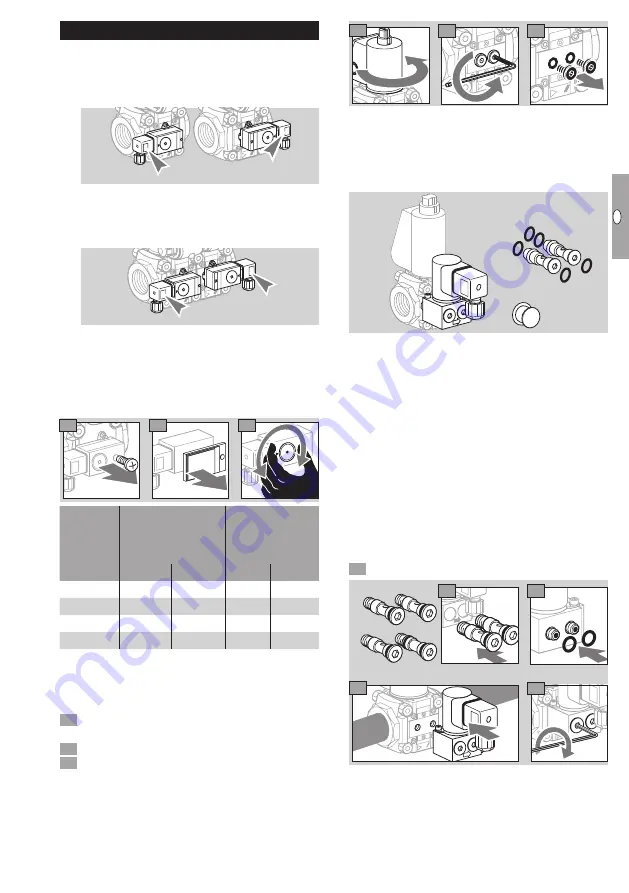
GB-9
D
GB
F
NL
I
E
Accessories
Pressure switch for gas DG..VC
▷
The pressure switch for gas monitors the inlet
pressure p
u
, the outlet pressure p
d
and the in-
terspace pressure p
z
.
DG..C..1
DG..C..9
p
u
p
u
p
z
p
d
▷
When using two pressure switches on the same
side of the double solenoid valve, only the com-
bination DG..C..1 and DG..C..9 may be used for
design reasons.
DG..C..1
DG..C..9
p
u
p
u
p
z
p
d
▷
When retrofitting the pressure switch for gas,
see enclosed operating instructions “Pressure
switches for gas DG..C”, section entitled “Mount-
ing the DG..C..1, DG..C..9 on valVario gas so-
lenoid valves”.
▷
The switching point is adjustable via hand wheel.
2
3
1
Adjusting range
(adjusting tolerance
= ± 15% of the
scale value)
Mean switching
differential at min.
and max. setting
[mbar]
["WC]
[mbar]
["WC]
DG 17VC
2 – 17
0.8 – 6.8 0.7 – 1.7 0.3 – 0.8
DG 40VC
5 – 40
2 – 16
1 – 2
0.4 – 1
DG 110VC 30 – 110
12 – 44
3 – 8
0.8 – 3.2
DG 300VC 100 – 300 40 – 120
6 – 15
2.4 – 8
▷
Deviation from the switching point during testing
pursuant to EN 1854 Gas pressure switches:
± 15%.
Bypass/pilot gas valves
1
Disconnect the system from the electrical power
supply.
Shut off the gas supply.
Prepare the installed main valve.
▷
Turn the actuator so that the side on which the
bypass/pilot gas valve is to be installed is ac-
cessible.
6
5
4
VBY for VAS 1
Medium and ambient temperatures: 0 to +60°C
(32 to 140°F), no condensation permitted.
Enclosure: IP 54.
Scope of delivery
B
C
A
VBY 8
VAS 1
Rp ¼
(Zündgasventil)
Bypass valve VBY..I
A
1 x bypass valve VBY..I
B
2 x retaining screws with 4 x O-rings: both retain-
ing screws have a bypass orifice
C
Grease for O-rings
▷
The screw plug at the outlet remains in place.
Pilot gas valve VBY..R
A
1 x pilot gas valve VBY..R
B
2 x retaining screws with 5 x O-rings: one retain-
ing screw has a bypass orifice (2 x O-rings), the
other does not (3 x O-rings)
C
Grease for O-rings
▷
Remove the screw plug at the outlet and connect
the Rp ¼ pilot gas line.
Mounting the VBY
7
Grease O-rings
B
.
VBY..I
VBY..R
8
9
10
11
▷
Tighten the retaining screws alternately so that
VBY and VAS are flush.