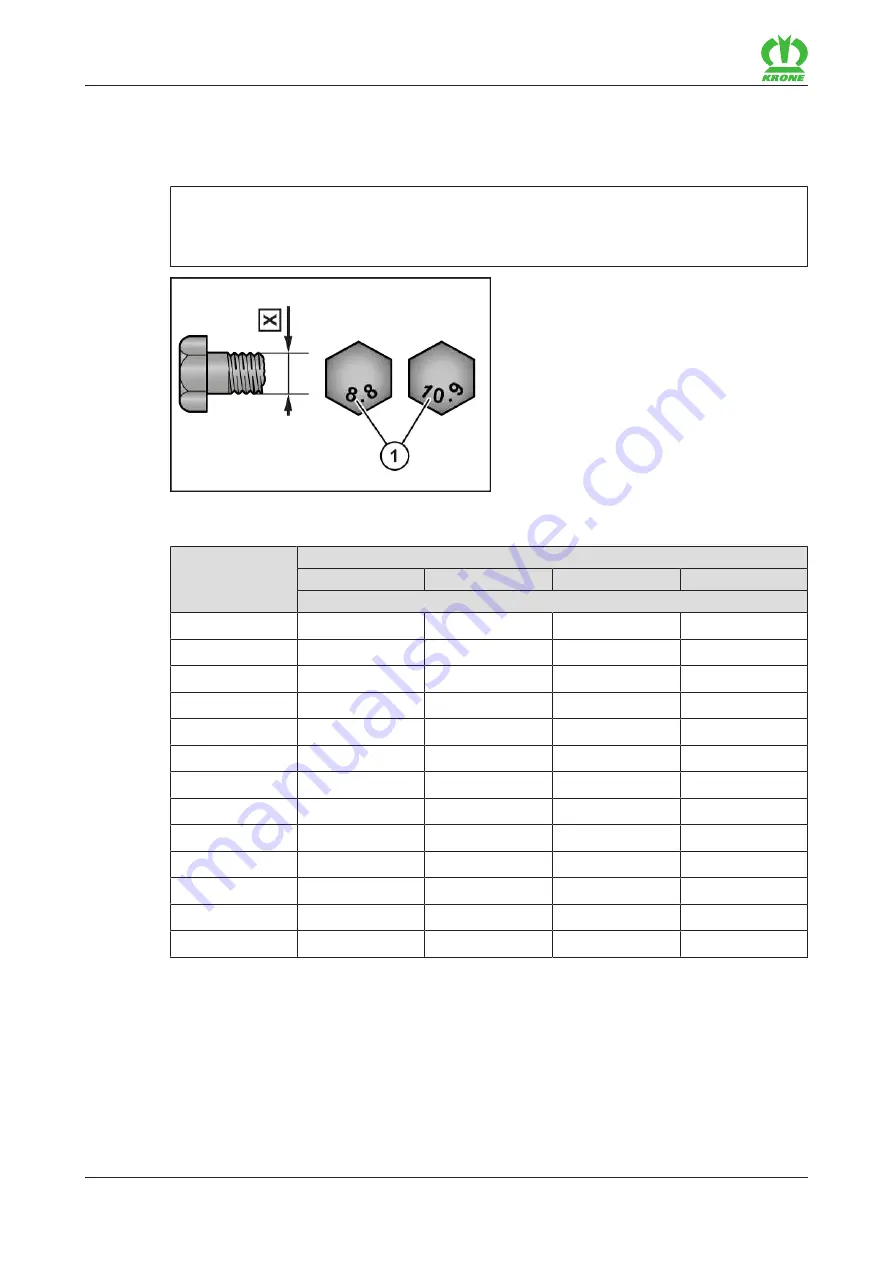
11
Maintenance - General Information
11.2
Tightening torques
58
ActiveMow R 200
Original Operating Instructions 150000521_04_en
11.2
Tightening torques
Metric thread screws with control thread
INFORMATION
The table does not apply to countersunk screws with hexagon socket in case the countersunk
screw is tightened via hexagon socket.
DV000-001
X
Thread size
1
Strength class on screw head
X
Strength class
5.6
8.8
10.9
12.9
Tightening torque (Nm)
M4
3.0
4.4
5.1
M5
5.9
8.7
10
M6
10
15
18
M8
25
36
43
M10
29
49
72
84
M12
42
85
125
145
M14
135
200
235
M16
210
310
365
M20
425
610
710
M22
571
832
972
M24
730
1,050
1,220
M27
1,100
1,550
1,800
M30
1,450
2,100
2,450