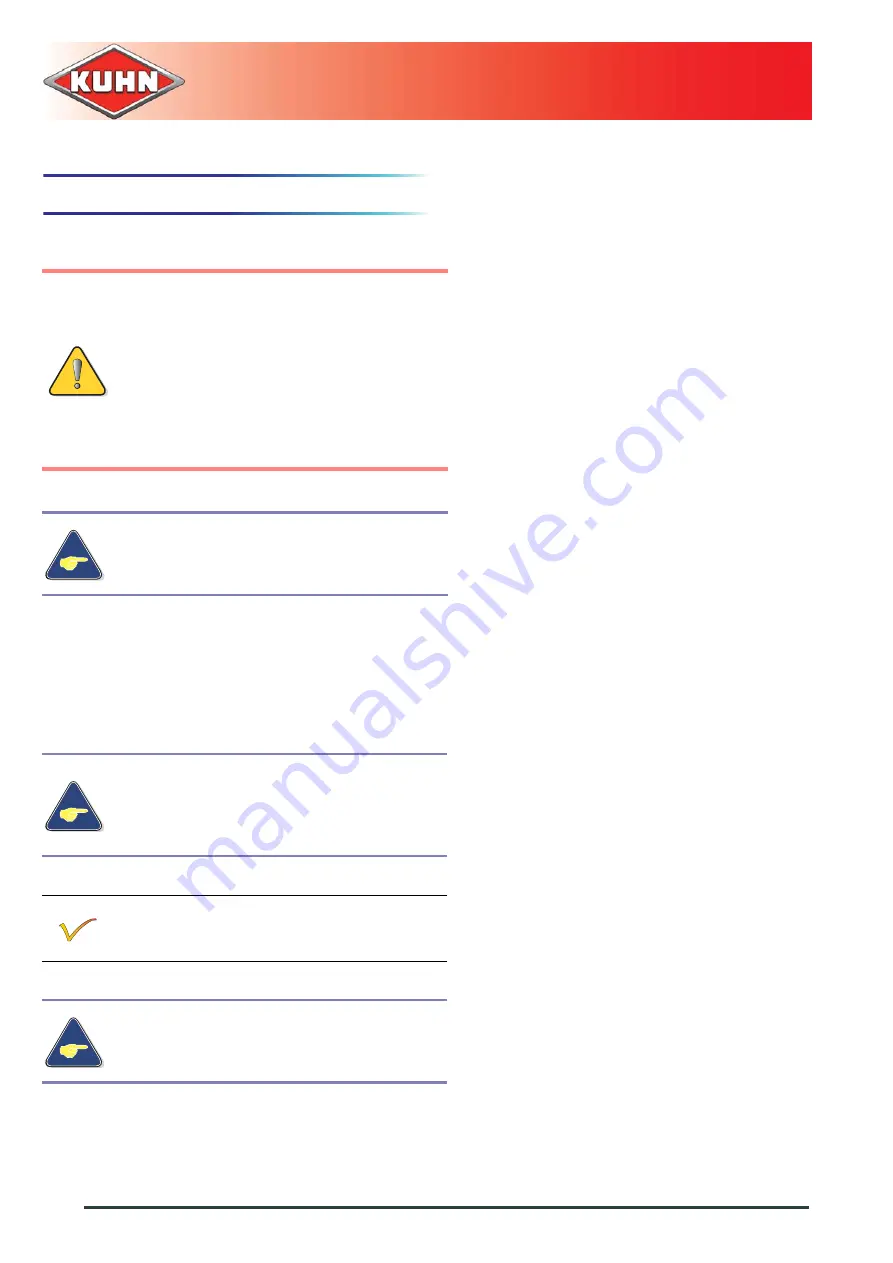
EL162
74
8. - Instructions for work
KN146AGB_L
Cultiplow
8.3
Machine use
Before engaging the machine in the ground:
- Engage the tractor pto and gradually increase the
speed up to 540/750/min or 1000 min(Depending
on the tractor pto speed).
- Wait until this rotation speed is reached.
Before engaging the machine in the ground:
- Check that nobody is within the machine
pivoting area.
- If there is someone, make sure the person
moves away.
- Pay particular attention if working on very
uneven grounds.
- Only work in straight lines. Lift the machine
to turn.
Engaging the machine in the ground before
engaging the tractor PTO can lead to
excessive power requirement and trigger the
torque limiter.
- Determine groundspeed/engine speed ratio
that is best suited to the work conditions.
- Check blade condition before each use or
immediately after hitting an obstacle.
Summary of Contents for EL162
Page 2: ......