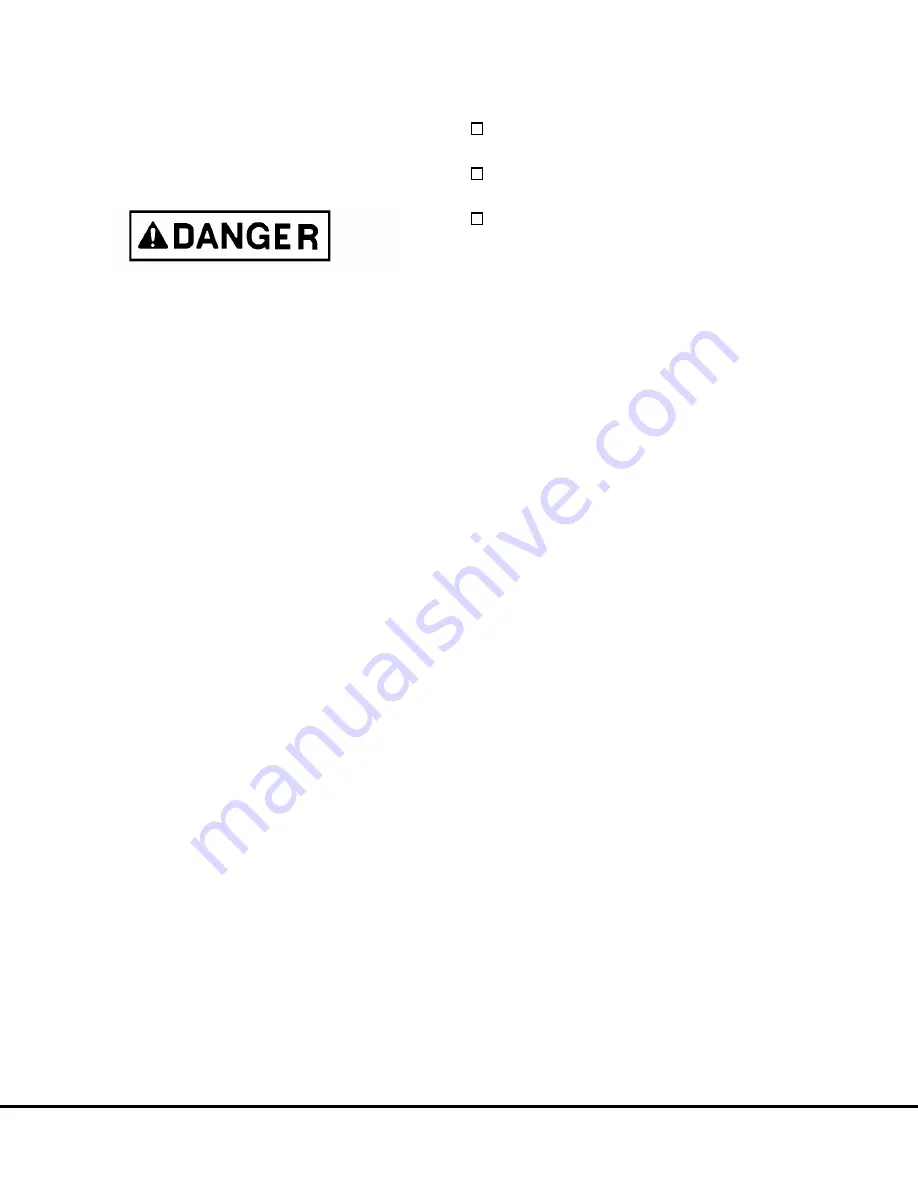
WHEEL MOTOR
Read and observe the following instructions be-
fore attempting removal of the wheel motors or any
repairs on the propulsion system components!
•
Do not step on or use any power cable as a
handhold when the engine is running.
•
All removal, repairs and installation of propul-
sion system electrical components, cables etc.
must be performed by an electrical maintenance
technician properly trained to service the sys-
tem.
