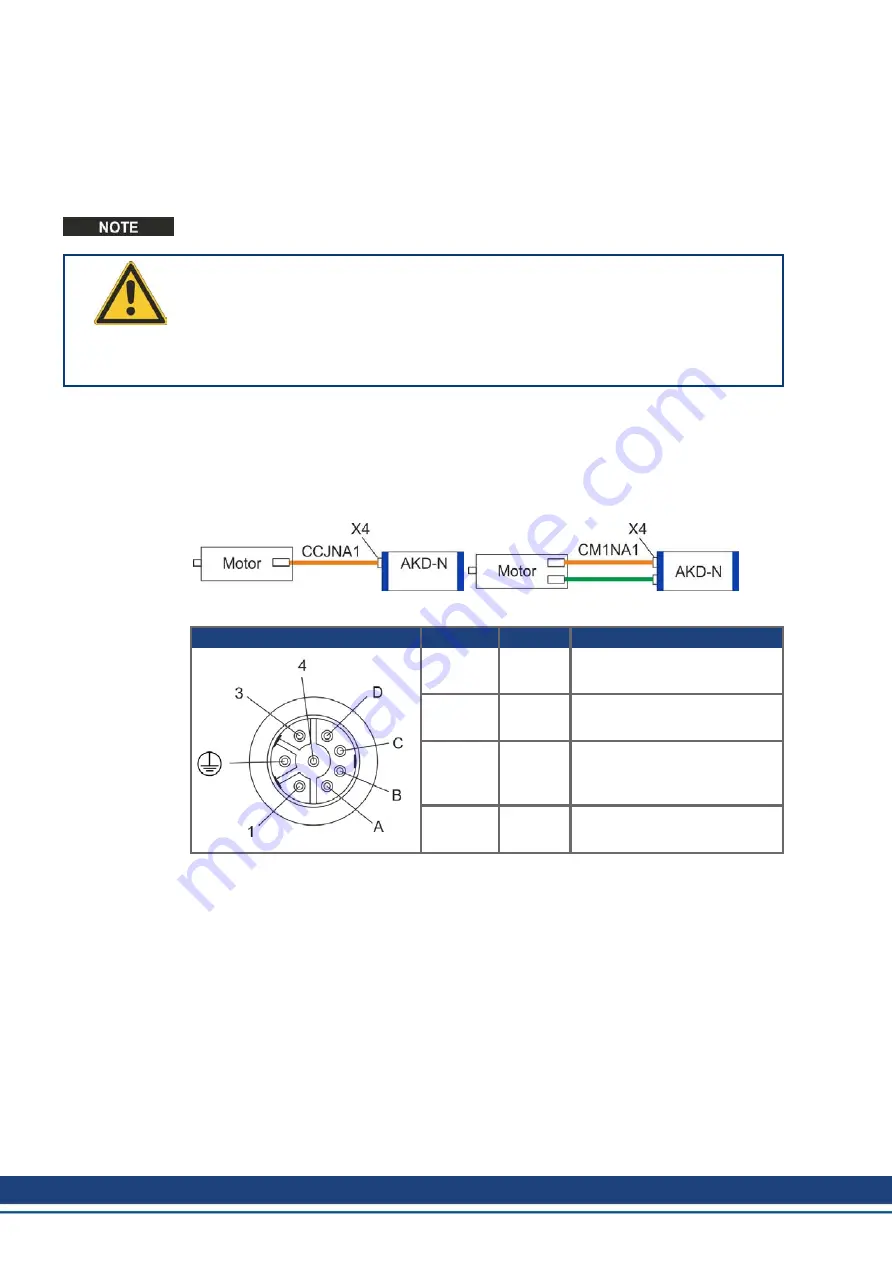
AKD-N Installation | 8 Electrical Installation
8.9 Motor Brake Connection (X4)
A 24 V holding brake in the motor can be controlled directly by the drive. The brake only
works with sufficient 24 V voltage level. Check voltage drop, measure the voltage at brake
input and check brake function (brake and no brake). Maximum current for the motor brake is
1 A with AKD-N00307 and 1.5 A with AKD-N00607.
The stand-by power supply from AKD-C limits the number of brakes in the system. Observe
the projecting hints for system topology and limits in the
Projecting Guide
.
CAUTION
This function does not ensure functional safety. Functional safety requires
and additional, external mechanical brake, operated by a safety con-
troller. Set parameter MOTOR.BRAKEIMM to 1 with vertical axes, to
apply the brake immediately after faults or Hardware Disable.
The brake function must be enabled and configured with parameter using WorkBench, for
details refer to the online help.
Single line hybrid cable and dual line motor power cable use two lines for motor holding brake
connection.
Single Line
Dual Line
X4
Signal
Description
A
+BR
Motor holding brake, positive
B
-BR
Motor holding brake, negative
C, D
...
Single Line: Feedback (
Dual Line: unused
1,2,3,4
...
Motor power (
58
Kollmorgen | December 2014