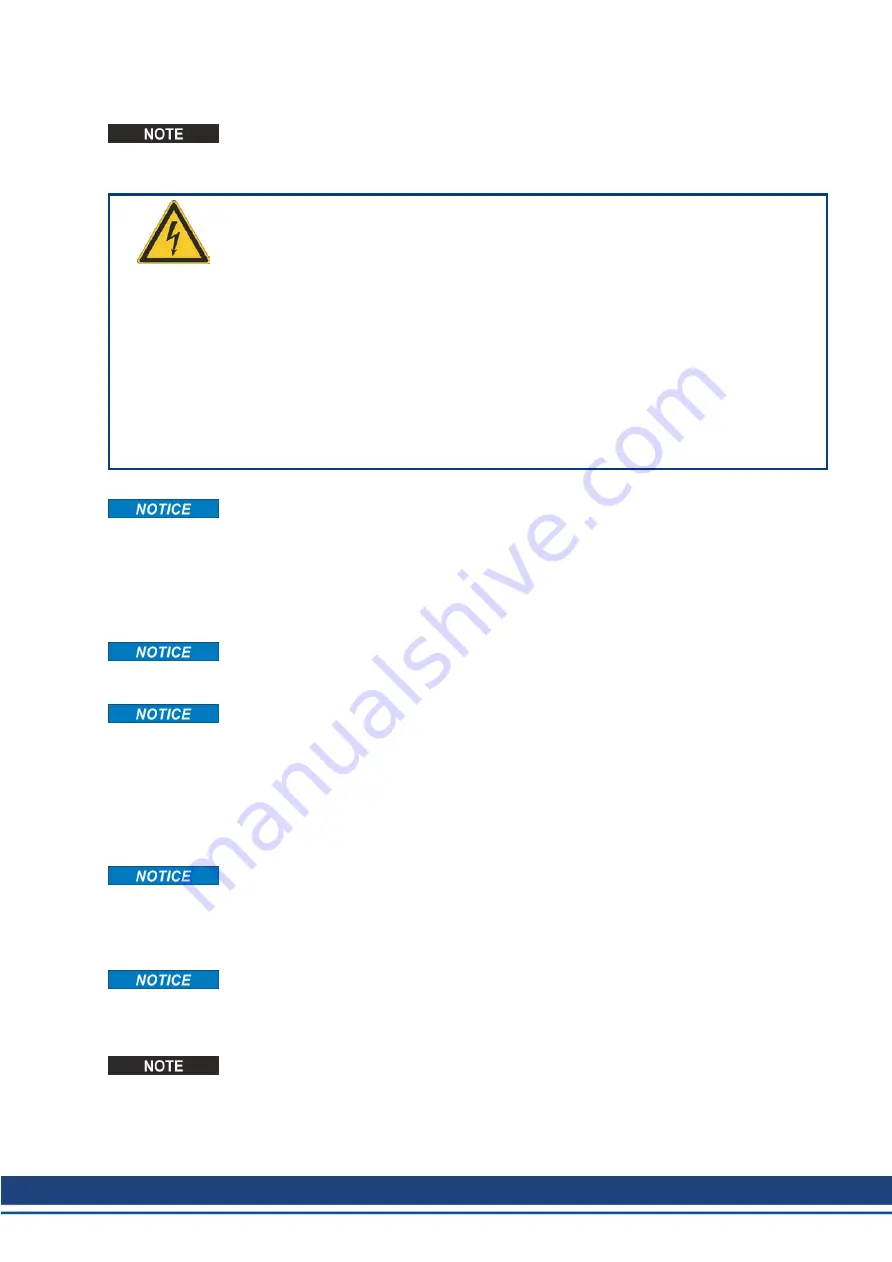
2.5 Electrical Installation
For connector overview (
# 146). For more interface pinout refer to the
Instructions Manual
.
2.5.1 Important Notes
WARNING
Never remove electrical connections to the servo amplifier while it is live.
There is a danger of electrical arcing with damage to contacts and serious
personal injury. Wait at least five minutes after disconnecting the servo
amplifier from the main supply power before touching potentially live sec-
tions of the equipment (e.g. contacts) or undoing any connections.
Capacitors can still have dangerous voltages present up to 5 minutes
after switching off the supply power. To be sure, measure the voltage in
the DC bus link and wait until it has fallen below 60 V.
Control and power connections can still be live, even if the motor is not
rotating.
Wrong mains voltage, unsuitable motor or wrong wiring will damage the amplifier.
Check the combination of servo amplifier and motor. Compare the rated voltage and current
of the units. Implement the wiring according to the connection diagram (
Make sure that the maximum permissible rated voltage at the terminals L1, L2, L3 or +DC, –
DC is not exceeded by more than 10% even in the most unfavorable circumstances (see
IEC 60204-1).
Excessively high external fusing will endanger cables and devices. The fusing of the AC sup-
ply input and 24 V supply must be installed by the user, best values (
# 45). Hints for use
of Residual-current circuit breakers (FI) see
Instructions Manual
.
Correct wiring is the basis for reliable functioning of the servo system. Route power and con-
trol cables separately. We recommend a distance of at least 200 mm. This improves the inter-
ference immunity. If a motor power cable is used that includes cores for brake control, the
brake control cores must be separately shielded. Ground the shielding at both ends. Ground
all shielding with large areas (low impedance), with metalized connector housings or shield
connection clamps wherever possible. Notes on connection techniques can be found in the
Instructions Manual
.
Feedback lines may not be extended, since thereby the shielding would be interrupted and
the signal processing could be disturbed. Lines between servo amplifiers and filter or external
brake resistor must be shielded. Install all power cables with an adequate cross-section, as
per IEC 60204.
The servo amplifier's status must be monitored by the PLC to acknowledge critical situ-
ations. Wire the BTB/RTO contact in series into the emergency stop circuit of the install-
ation. The emergency stop circuit must operate the supply contactor.
It is permissible to use the setup software to alter the settings of the servo amplifier. Any
other alterations will invalidate the warranty.
S300 Safety Guide | 2 English
Kollmorgen | wiki-kollmorgen.eu | December 2015
49
Summary of Contents for SERVOSTAR 300
Page 30: ...S300 Safety Guide 1 Deutsch 30 Kollmorgen wiki kollmorgen eu December 2015...
Page 58: ...S300 Safety Guide 2 English 58 Kollmorgen wiki kollmorgen eu December 2015...
Page 86: ...S300 Safety Guide 3 Fran ais 86 Kollmorgen wiki kollmorgen eu December 2015...
Page 114: ...S300 Safety Guide 4 Italiano 114 Kollmorgen wiki kollmorgen eu December 2015...
Page 117: ...5 1 2 PDF 5 1 3 Symbol S300 Safety Guide 5 Kollmorgen wiki kollmorgen eu December 2015 117...
Page 122: ...S300 Safety Guide 5 5 2 3 UN 230 B S300 122 Kollmorgen wiki kollmorgen eu December 2015...
Page 126: ...S300 Safety Guide 5 5 3 2 SERVOSTAR 300 126 Kollmorgen wiki kollmorgen eu December 2015...
Page 139: ...5 6 3 3 S300 Safety Guide 5 Kollmorgen wiki kollmorgen eu December 2015 139...
Page 153: ...S300 Safety Guide Kollmorgen wiki kollmorgen eu December 2015 153...