•
In the event of a propulsion system malfunction,
a qualified technician should inspect the truck
and verify the propulsion system does not have
dangerous voltage levels present before repairs
are started.
After the truck is parked in position for the repairs, the
truck must be shut down properly to ensure the safety
of those working in the area of the wheel motors, and
possibly the electrical cabinet and retarding grids. The
following procedures will ensure the electrical system
is properly discharged before repairs are started.
PREPARATION
1. Reduce the engine speed to idle. Place the selec-
tor switch in NEUTRAL and apply the parking
brake. Be certain the parking brake applied indi-
cator lamp in the overhead panel is illuminated.
2. Place the drive system in the REST mode by
turning the Rest switch on the instrument panel
ON. Be certain the REST warning lamp is illumi-
nated.
3. Shut down the engine using the keyswitch. Place
the GF Cutout Switch in the CUTOUT position.
4. Verify the LINK VOLTAGE lights are OFF. If they
remain on longer than 5 minutes after shutdown,
notify the electrical department.
5. Verify the steering accumulators have bled down
by attempting to steer.
6. Bleed down the brake accumulators using the
manual bleed valves on the brake manifold.
7. Open the battery disconnect switches.
Front wheels must be securely blocked to prevent
movement as brakes will be released.
All electrical cables and hydraulic hoses should
be marked prior to removal.
Close the shut-off valves on the hydraulic pumps
to reduce amount of oil loss from brake system.
Removal
NOTE: If suitable equipment is available to lift wheel
motor assembly from the axle housing it is not neces-
sary to remove the truck body. The equipment used
must be capable of lifting and supporting the weight of
the complete wheel motor assembly, 35,050 Lbs.
(15,913 kg.), must be mobile and must be capable of
aligning the wheel motor to the axle housing mounting
flange during installation.
If the wheel motor must be removed by use of a crane
or overhead hoist, refer to Section “B” for body removal
instructions.
1. Raise the rear of truck as described in this Section,
until tires clear the ground. Use support stands or
cribbing to block under rear housing.
2. Remove the inner and outer wheels from wheel
motor. Refer to tire and wheel removal instruc-
tions in this Section. Be certain additional cap-
screws have been installed to provide support for
the wheel motor transmission housing while the
rear tires are removed.
3. With the pump shut-off valves in the closed posi-
tion, remove the drain plug at bottom of brake
assembly and drain oil from disc brake housing.
4. Remove covers from access holes (17, Figure 5-1)
5. Disconnect brake system cooling lines (2 & 10) at
brake back plate. Disconnect brake apply lines
(11). Cap and plug openings.
6. Remove clamps (3) securing brake hoses to spin-
dles.
7. Open rear access cover and remove wing nuts
securing duct tube to axle housing. Remove tube.
8. Open access covers inside axle housing.
9. Disconnect parking brake supply line for the motor
to be removed. Disconnect air sensor hose if
necessary.
10. Remove wheel motor cooling air exhaust duct (5)
from between wheel motors.
G5-4
Rear Axle Housing
9/99 G05015
Summary of Contents for 930E-2
Page 1: ......
Page 2: ......
Page 4: ...NOTES ...
Page 8: ...KOMATSU MODEL 930E Dump Truck A 4 Introduction A00017 03 01 ...
Page 10: ...NOTES A1 2 Index A01001 2 94 ...
Page 12: ...930E MAJOR COMPONENTS A2 2 Major Component Description A02055 ...
Page 35: ...START HERE Walk Around Inspection A03017 General Safety and Operating Instructions A3 21 ...
Page 46: ...NOTES A3 32 General Safety and Operating Instructions A03017 ...
Page 78: ...NOTES B1 2 Index B01016 ...
Page 88: ...NOTES B3 6 Dump Body B03013 03 01 ...
Page 92: ...NOTES B4 4 Fuel Tank B04015 ...
Page 94: ...NOTES C1 2 Index C01021 03 01 ...
Page 118: ...NOTES C5 6 Air Filtration System C05013 5 98 ...
