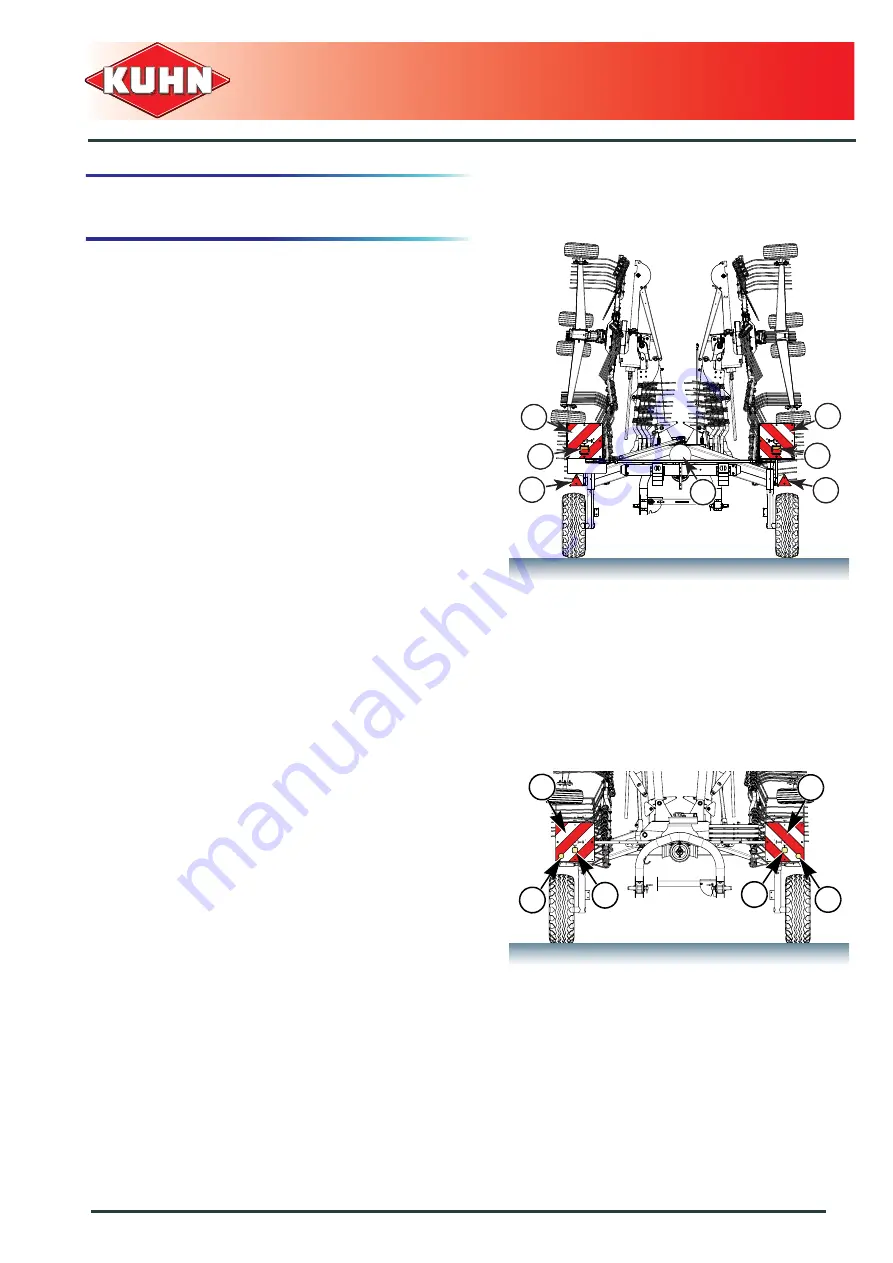
Safety
Gyrorake
GA8121
21
KN202BGB F
4. Road safety equipment and
recommendations
The road safety equipment is mounted in the factory or
by your authorized Kuhn dealer according to current
safety regulations.
- Always keep to the legal speed limit for driving a
tractor-machine assembly on public roads.
Whatever the speed, we recommend, for everyones'
safety, not to exceed a maximum speed
of 40 km/h (25 mph).
The rear device is made up of the following components:
• 2 signalling panels (1).
• 2 signalling lights (2) (red light / stop light / turn
signal light).
• 2 red reflectors (3).
• A speed limit decal (4) supplied according to the
country where the machine is bound for.
The front device is made up of the following components:
• 2 signalling panels (1).
• 2 white lights (2).
• 2 white reflectors (3).
3
3
1
1
2
2
1
4
2
3
1
2
3