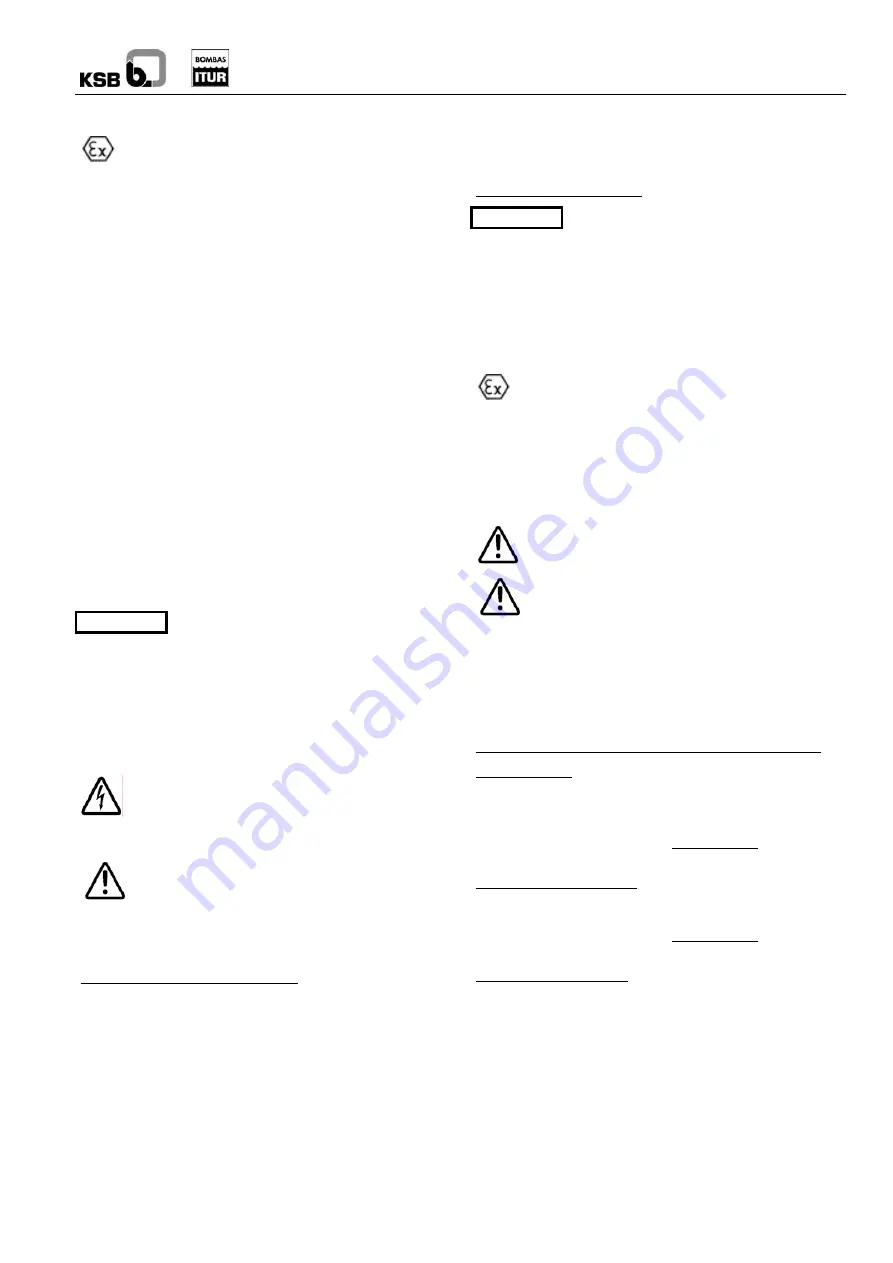
RWCP, RWCN
11
6.2.4
Temperature of the liquid to be pumped
The power absorbed by the pump increases with the
viscosity of the impelled liquid. In order to prevent
overloading in the motor, pump and coupling, this viscosity
must not exceed that shown in the order and in the ATEX
declaration of conformity.