Page 126: ...NOTES D2 6 24VDC Electric Supply System D02018 ...
Page 142: ...NOTES D3 16 24VDC System Components D03019 04 01 ...
Page 146: ...FIGURE 2 1 PROPULSION SYSTEM DIAGRAM E2 2 Electrical Propulsion System Components E02014 3 01 ...
Page 196: ...NOTES E2 52 Electrical Propulsion System Components E02014 3 01 ...
Page 240: ...NOTES E3 44 AC Drive System Electrical Checkout Procedure 3 01 E03015 Release 17 Software ...
Page 242: ...NOTES G1 2 Index G01017 ...
Page 250: ...NOTES G2 8 Tires and Rims G02015 ...
Page 274: ...NOTES H1 2 Index H01013 04 01 ...
Page 282: ...NOTES H2 8 Front Suspensions H02013 2 01 ...
Page 288: ...NOTES H3 6 Rear Suspensions H03013 ...
Page 334: ...NOTES J3 32 Brake Circuit Component Service J03019 1 99 ...
Page 378: ...NOTES L2 8 Hydraulic System L02028 ...
Page 401: ...FIGURE 4 5 FLOW AMPLIFIER VALVE L04031 Steering Circuit L4 7 ...
Page 403: ...FIGURE 4 6 FLOW AMPLIFIER NO STEER L04031 Steering Circuit L4 9 ...
Page 405: ...FIGURE 4 7 FLOW AMPLIFIER LEFT STEER L04031 Steering Circuit L4 11 ...
Page 407: ...FIGURE 4 8 FLOW AMPLIFIER RIGHT STEER L04031 Steering Circuit L4 13 ...
Page 409: ...FIGURE 4 9 FLOW AMPLIFIER NO STEER EXTERNAL SHOCK LOAD L04031 Steering Circuit L4 15 ...
Page 414: ...NOTES L4 20 Steering Circuit L04031 ...
Page 422: ...NOTES L5 8 Steering Control Unit L05021 ...
Page 429: ...L06021 Steering Circuit Component Repair L6 7 ...
Page 450: ...NOTES L6 28 Steering Circuit Component Repair L06021 ...
Page 466: ...NOTES L7 16 Hoist Circuit L07023 ...
Page 492: ...NOTES L9 6 Hydraulic System Filters L09008 ...
Page 504: ...NOTES L10 12 Hydraulic Check out Procedure L10012 ...
Page 508: ...NOTES M1 2 Index M01034 03 01 ...
Page 518: ...NOTES M2 3 10 Ansul Checkfire Electric Detection and Actuation System M02003 ...
Page 524: ...NOTES M5 4 Wiggins Quick Fill Fuel System M05002 10 96 ...
Page 532: ...NOTES M8 8 Special Tools M08012 9 99 ...
Page 560: ...NOTES M9 28 Air Conditioning System M09010 6 97 for HFC 134a Refrigerant ...
Page 618: ...M20 20 Payload Meter II M20007 10 00 ...
Page 619: ...M20007 10 00 Payload Meter II M20 21 ...
Page 627: ...M20007 10 00 Payload Meter II M20 29 ...
Page 634: ...NOTES N1 2 Index N01020 03 01 ...
Page 654: ...NOTES N3 6 Cab Components N03011 7 98 ...
Page 660: ...NOTES N4 6 Operator Comfort N04020 ...
Page 686: ...NOTES N5 26 Operator Cab Controls N05044 ...
Page 688: ...NOTES P1 2 Index P01024 ...
Page 691: ...P02034 Lubrication and Service P2 3 ...
Page 722: ......
Page 723: ......
Page 724: ......
Page 725: ......
Page 726: ......
Page 727: ......
Page 728: ......
Page 729: ......
Page 730: ......
Page 731: ......
Page 732: ......
Page 733: ......
Page 734: ......
Page 735: ......
Page 736: ......
Page 737: ...NOTES R1 2 930E Schematics R01048 with Cummins QSK60 Series Engine ...
Page 738: ......
Page 739: ......