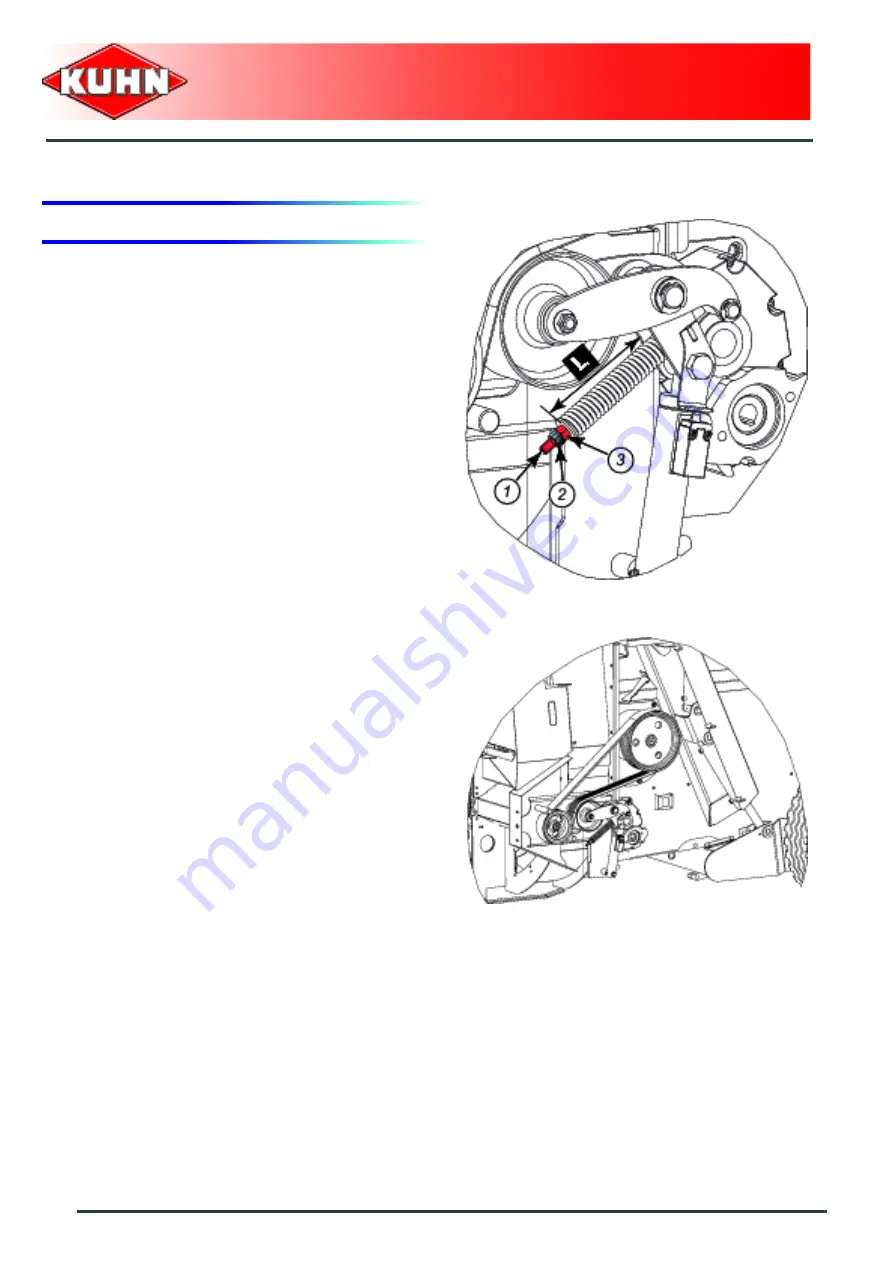
Silo unloader - Straw spreader - Mixer - Distributor
82
ATHENOR 6070
Maintenance and storage
7. Belt tension
In order to guarantee optimal operation, belt tension
must be checked and adjusted if necessary every 100
hours (or more often in case of frequent feeding with
tough products).
The belt tension is adjusted using the screw rod (1) nut
(2) and check nut (3).
In the engaged position, the spring tension must be set
to L = 180 mm (0’7’’) (length of compressed spring).
Left side drive (lower bale separator)
Summary of Contents for ATHENOR 6070
Page 2: ......
Page 19: ...Safety Silo unloader Straw spreader Mixer Distributor ATHENOR 6070 17 ...
Page 94: ...Silo unloader Straw spreader Mixer Distributor 92 ATHENOR 6070 Trouble shooting guide ...
Page 97: ......
Page 98: ......