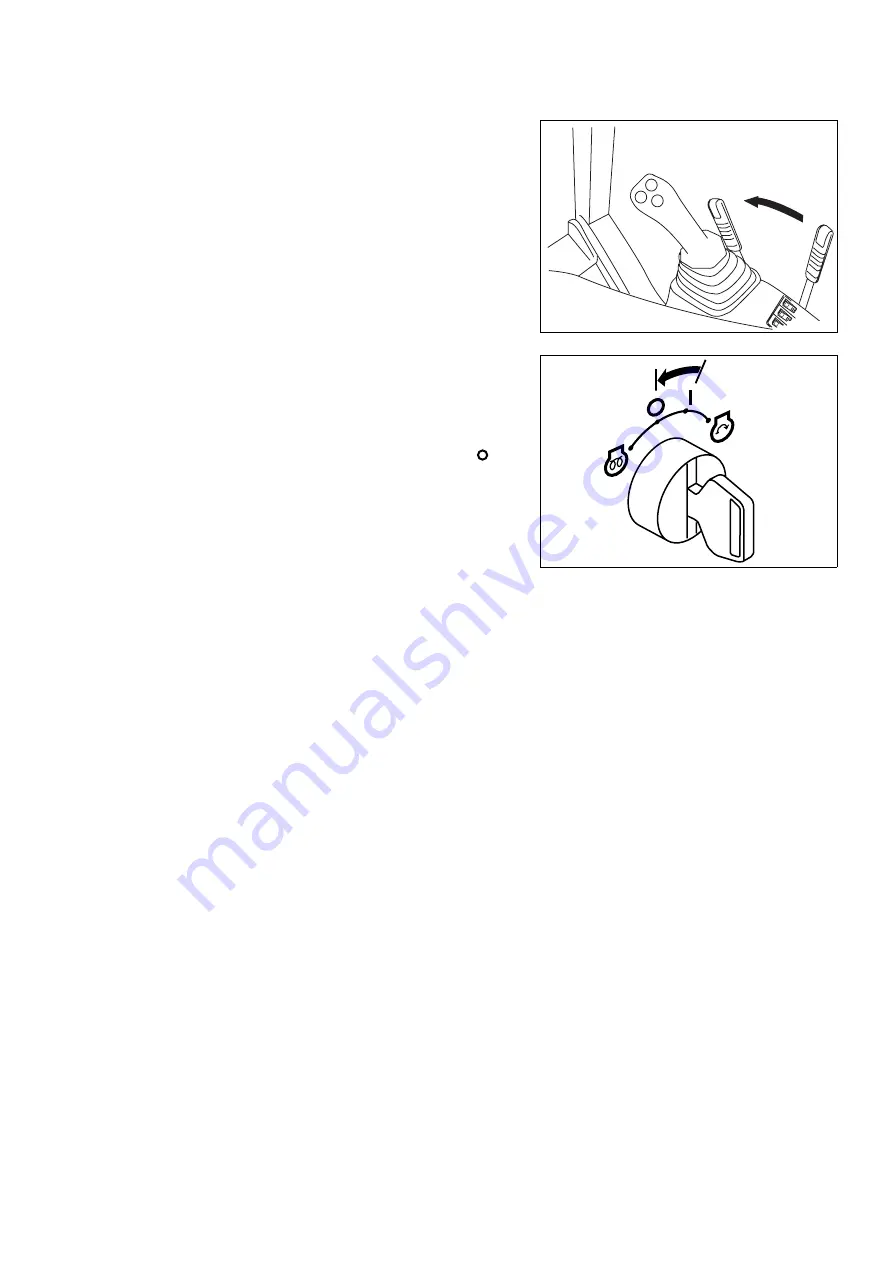
STOPPING THE ENGINE
123
3.8 STOPPING THE ENGINE
IMPORTANT
q
Do not stop the engine suddenly, except in case of
emergency; the sudden stop of the engine while it is
running shortens its life.
q
It is likewise recommended not to stop the engine sud-
denly if it has been running for a long period and is still
hot; in this case, let the engine idle for about 5 minutes,
in order to allow it to cool down gradually before stop-
ping it.
Before stopping the engine, proceed as follows:
1 - Rest the work equipment on to the ground.
2 - Shift the levers to the neutral position and engage the sa-
fety devices.
3 - Shift the accelerator lever to the idling position.
Stop the engine by turning the ignition key to position « »
(OFF).
RWA32520
RWA02000
Summary of Contents for 37BF50111
Page 2: ......
Page 17: ...SAFETY AND ACCIDENT PREVENTION 15...
Page 19: ...SAFETY NOISE AND VIBRATION PLATES 17 RWA00010 RWA37020...
Page 21: ...SAFETY NOISE AND VIBRATION PLATES 19 RWA37040 RWA00010 RWA00020...
Page 53: ...THE MACHINE AND ITS OPERATIONS 51...
Page 62: ...GENERAL VIEWS 60 10 Left console switches 11 Right console switches RWAA9720 11 RWAA11260 10...
Page 154: ...152 PAGE INTENTIONALLY LEFT BLANK...
Page 155: ...MAINTENANCE 153...
Page 205: ...TECHNICAL SPECIFICATIONS 203...
Page 213: ...TECHNICAL DATA 211 SOLID TYRES SIZE MAKE 10x16 5 AIR BOSS...
Page 214: ...212 PAGE INTENTIONALLY LEFT BLANK...
Page 215: ...AUTHORISED OPTIONAL EQUIPMENT 213...
Page 242: ...240 PAGE INTENTIONALLY LEFT BLANK...
Page 243: ......
Page 244: ...2004 KOMATSU UTILITY EUROPE S p A All Rights Reserved Printed in Europe...