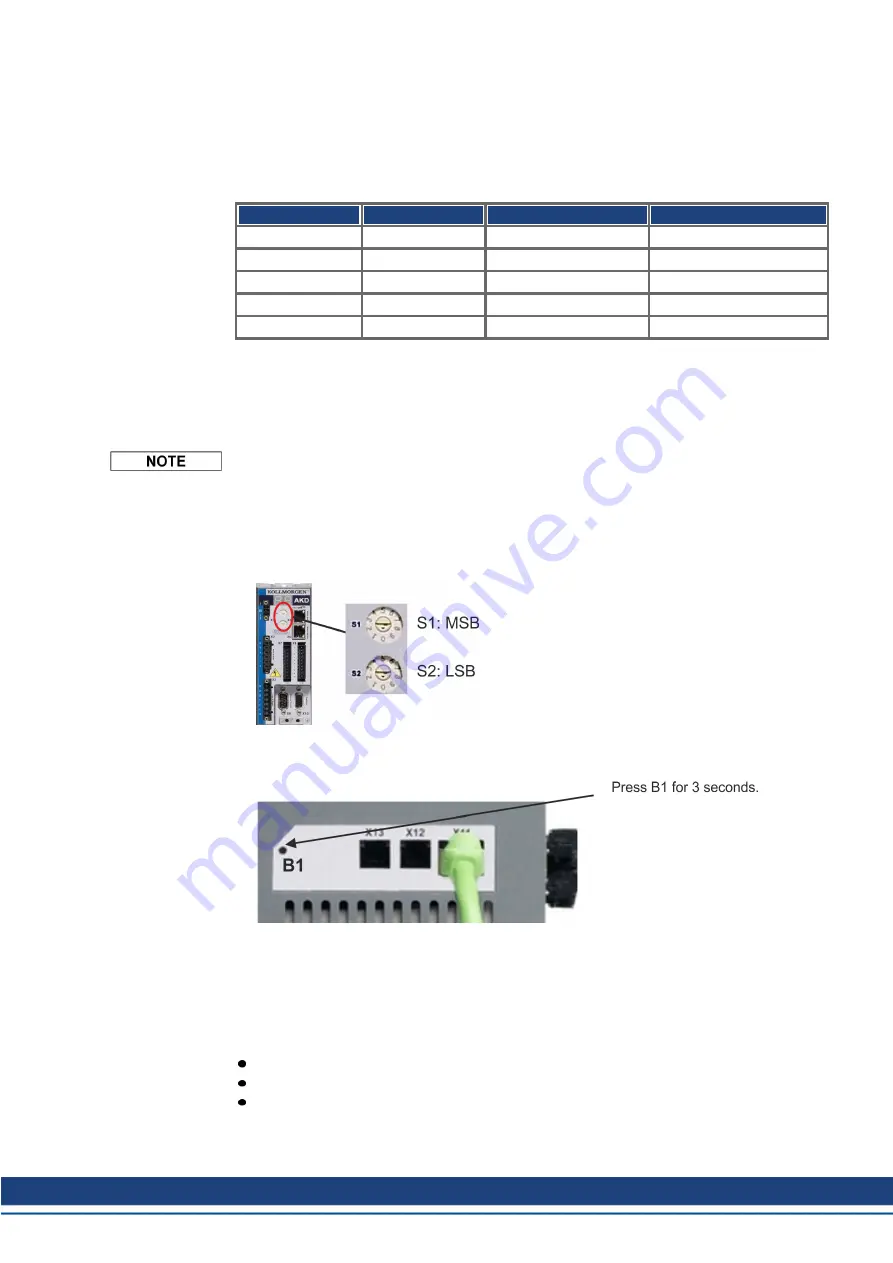
9.20.2 Baud rate for CAN-Bus
The user can decide to use a fixed baud rate or an auto baud detection algorithm for the star-
tup behavior of the drive. The transmission rate can be set via the parameter
FBUS.PARAM01
. The parameter FBUS.PARAM01 can either be set via WorkBench or via
a special mechanism with the rotary switches in the AKD front.
Baud rate [kBit/s] FBUS.PARAM01 Upper rotary switch S1
Lower rotary switch S2
auto detect
0
9
0
125
125
9
1
250
250
9
2
500
500
9
3
1000
1000
9
4
In case of a fix baud rate, the drive sends the boot up message with the baud rate saved in
the drive's non volatile memory after a power cycle. In case of auto baud detection, the drive
listens for a valid CAN frame on the bus. When a valid frame is received, the drive sends the
boot up message with the measured bit time. The baud rate can either be stored afterwards
to non volatile memory via object 1010 sub 1, or the auto baud mechanism is used always.
For reliable auto baud detection, it is recommended to use suitable cabling of the CAN-Bus
(two terminators, GND connection etc.). The drive needs to be disabled, if auto baud is in
use.
For setting the baud rate with rotary switches, follow the procedure below:
1. Disable the drive.
2. Set the rotary switches to either 90 to 94 (see above table).
Set S1 to 9 and S2 to either 0 or 4
3. Push the button B1 on the AKD for at least 3 seconds until the rotary switch setting is dis-
played on the AKD-display.
4. When the display blinks with the set rotary switch setting stop pushing B1 and wait until
the blinking stops. During that time the parameter FBUS.PARAM01 is set to the new
value and all parameters are stored to the non volatile memory. The new setting will be
taken with the next power-up of the drive.
If an error occurred, the following error messages will flash 5 times:
E1 - Drive is enabled
E2 - Non-volatile storage of the new setting failed
E3 - Invalid rotary switch selection
AKD Installation | 9 Electrical Installation
Kollmorgen | kdn.kollmorgen.com | October 2017
177