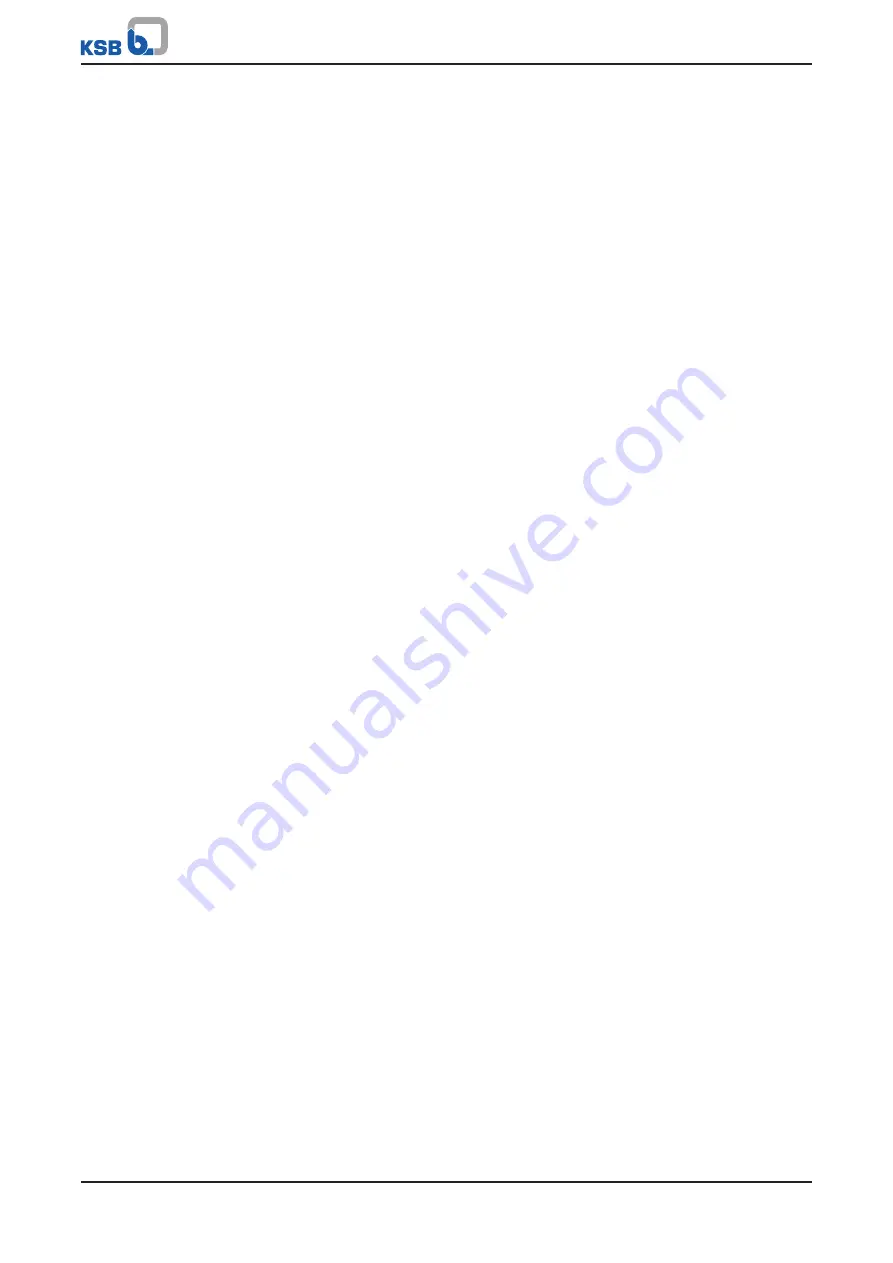
2 Safety
8 of 40
BOA-H Mat P
▪
In the case of customised special variants, further restrictions may apply with
regard to the operating mode and service life. Refer to the relevant sales
documentation for applicable limitations.
▪
The operator is responsible for ensuring compliance with all local regulations not
taken into account.
▪
The operator is responsible for any eventualities or incidents which may occur
during installation performed by the customer, operation and maintenance.
2.3 Intended use
▪
Only operate valves and actuators which are in perfect technical condition.
▪
Do not operate partially assembled valves or actuators.
▪
Only use the valve for fluids specified in the product literature. Take the design
and material variant into account.
▪
Only operate the valve within the operating limits described in the other
applicable documents.
▪
Only operate the actuator within the permissible ambient temperature limits.
▪
Consult the manufacturer about any other modes of operation not described in
the product literature.
▪
Do not use the valve or actuator as a foothold.
2.3.1 Prevention of foreseeable misuse
▪
Never exceed the permissible application and operating limits specified in the
product literature regarding pressure, temperature, etc.
▪
Observe all safety information and instructions in this manual.
2.4 Personnel qualification and training
▪
All personnel involved must be fully qualified to transport, install, operate,
maintain and inspect the product this manual refers to and be fully aware of the
interaction between the valve and the system.
▪
The responsibilities, competence and supervision of all personnel involved in
transport, installation, operation, maintenance and inspection must be clearly
defined by the operator.
▪
Deficits in knowledge must be rectified by means of training and instruction
provided by sufficiently trained specialist personnel. If required, the operator can
commission the manufacturer/supplier to train the personnel.
▪
Hands-on training at the valve and the actuator must always be supervised by
specialist technical personnel.
2.5 Consequences and risks caused by non-compliance with this manual
▪
Non-compliance with these operating instructions will lead to forfeiture of
warranty cover and of any and all rights to claims for damages.
▪
Non-compliance can, for example, have the following consequences:
– Hazards to persons due to electrical, thermal, mechanical and chemical
effects and explosions
– Failure of important product functions
– Failure of prescribed maintenance and servicing practices
– Hazard to the environment due to leakage of hazardous substances
Summary of Contents for BOA-CVP H
Page 1: ...Automated Globe Valves BOA H Mat P Installation Operating Manual...
Page 38: ......
Page 39: ......