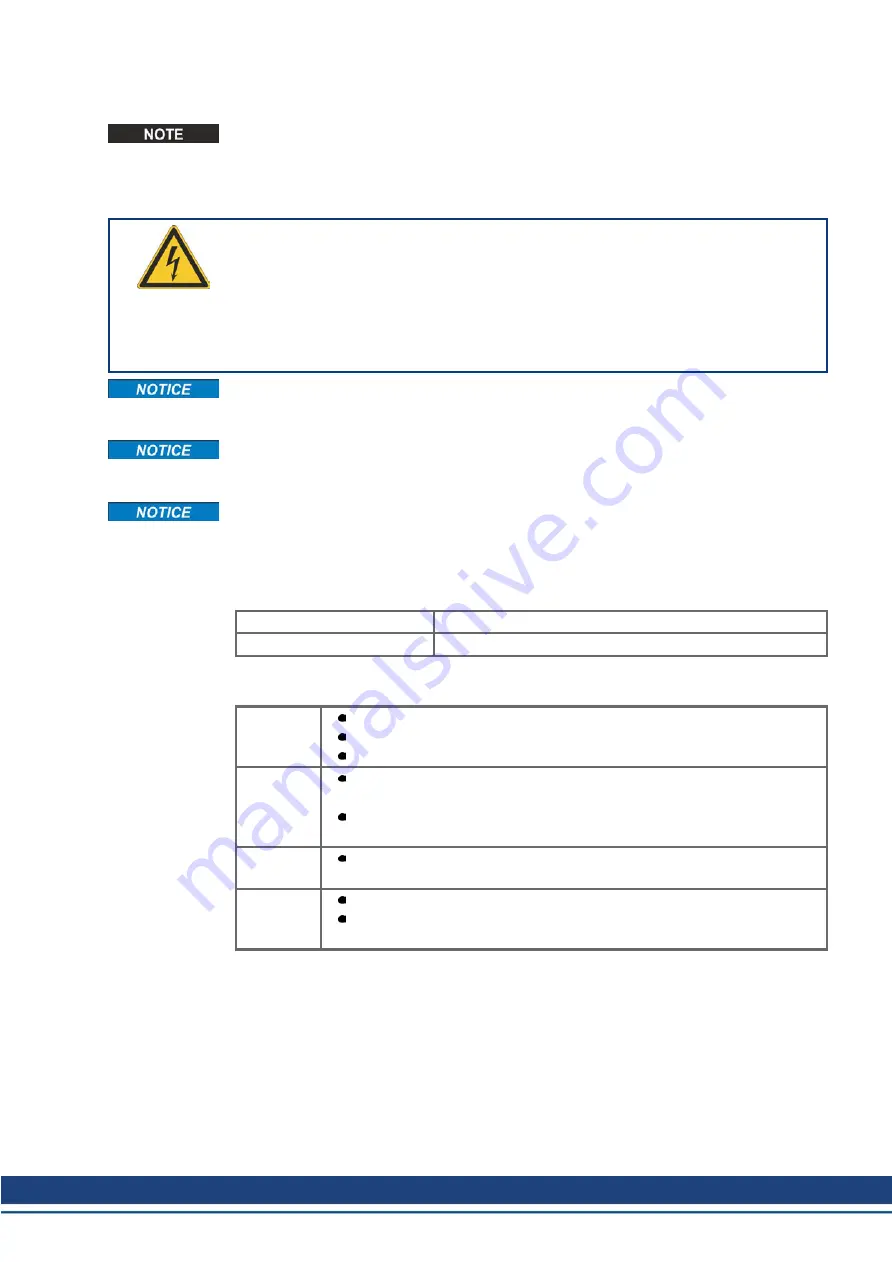
2.4 Mechanical Installation
Dimensions and mounting see (
2.4.1 Important Notes
CAUTION
There is a danger of electrical shock by high EMC level which could res-
ult in injury, if the servo amplifier (or the motor) is not properly EMC-groun-
ded. Do not mount the servo amplifier to painted (i.e. non-conductive)
mounting plates. In unfavourable circumstances, use copper mesh tape
between the earthing bolts and earth potential to deflect currents.
Protect the servo amplifier from impermissible stresses. In particular, do not let any com-
ponents become bent or any insulation distances altered during transport and handling. Avoid
contact with electronic components and contacts.
The servo amplifier will switch itself off in case of overheating. Ensure that there is an
adequate flow of cool, filtered air into the bottom of the control cabinet, or use a heat
exchanger.
Do not mount devices that produce magnetic fields directly beside the servo amplifier.
Strong magnetic fields can directly affect internal components. Mount devices which pro-
duce magnetic field with distance to the servo amplifier and/or shield the magnetic fields.
2.4.2 Guide to Mechanical Installation
Material
4 respectively 6 hexagon socket screws to EN 4762, M5
Tool required
4 mm Allen key
The following notes should assist you to carry out the mechanical installation in a sensible
sequence, without overlooking anything important.
Site
Mount in a closed switchgear cabinet.
The site must be free from conductive or corrosive materials.
For the mounting position in the cabinet refer to (
Ventilation
Check that the ventilation of the servo amplifier is unimpeded and keep
within the permitted ambient temperature (
Keep the required space clear above and below the servo amplifier (
Assembly
Assemble the servo amplifier and power supply, filter and choke close
together on the conductive,
grounded
mounting plate in the cabinet.
Grounding
Shielding
EMC-compliant (EMI) shielding and grounding see Instructions Manual.
Earth (ground) the mounting plate, motor housing and CNC-GND of the
controls.
S700 Safety Guide | 2 English
Kollmorgen | September 2015
63
Summary of Contents for S700 Series
Page 14: ...S700 Safety Guide 1 Deutsch 1 3 3 Antriebssystem mit S701 S724 14 Kollmorgen September 2015 ...
Page 15: ...1 3 4 Antriebssystem mit S748 S772 S700 Safety Guide 1 Deutsch Kollmorgen September 2015 15 ...
Page 40: ... S700 Safety Guide 1 Deutsch 40 Kollmorgen September 2015 ...
Page 52: ...S700 Safety Guide 2 English 2 3 3 Motion system with S701 S724 52 Kollmorgen September 2015 ...
Page 53: ...2 3 4 Motion system with S748 S772 S700 Safety Guide 2 English Kollmorgen September 2015 53 ...
Page 78: ... S700 Safety Guide 2 English 78 Kollmorgen September 2015 ...
Page 116: ... S700 Safety Guide 3 Français 116 Kollmorgen September 2015 ...
Page 154: ... S700 Safety Guide 4 Italiano 154 Kollmorgen September 2015 ...
Page 167: ...5 3 3 Приводная система с S701 S724 S700 Safety Guide 5 Русский Kollmorgen September 2015 167 ...
Page 168: ...S700 Safety Guide 5 Русский 5 3 4 Приводная система с S748 S772 168 Kollmorgen September 2015 ...
Page 194: ... S700 Safety Guide 5 Русский 194 Kollmorgen September 2015 ...
Page 214: ... S700 Safety Guide 6 Appendix 214 Kollmorgen September 2015 ...
Page 215: ... S700 Safety Guide Kollmorgen September 2015 215 ...