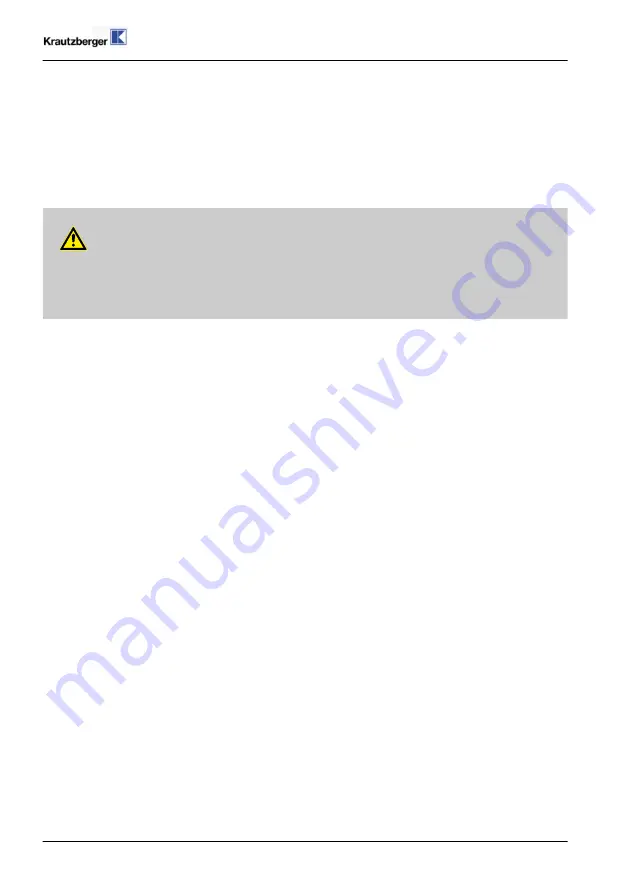
5 Installation
Personnel:
n
Qualified personnel
Protective equipment:
n
Safety shoes
WARNING!
Health hazard!
In conjunction with any use in food and pharmaceutical applications, only use food oils fea-
turing the viscosity class HL 32.
5.1 General installation information
Adhere to the following general information for the installation:
n
Only carry out the installation and commissioning according to the steps described in this
operating manual.
n
Always observe the applicable country-specific safety, accident prevention, occupational
safety, and environmental protection regulations applicable for the area of use for the pneu-
matic agitator.
n
Only use hose lines with a maximum length of 3 m and a diameter of 8-9 mm.
n
Reduce the supply air through the installation of a pressure regulator to a maximum of 6 bar.
n
Provide a cut-off device (e.g. ball valve) at a suitable location for a simple activation and deac-
tivation of the pneumatic agitator. Slowly open the cut-off device.
n
In addition, install suitable pressure regulator with pressure gauge in the supply line in order
to adjust the rotational speed.
n
Only operate pneumatic agitator in vertical position with agitator impellers facing down.
n
Operate the pneumatic agitator with processed, dried compressed air (air quality pursuant to
DIN ISO 8573-1: grade 4).
n
Krautzberger recommends using a maintenance unit.
n
A pressure relieve screw has been placed on the side of the adapter plate of the compressed-
air motor. It must not be covered up under any circumstances and the exhaust air must not be
reduced.
n
Maintain minimum clearances for the agitator impellers (
).
Operating instructions
T-Dok-031-GB-Rev.4
[email protected], www.krautzberger.com
GB–14
Summary of Contents for 200-0356
Page 44: ......