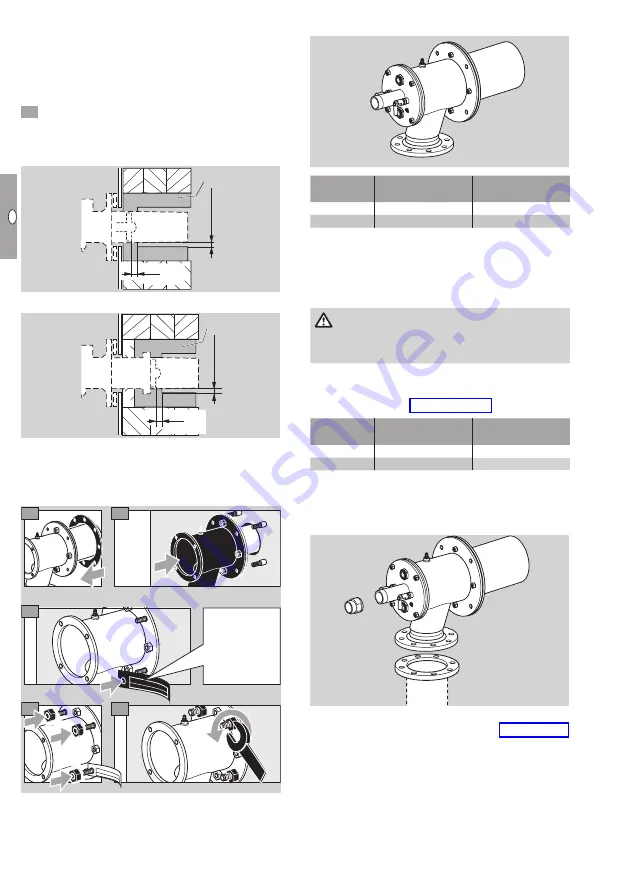
GB-4
D
GB
F
NL
I
E
Insulating the ceramic tube
▷
Protect the burner extension from thermal stress.
▷
We recommend solid shaped parts
A
or high
temperature resistant ceramic fibrous material
B
for insulation.
▷
Observe an annular gap of at least 10 mm (0.4").
Insulate the ceramic tube at least as far as the
burner head, to a maximum of 20 mm (0.8")
behind the burner head.
▷
Burner without extension:
A/B
≥ 10 mm ≥
0.4
in
A/B
20 mm
0.8 in
20 mm
0.8 in
≥
10 mm
≥
0.4
in
▷
Burner with extension:
A/B
≥ 10 mm ≥
0.4
in
A/B
20 mm
0.8 in
20 mm
0.8 in
≥
10 mm
≥
0.4
in
Installation on the furnace
▷
When installing, always ensure that when the
burner is mounted, it is sealed tightly on the
furnace wall.
2
4
1
5
3
TSC 65AO
48-300/35
-Si150
0
Si-1500
y
n
a
m
r
e
G
k
c
ü
r
b
a
n
s
O
8
1
0
9
4
-
D
Attach the
ceramic tube
type label.
Air connection, gas connection
GA
LA
Type
Gas connection
GA
Air connection
LA
ZIC 165
Rp 1½
DN 100
ZIC 200
Rp 2
DN 150
▷
Threaded connection to DIN 2999, flange dimen-
sions to DIN 2633, PN 16.
▷
Install flexible tubes or bellows units to prevent
mechanical stress or transmission of vibration.
▷
Ensure that the seals are undamaged.
DANGER
Risk of explosion! Ensure the connection is gas-
tight.
Connection to ANSI/NPT
▷
An adapter set is required for connection to ANSI/
NPT, see page 12 (Adapter set).
Type
Gas connection
GA
Air connection
LA*
ZIC 165
1½ – 11.5 NPT
4.57"
ZIC 200
1½ – 11.5 NPT
6.72"
* Flange hole diameter.
▷
Weld flange
J
to air pipe
P
for air connection
LA
and use NPT thread adapter
H
for gas con-
nection
GA
.
GA
LA
H
J
P
▷
The nozzle set with NPT coupling is required for