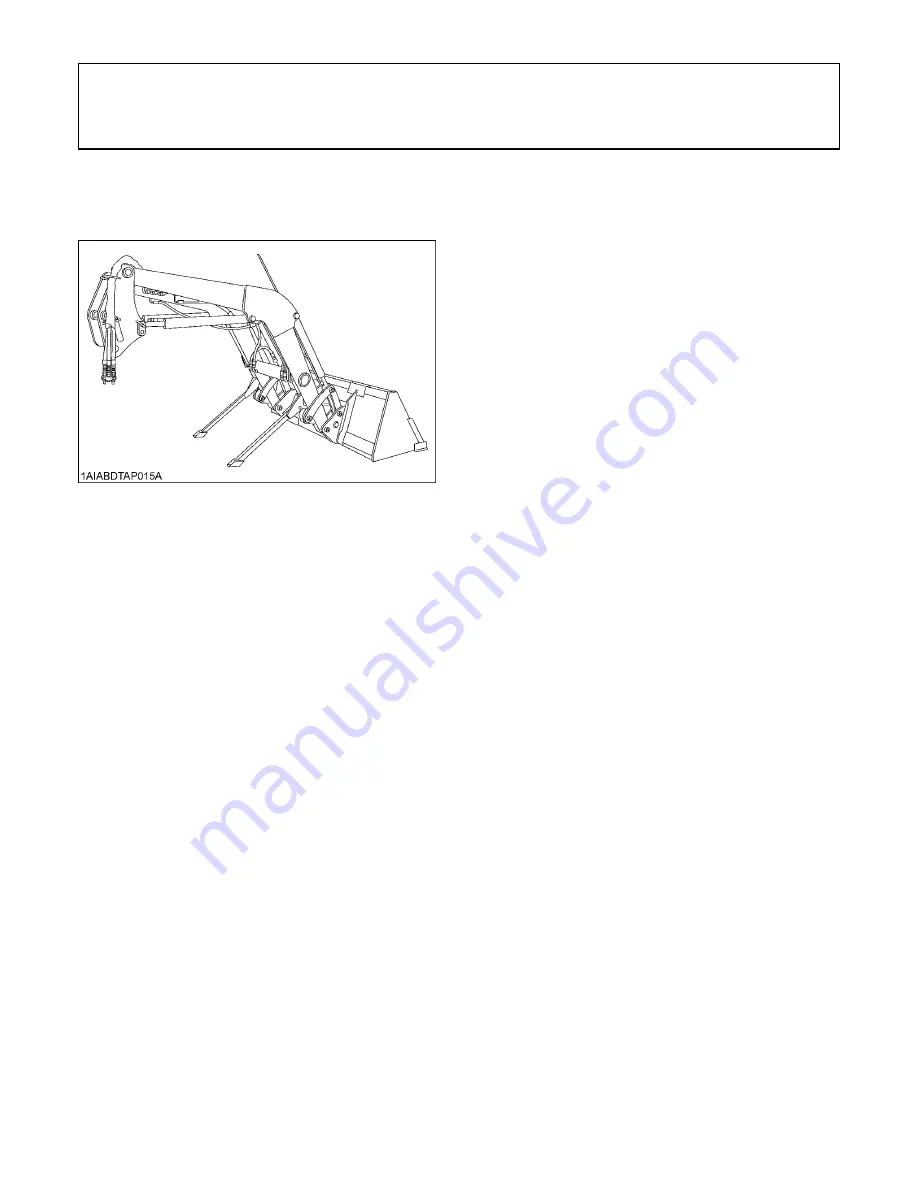
37
STORING THE LOADER
STORING THE LOADER
1. Store the loader in a clean dry place.
2. Make sure the loader is properly supported.
3. Attach the protective plugs and caps to the couplers to
protect them from dust.
4. Check all hydraulic hoses and connections. Repair or
replace them if necessary.
5. Repair or replace any worn, damaged or missing
parts.
6. Lubricate loader as described in "LUBRICATION" in
Maintenance section.
7. Apply a coat of grease to all exposed cylinder rods and
mounting pins to prevent rust.
8. Repaint worn or scratched parts.
Summary of Contents for LA1954
Page 1: ......
Page 2: ...California Proposition 65 Cancer and Reproductive Harm www P65Warnings ca gov WARNING ...
Page 8: ...3 SAFE OPERATION DANGER WARNING AND CAUTION LABELS ...
Page 9: ...SAFE OPERATION 4 ...
Page 11: ......
Page 17: ...6 SPECIFICATIONS LA1954 For greatest power For greatest lift ...
Page 18: ...7 SPECIFICATIONS LA2254 For greatest power For greatest lift ...
Page 50: ...ABBREVIATION LIST ...