6.2.5
Maximum pump speed
In order to protect the pump from over speed, the maximum
rotation speed shall be that shown on the name plate
engraved in the pump- If the speed shall not be indicated in
the name plate it is necessary to consult with KSB ITUR.
If eventually it would be wished to perform the pump at higher
speed, it is necessary to consult with KSB ITUR.
6.3
Starting up after storage
If the storage and/or standstill of the pump has been for a
prolonged period of time (over 6 months), it is necessary to:
-
Check the state of the joints.
-
Check the levelling.
-
Check all the auxiliary connections.
-
Renew the lubrication of the bearings (where fitted).
-
Change the packing (when fitted)
-
After a short storage period, simply turn the pump shaft
manually to unlock the rotor equipment.
-
Follow the specific post-storage instructions in the motor
manuals and other items.
-
Observe all the steps shown in the "Start-up" section.
If the equipment is going to be in shutdown
for a certain period of time and there is the
possibility of freezing temperatures, it is necessary to
completely drain the pump in order to prevent any
deterioration from the freezing of the contained fluid.
7 Maintenance/Conservation
7.1 General
instructions
Before dismounting, ensure that:
The motor cannot be operated accidentally, by
disconnecting from the electricity supply (e.g.
removing cut-outs, unplugging, disconnecting the
automatic circuit breaker, etc) or the start-up batteries
(disconnect operating energy).
The pump is free of pumped fluid, cleaning it
internally with appropriate liquid whenever it is a
hazardous fluid (hot, contaminant, inflammable,…)
7.2 Maintenance/inspection
7.2.1 Checking
instructions
During the first minutes of operation:
In cases of mechanical seal
-
There may be a brief large leak during start up. Should
this leak persist, shutdown the group and determine the
cause. The causes may be, amongst others, dirt in the
pumped area or dry operation due to incomplete
discharge of the pump air.
In cases of packing:
-
There is no leak; immediately loosen the packing gland
until a small dripping is achieved.
-
Excessive fluid leak; leave to settle for 10 minutes; tighten
the packing gland by turning 1/6th and leaving for 5
minutes. Repeat the process until between 20 and 60
drops per minute are achieved.
After a few hours operation:
Check the bearing temperature at the point in
the bearing location area. Normal
temperature can reach up to 40°C above environmental
temperature, but must never exceed 90°C.
Note
Observe the possible anomalies shown in point 8 of this
manual.
The reserve pumps should be started up and shutdwon once
a week, in order to ensure they are always in service
conditions.
The failure of one or both sides of the seal may lead to
excess heating. This can be corrected by following the
instructions of the seal manufacturer, both with regards to its
assembly and the maintenance of the auxiliary seal devices,
where appropriate. Alternatively, the pump may be fitted with a
surveillance device if the purchaser has so specified.
7.2.2 Lubrication
Before lubricating the pump, ensure that
The pump is stopped and cannot be started up
accidentally.
The bearing support temperature is less than 40ºC,
in order to prevent burns to hands. To do this,
measure the temperature with a thermocouple.
The absence of grease in the bearing support may lead to a
lack of lubrication of the lip seals, which will come into dry
contact with the shaft. This contact may lead to a high shaft
temperature which might cause ignition. To prevent this,
regularly check the grease level in the bearings support.
BEARINGS:
Lubricated with grease. PUMP WITH GREASE NIPPLES:
1
st
re-lubrication
The pump leaves the factory with the bearings greased for
approximately 1000 hours of operation. After this time (or one
year, whatever may occur first) proceed to first re-lubrication.
Check re-lubrication quantity in each greaser in the attached
chart
Subsequent re-lubrications
The periodicity for subsequent re-lubrications should be 2000
hours of operation or once a year (whatever may occur first).
Check re-lubrication quantity in each greaser in the attached
chart
Grease change (re-filling)
Change grease after aprox. 8000 hours of operation or once
every two years (whatever may occur first).
For complete grease change it is necessary first to dismantle
the bearings and carefully clean their positions in the support
in order to remove old grease.
Afterwards proceed to re-filling of grease up to aprox. 75% of
the free space in the bearing and aprox 40% of the free space
at bearing cover. See approx. re-filling quantity in the attached
chart.
Note