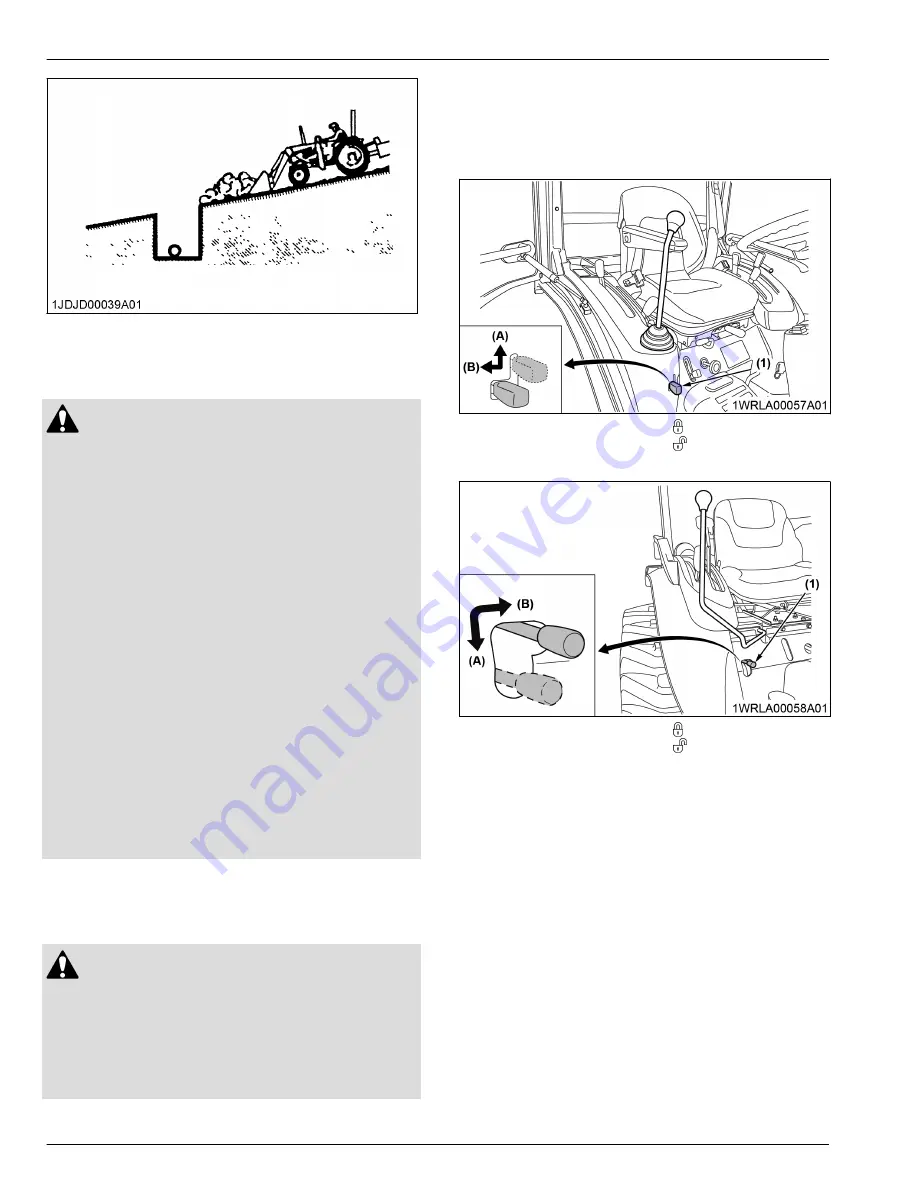
10. Precautions for handling large
heavy objects
DANGER
To avoid personal injury or death:
• Handling large, heavy objects can be dangerous
due to the following reasons.
– Danger of rolling the tractor over
– Danger of upending the tractor
– Danger of the object rolling or sliding down
the loader boom onto the operator
• If you must handle large, heavy objects, protect
yourself by the following methods.
– Do not lift load higher than necessary to
clear the ground when the tractor is moving
– Add rear ballast to the tractor to
compensate for the load
– Do not lift large objects with equipment not
equipped an anti-rollback device
– Move the machine slowly and carefully
– Avoid rough terrain
– Keep the transport distance as short as
possible and carry the load as low as
possible during transport
– Make sure that the loader and the bucket are
at proper height and have stopped moving
before transport
VALVE LOCK
The control valve is equipped with a valve lock.
WARNING
To avoid personal injury or death from crushing:
• Do not utilize the valve lock for machine
maintenance or repair.
• The valve lock is to prevent accidental actuation
when implement is not in use or during
transport.
The control valve can be locked when the loader
control lever is in the
“Neutral”
position.
The lock is not intended to, and will not, prevent a leak
down of the implement during the period of storage.
[CAB]
(1) Lock lever
(A)
Lock
(B)
Unlock
[ROPS]
(1) Lock lever
(A)
Lock
(B)
Unlock
FRONT REMOTE HYDRAULIC
CONTROL SYSTEM (IF
EQUIPPED)
This system can be used for a front mounted hydraulic
implement, as it provides hydraulic oil to the front outlet
directly.
1. Installing the hydraulic quick
coupler
1. Remove the cap from the front hydraulic outlet.
OPERATING THE LOADER
TECHNIQUES FOR OPERATING THE LOADER AND THE TRACTOR
28
LA535
Summary of Contents for LA535
Page 4: ......
Page 10: ...SAFETY LABELS SAFE OPERATION 6 LA535 ...
Page 11: ...SAFE OPERATION LA535 7 ...
Page 57: ... A Top of bolt B Length REINSTALLING THE LOADER LA535 53 ...