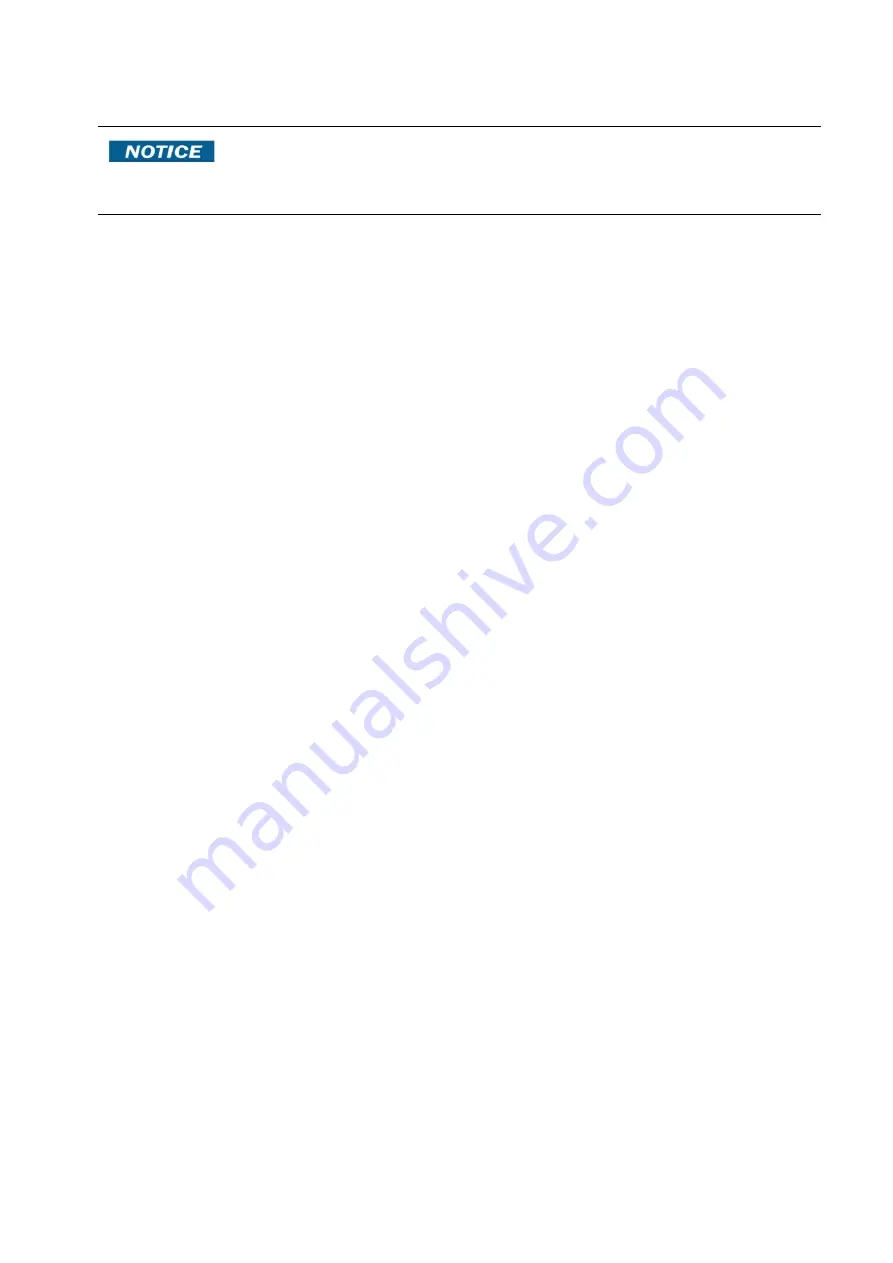
www.kontron.com
CP6940 User Guide
// 15
1.2.7
Shock
The CP6940-RA-OC-P and the CP6940-RA-OC board is designed to meet the VITA 47 standard:
•
20g / 11ms half-sine, or 20g / 11ms terminal sawtooth shock pulses in all three axes
The CP6940-SA-OC-V board is designed to meet the requirements of the following standards:
•
DIN/IEC 60068-2-27
•
Peak Acceleration: 30 g, Shock Duration: 9 ms half sine, Recovery Time: 5 s, Shock Count: 3/direction, 6 direc-
tions, total 18
1.2.8
Bump
All tree CP6940 Boards are designed to meet the IEC 60068-2-29:
•
Peak Acceleration: 15 g
•
Shock Dur.: 11 ms half sine
•
Shock Count: 500
•
Recovery time: 1 s
1.2.9
Safety
The boards are designed to meet or meets the following requirements:
•
UL 61010-1
The boards are designed to meet the following flammability requirement (as specified in Telcordia GR-63-CORE):
•
UL 94V-0/1 with Oxygen index of 28% or greater material
1.2.10
Electromagnetic Compatibility
he boards are designed to meet or exceed class B limit of the following specifications/requirements (assuming an ade-
quate system/chassis):
•
FCC 47 CFR Part 15, Subpart B (USA)
•
EN55032 (Europe)
•
EN61000
•
VCCI (Voluntary Japan Electromagnetic Compatibility requirement)
1.2.11
Reliability
Targeted MTBF is around 140.000h @ 30° C, calculations based on Bellcore Issue 6.
1.2.12
WEEE
Compliant to:
•
Directive 2002/96/EC: Waste electrical and electronic equipment
1.2.13
RoHS Compliance
Components and materials of the product must not contain lead, mercury, cadmium, hexavalent chromium, polybromi-
nated biphenyls (PBB) or polybrominated diphenyl ethers (PBDE) according Directive 2011/65/EU.
1.2.14
Lead-free
The boards have to be completely lead-free concerning the production process and the components used.
If the CP6940 board is used in heavy shock and vibration environment, the hole system
must withstand these requirements. This means the chassis, backplane and guiderails
should be designed for harsh environment. Guide rails with wedge locks are recommend.
The backplane has to be stiffened to avoid connector micro movement. It is also recom-
mended to use connectors which are designed for a rugged environment.