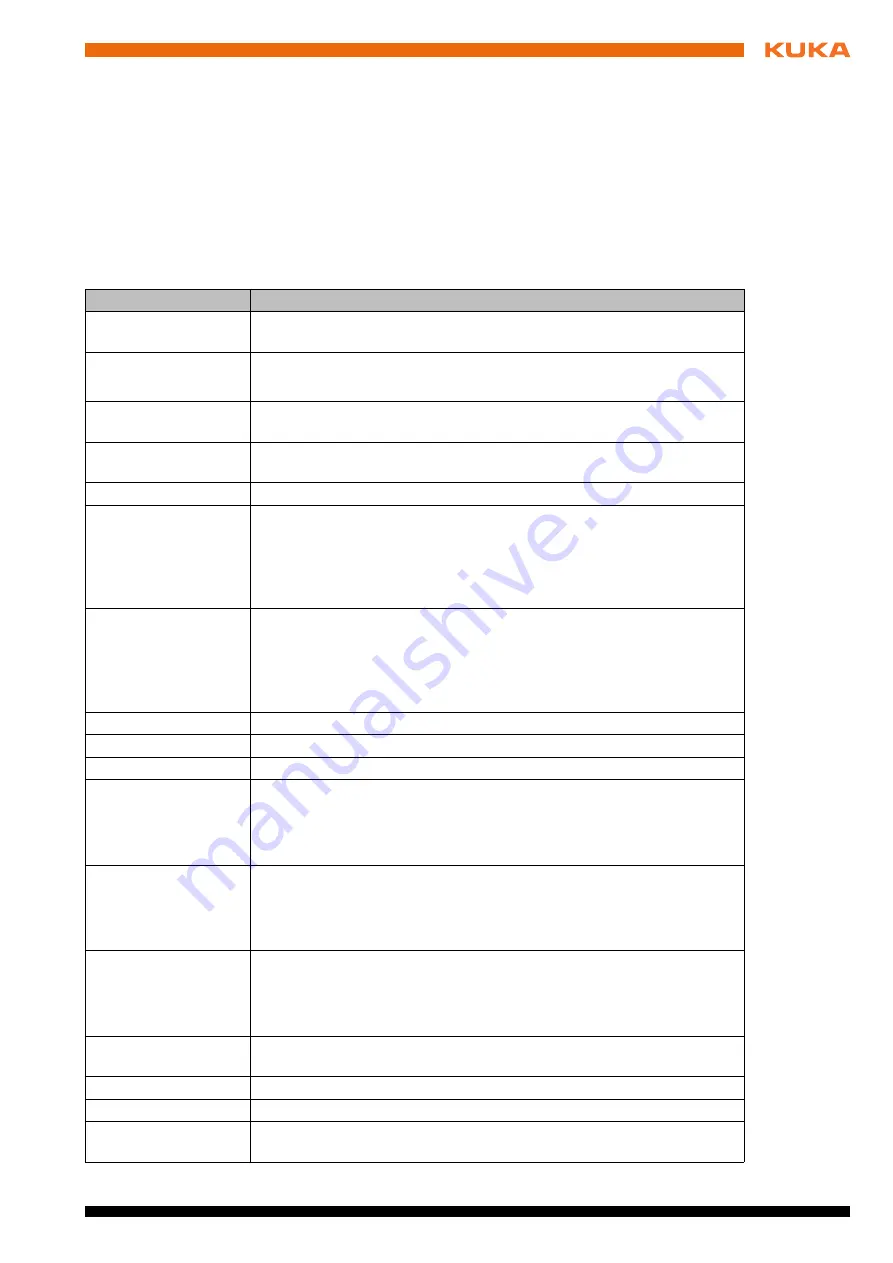
Issued: 28.03.2013 Version: MA KR AGILUS sixx V8 en (PDF)
5 Safety
has been incorporated into machinery, or has been assembled with other parts
to form machinery, and this machinery complies with the terms of the EC Ma-
chinery Directive, and the EC declaration of conformity is present in accor-
dance with Annex II A.
The declaration of incorporation, together with its annexes, remains with the
system integrator as an integral part of the technical documentation of the
complete machinery.
5.1.4
Terms used
Term
Description
Axis range
Range of each axis, in degrees or millimeters, within which it may move.
The axis range must be defined for each axis.
Stopping distance
Stopping distance = reaction di braking distance
The stopping distance is part of the danger zone.
Workspace
The manipulator is allowed to move within its workspace. The work-
space is derived from the individual axis ranges.
Operator
(User)
The user of the industrial robot can be the management, employer or
delegated person responsible for use of the industrial robot.
Danger zone
The danger zone consists of the workspace and the stopping distances.
Service life
The service life of a safety-relevant component begins at the time of
delivery of the component to the customer.
The service life is not affected by whether the component is used in a
robot controller or elsewhere or not, as safety-relevant components are
also subject to ageing during storage.
KCP
The KCP (KUKA Control Panel) teach pendant has all the operator con-
trol and display functions required for operating and programming the
industrial robot.
The KCP variant for the KR C4 is called KUKA smartPAD. The general
term “KCP”, however, is generally used in this documentation.
KUKA smartPAD
See KCP
Manipulator
The robot arm and the associated electrical installations
Safety zone
The safety zone is situated outside the danger zone.
Stop category 0
The drives are deactivated immediately and the brakes are applied. The
manipulator and any external axes (optional) perform path-oriented
braking.
Note:
This stop category is called STOP 0 in this document.
Stop category 1
The manipulator and any external axes (optional) perform path-main-
taining braking. The drives are deactivated after 1 s and the brakes are
applied.
Note:
This stop category is called STOP 1 in this document.
Stop category 2
The drives are not deactivated and the brakes are not applied. The
manipulator and any external axes (optional) are braked with a normal
braking ramp.
Note:
This stop category is called STOP 2 in this document.
System integrator
(plant integrator)
System integrators are people who safely integrate the industrial robot
into a complete system and commission it.
T1
Test mode, Manual Reduced Velocity (<= 250 mm/s)
T2
Test mode, Manual High Velocity (> 250 mm/s permissible)
External axis
Motion axis which is not part of the manipulator but which is controlled
using the robot controller, e.g. KUKA linear unit, turn-tilt table, Posiflex.
Summary of Contents for KR AGILUS sixx
Page 6: ...6 141 Issued 28 03 2013 Version MA KR AGILUS sixx V8 en PDF KR AGILUS sixx...
Page 10: ...10 141 Issued 28 03 2013 Version MA KR AGILUS sixx V8 en PDF KR AGILUS sixx...
Page 14: ...14 141 Issued 28 03 2013 Version MA KR AGILUS sixx V8 en PDF KR AGILUS sixx...
Page 86: ...86 141 Issued 28 03 2013 Version MA KR AGILUS sixx V8 en PDF KR AGILUS sixx...
Page 130: ...130 141 Issued 28 03 2013 Version MA KR AGILUS sixx V8 en PDF KR AGILUS sixx...
Page 138: ...138 141 Issued 28 03 2013 Version MA KR AGILUS sixx V8 en PDF KR AGILUS sixx...
Page 141: ...141 141 Issued 28 03 2013 Version MA KR AGILUS sixx V8 en PDF KR AGILUS sixx...