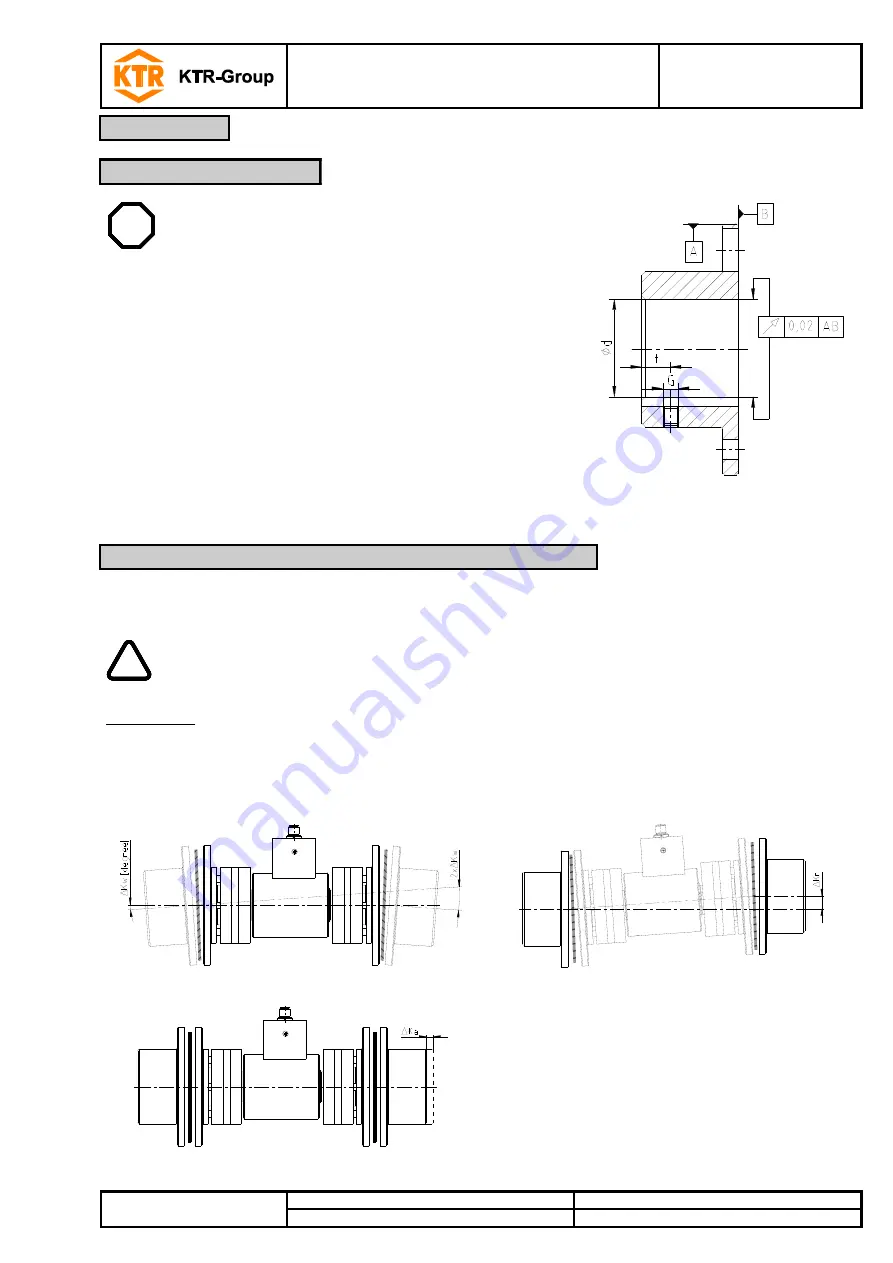
DATAFLEX
®
110/...
Torque Measuring Shaft
Operating/Assembly instructions
KTR-N
Sheet:
Edition:
49018 EN
8 of 22
1
Please observe protection
note ISO 16016.
Drawn:
2017-08-02 Pz/Da
Replacing:
---
Verified:
2017-08-03 Pz
Replaced by:
STOP
The maximum permissible bore diameters d
1max
and
d
2max
(see RADEX
®
-N catalogue) must not be
exceeded. If these figures are disregarded, the
coupling may tear. Rotating particles may cause
danger to life.
•
Hub bores machined by the customer have to observe
concentricity or axial runout, respectively (see
illustration 4).
•
Please make absolutely sure to observe the figures
for Ø d
1max
and Ø d
2max
.
•
Carefully align the hubs when the finish bores are
drilled.
•
Please provide for a setscrew according to
DIN EN ISO 4029 with a cup point or an end plate to
fasten the hubs axially.
Illustration 4: Concentricity and axial runout
The displacement figures specified in table 4 provide for sufficient safety to compensate for external influences
like, for example, thermal expansion or foundation settling.
!
In order to ensure a long service life of the measuring shaft, the shaft ends have to be
accurately aligned. Please absolutely observe the displacement figures specified (see
table 4). If the figures are exceeded, the measuring shaft with coupling will be damaged.
Please note:
•
The displacement figures specified in table 4 are maximum figures which must not arise in parallel. If radial,
axial and angular displacement arises at the same time, these values must be reduced (see illustration 6).
•
Please inspect with a dial gauge, ruler or feeler gauge whether the permissible displacement figures specified
in table 4 can be observed.
Angular displacement
Radial displacement
Illustration 5: Displacements
Axial displacement
4
Assembly
4.2 Advice for finish bore
4.3 Displacements - alignment of the torque measuring shaft