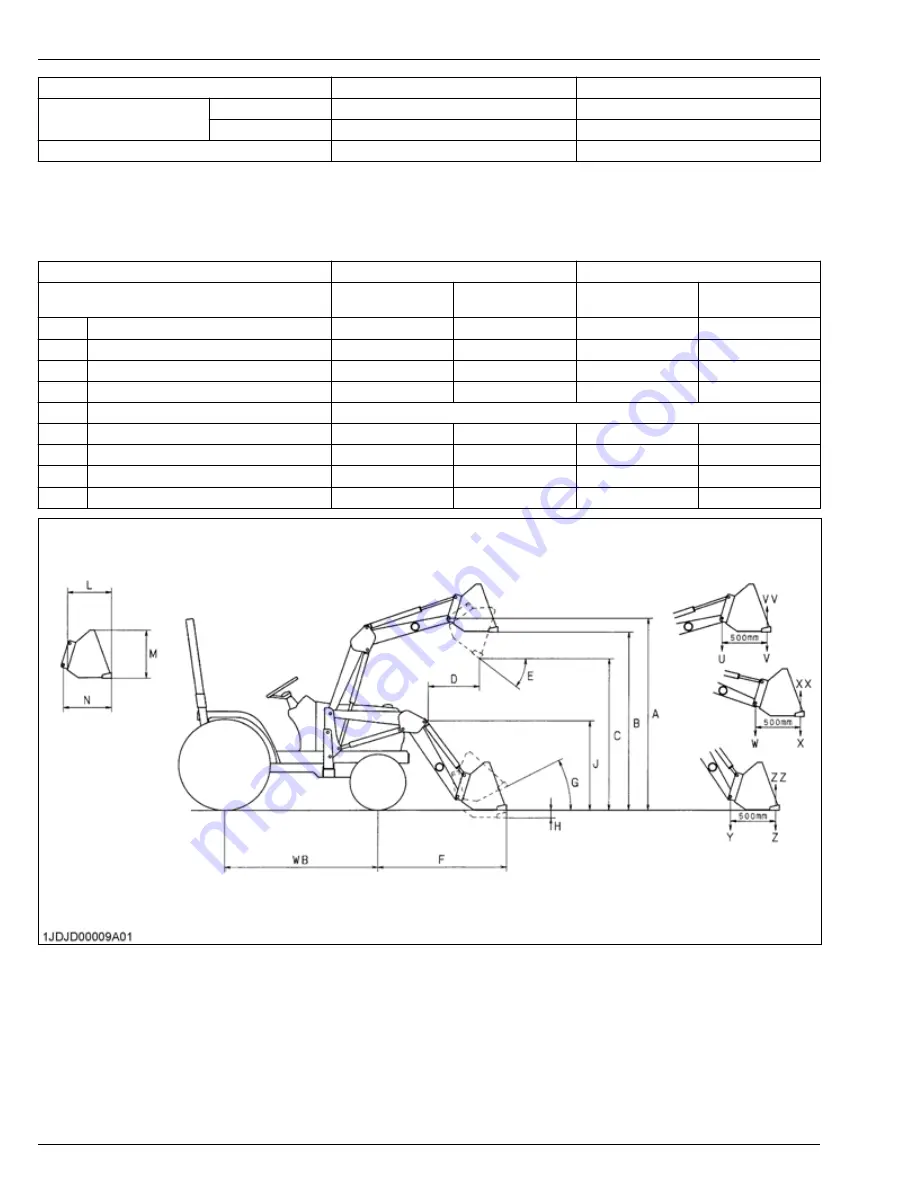
Loader model
LA344
LA344S
Capacity
Struck
0.14 m
3
(4.9 cu.ft.)
0.13 m
3
(4.6 cu.ft.)
Heaped
0.17 m
3
(6.0 cu.ft.)
0.17 m
3
(6.0 cu.ft.)
Weight
60 kg (132 lbs)
56 kg (123 lbs)
3. Dimensional specifications
Loader model
LA344
LA344S
Tractor model
BX1880
BX2380, BX2680,
and BX23S
BX1880
BX2380, BX2680,
and BX23S
A
Maximum lift height (to bucket pivot pin)
1795 mm (70.7 in.)
1804 mm (71.0 in.)
1795 mm (70.7 in.)
1804 mm (71.0 in.)
B
Maximum. lift height under level bucket
1652 mm (65.0 in.)
1662 mm (65.4 in.)
1654 mm (65.1 in.)
1664 mm (65.5 in.)
C
Clearance with bucket dumped
1316 mm (51.8 in.)
1323 mm (52.1 in.)
1281 mm (50.4 in.)
1288 mm (50.7 in.)
D
Reach at max. lift height (dumping reach)
642 mm (25.3 in.)
646 mm (25.4 in.)
673 mm (26.5 in.)
677 mm (26.5 in.)
E
Maximum dump angle
0.79 rad (45°)
F
Reach with bucket on ground
1398 mm (55.0 in.)
1392 mm (54.8 in.)
1445 mm (56.9 in.)
1438 mm (56.6 in.)
G
Bucket roll-back angle
0.52 rad (30°)
0.51 rad (29°)
0.52 rad (30°)
0.51 rad (29°)
H
Digging depth
134 mm (5.3 in.)
125 mm (4.9 in.)
132 mm (38.6 in.)
122 mm (4.8 in.)
J
Overall height in carrying position
981 mm (38.6 in.)
990 mm (39.0 in.)
981 mm (38.6 in.)
990 mm (39.0 in.)
1. INFORMATION
SPECIFICATIONS
3.Dimensional specifications
1-12
LA344, LA344S
KiSC issued 02, 2017 A
Summary of Contents for LA344
Page 1: ...LA344 LA344S WORKSHOP MANUAL FRONT LOADER KiSC issued 02 2017 A ...
Page 5: ...1 INFORMATION KiSC issued 02 2017 A ...
Page 9: ...1 INFORMATION SAFETY FIRST 1 4 LA344 LA344S KiSC issued 02 2017 A ...
Page 11: ...1 INFORMATION SAFETY DECALS 1 6 LA344 LA344S KiSC issued 02 2017 A ...
Page 12: ...SAFETY DECALS 1 INFORMATION LA344 LA344S 1 7 KiSC issued 02 2017 A ...
Page 15: ...1 INFORMATION TERMINOLOGY 1 10 LA344 LA344S KiSC issued 02 2017 A ...
Page 20: ...2 GENERAL KiSC issued 02 2017 A ...
Page 22: ...2 GENERAL IDENTIFICATION 2 2 LA344 LA344S KiSC issued 02 2017 A ...
Page 24: ...2 GENERAL 2 4 LA344 LA344S KiSC issued 02 2017 A ...
Page 26: ...2 GENERAL LUBRICATING SYSTEM 2 6 LA344 LA344S KiSC issued 02 2017 A ...
Page 30: ...2 GENERAL TIGHTENING TORQUES 5 Hydraulic fittings 2 10 LA344 LA344S KiSC issued 02 2017 A ...
Page 32: ...2 GENERAL MAINTENANCE CHECK LIST 2 12 LA344 LA344S KiSC issued 02 2017 A ...
Page 36: ...2 GENERAL SPECIAL TOOLS 1 Special tools for loader 2 16 LA344 LA344S KiSC issued 02 2017 A ...
Page 37: ...3 FRONT LOADER KiSC issued 02 2017 A ...
Page 71: ...3 FRONT LOADER SERVICING 5 Servicing 3 34 LA344 LA344S KiSC issued 02 2017 A ...