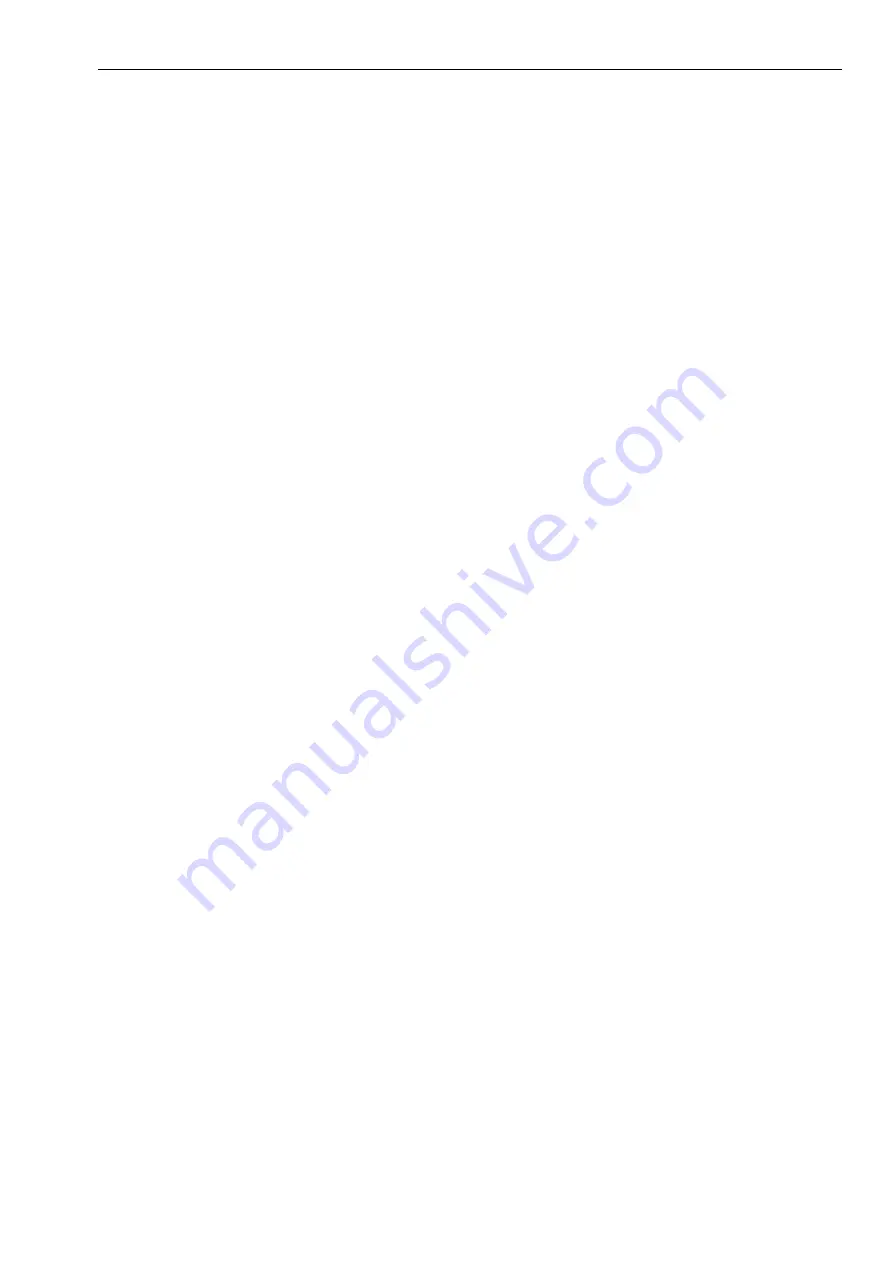
4.9 Service procedure
Maintenance
Every 8000 hours service
WA470-6H – VEAM946100
4-89
Check starting motor
Contact your KOMATSU distributor to have the starting motor
checked.
If the engine is started frequently, have this inspection carried
out every 1000 hours.
4.9.13
Every 8000 hours service
Maintenance for every 50, 250, 500, 1000, 2000 and 4000 hours
service should be carried out at the same time.
Replace high-pressure piping clamp
Ask your KOMATSU distributor to carry out this work.
Replace fuel spray prevention cap
Ask your KOMATSU distributor to carry out this work.
4.9.14
Every 12000 hours service
Maintenance for every 50, 250, 500, 1000, 2000, 4000 and (if
necessecary) 8000 hours service should be carried out at the
same time.
Replace injector assembly
For details see "Replace injector assembly (4-30)".
Summary of Contents for WA470-6 2006
Page 2: ......
Page 3: ...Foreword WA470 6H VEAM946100 1 1 1 Foreword...
Page 22: ...1 5 Contents Foreword 1 20 WA470 6H VEAM946100 7 Index 7 1 7 1 Index 7 2 8 Notes 8 1...
Page 28: ...1 7 CE Conforming equipment Foreword 1 26 WA470 6H VEAM946100...
Page 250: ...3 7 Troubleshooting Operation 3 178 WA470 6H VEAM946100...
Page 340: ...4 9 Service procedure Every 12000 hours service Maintenance 4 90 WA470 6H VEAM946100...
Page 341: ...Technical Data WA470 6H VEAM946100 5 1 5 Technical Data...
Page 343: ...Technical Data 5 1 Technical data WA470 6H VEAM946100 5 3 GK032301 A B H I G C E F D...
Page 348: ...5 4 Limit values for slopes Technical Data 5 8 WA470 6H VEAM946100...
Page 381: ...Index WA470 6H VEAM946100 7 1 7 Index...
Page 387: ...Notes WA470 6H VEAM946100 8 1 8 Notes...
Page 388: ...Notes 8 2 WA470 6H VEAM946100...
Page 389: ...Notes WA470 6H VEAM946100 8 3...
Page 390: ...Notes 8 4 WA470 6H VEAM946100...
Page 391: ...Notes WA470 6H VEAM946100 8 5...
Page 392: ...Notes 8 6 WA470 6H VEAM946100...