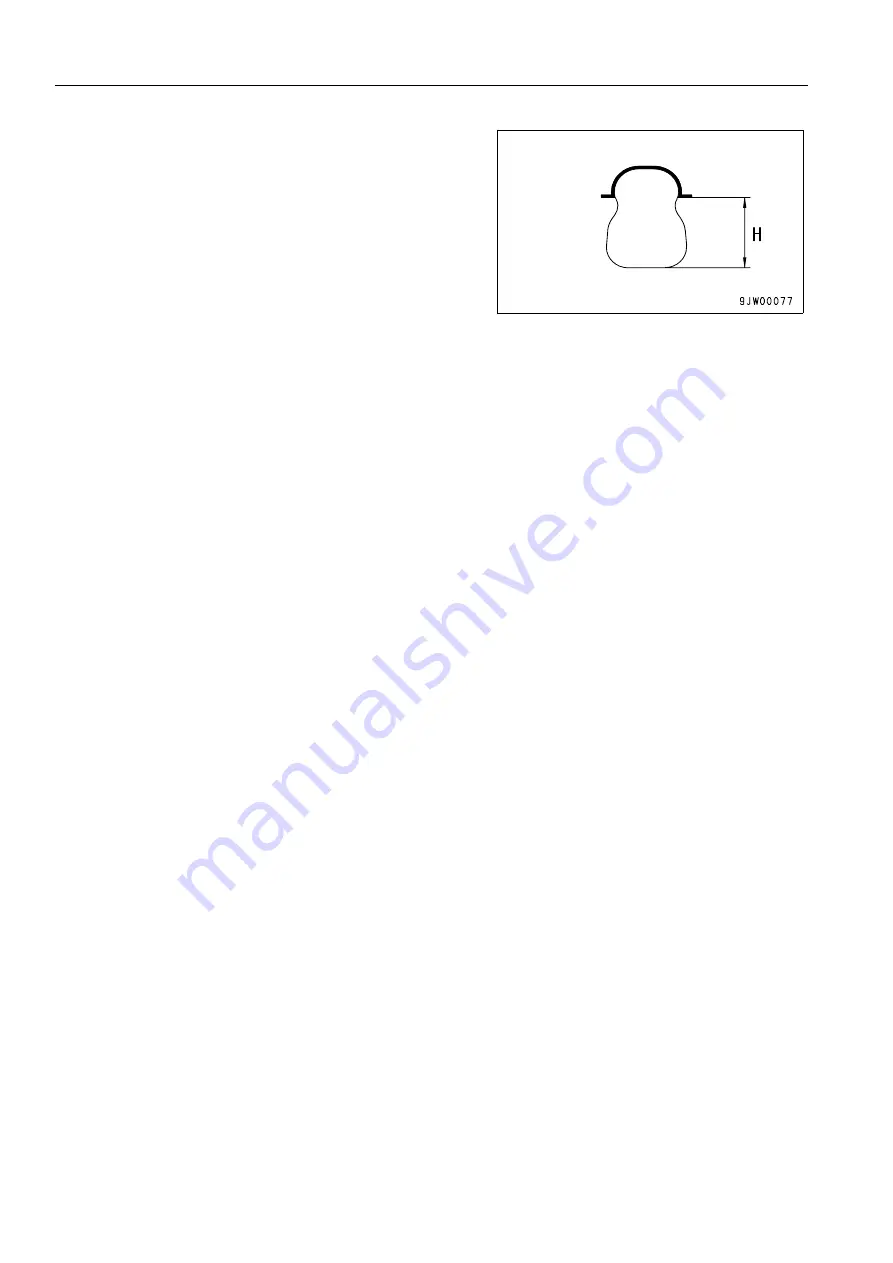
OPERATION
OPERATION
3-134
Stockpile operations mean the loading of sand and other loose
materials.
PRECAUTIONS FOR USING LOAD AND CARRY METHOD
3
When traveling continuously with load and carry operations, choose the correct tires to match the operating condi-
tions, or choose the operating conditions to match the tires. If this is not done, the tires will be damaged, so con-
tact your Komatsu distributor or tire dealer when selecting tires.
Summary of Contents for WA800-3E0
Page 2: ......
Page 3: ...FOREWORD 11...
Page 27: ...SAFETY SAFETY LABELS 2 5 LOCATION OF SAFETY LABELS 2...
Page 66: ...GENERAL VIEW OPERATION 3 4...
Page 84: ...EXPLANATION OF COMPONENTS OPERATION 3 22 SWITCHES 3...
Page 224: ...TROUBLESHOOTING OPERATION 3 162...
Page 309: ...SPECIFICATIONS 15...
Page 330: ...HANDLING MACHINES EQUIPPED WITH VHMS ATTACHMENTS OPTIONS 6 20...
Page 331: ...INDEX 17...
Page 332: ...INDEX 7 2...
Page 335: ...COLOPHON 18...