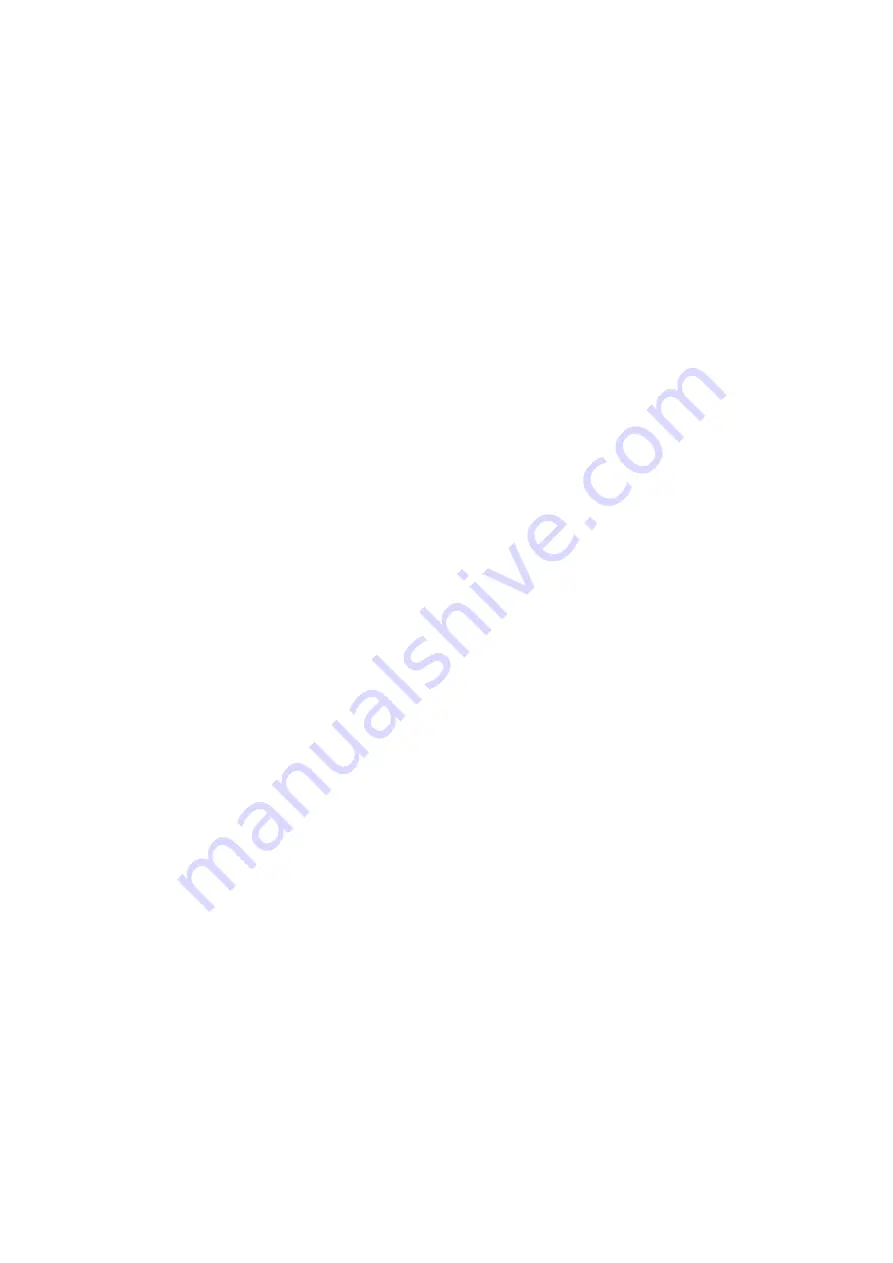
LUBRICANTS, COOLANT AND FILTERS
163
4.2.2 ELECTRIC SYSTEM MAINTENANCE
• It is extremely dangerous if the electrical equipment becomes wet or the covering of the wiring is damaged. This
will cause an electrical short circuit and may lead to malfunction of the machine. Do not wash the inside of the
operator's cab with water. When washing the machine, be careful not to let water get into the electrical compo-
nents.
• Service relating to the electric system is checking fan belt tension, checking damage or wear to the fan belt and
checking battery fluid level.
• Never install any electric components other than those specified by Komatsu.
• External electro-magnetic interference may cause malfunction of the control system controller, so before install-
ing a radio receiver or other wireless equipment, please contact your Komatsu Dealer.
• When working at the seashore, carefully clean the electric system to prevent corrosion.
• When installing an operator's cab cooler or any other electrical equipment, connect it to an independent power
source connector. The cables to supply power to the optional equipment must never be connected to the fuse,
starting switch, or battery relay.
4.2.3 HANDLING HYDRAULIC SYSTEM
• Hydraulic equipment is at a high temperature during operations and immediately after operations. During opera-
tions, it is also under high pressure, so be careful of the following points when carrying out inspection and main-
tenance of hydraulic-related equipment.
• Stop the machine on level ground, lower the bucket completely to the ground, and set so that there is no
pressure on the cylinder circuits.
• Always stop the engine.
• Immediately after the engine is stopped, the hydraulic oil and lubricants are at a high temperature and high
pressure. Wait for the temperature to go down before starting the maintenance operation.
Even when the temperature goes down, the circuits may be under internal pressure, so when loosening
plugs, screws, or hose connections, do not stand directly in front. Loosen gradually to release the internal
pressure before removing.
• Always release the air in the hydraulic tank to remove the internal pressure before carrying out inspection
and maintenance of the hydraulic circuit.
• Inspection and maintenance works include checking the hydraulic system for oil level, replacement of filter ele-
ments and replacement of hydraulic oil.
• If high-pressure hoses have been removed, check that there is no damage to the O-rings. If any damage is
found, replace the O-ring.
• It is necessary to bleed the air from the circuits when the hydraulic filter element or strainer have been replaced
or washed, or when hydraulic equipment has been repaired or replaced, or when the hydraulic piping has been
removed.
Summary of Contents for 15001
Page 2: ......
Page 18: ...16 PAGE INTENTIONALLY LEFT BLANK ...
Page 19: ...SAFETY AND ACCIDENT PREVENTION 17 ...
Page 54: ...52 PAGE INTENTIONALLY LEFT BLANK ...
Page 55: ...THE MACHINE AND ITS OPERATIONS 53 ...
Page 156: ...154 PAGE INTENTIONALLY LEFT BLANK ...
Page 157: ...MAINTENANCE 155 ...
Page 207: ...TECHNICAL SPECIFICATIONS 205 ...
Page 216: ...LIFTING CAPACITIES 214 PAGE INTENTIONALLY LEFT BLANK ...
Page 217: ...AUTHORISED OPTIONAL EQUIPMENT 215 ...
Page 232: ...230 PAGE INTENTIONALLY LEFT BLANK ...
Page 233: ......
Page 234: ... 2005 KOMATSU UTILITY EUROPE S p A All Rights Reserved Printed in Europe ...