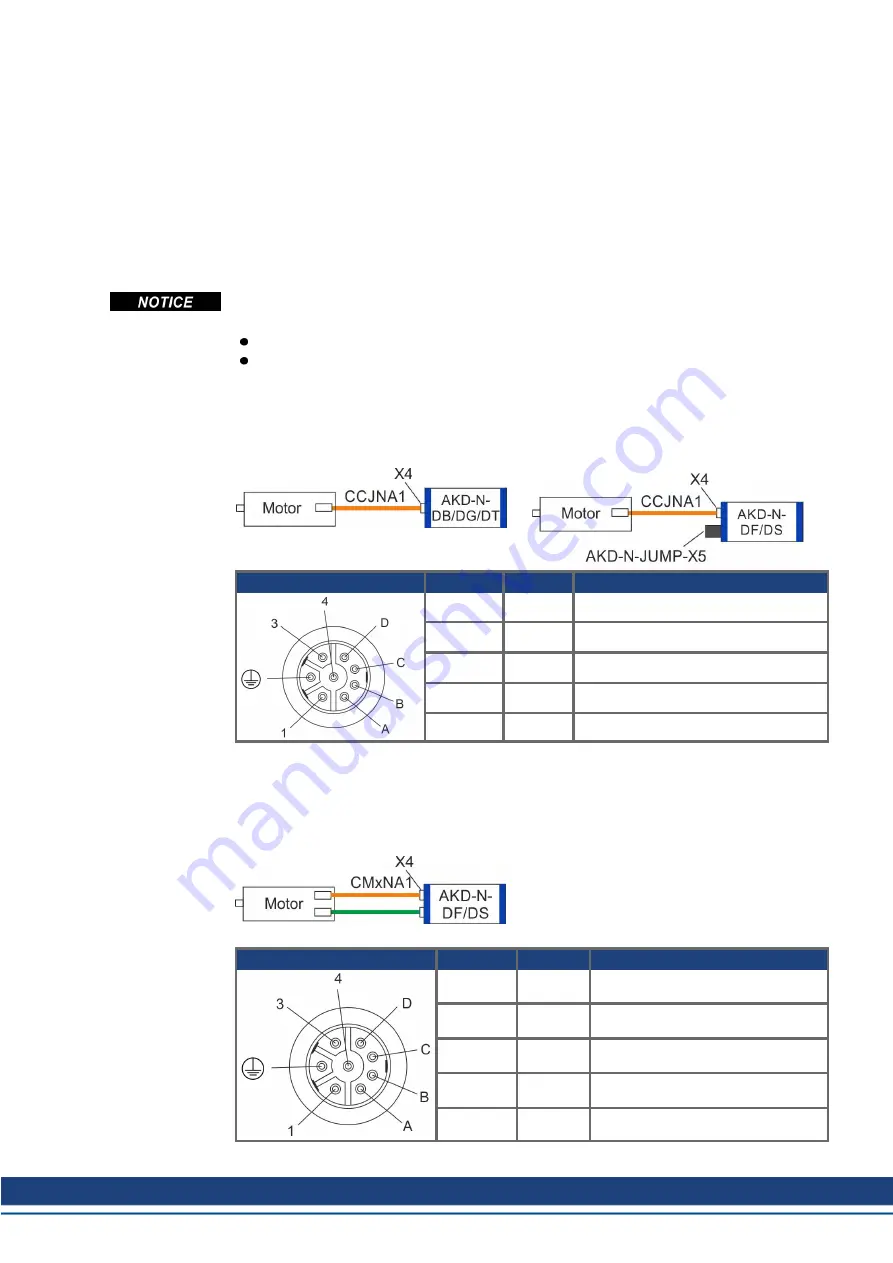
9.8 Motor Power Connection (X4)
Together with the motor supply cable and motor winding, the power output of the drive forms
an oscillating circuit. Characteristics such as cable capacity, cable length, motor inductance,
and frequency determine the maximum voltage in the system.
The AKD-N drive is able to protect the connected motor from overloading, if the parameters
are set correctly and the thermal protection sensor is connected and supervised. With Koll-
morgen motors the valid data are automatically set by the internal motor database. With
motors from other manufacturers the data from the nameplate must be entered to the refer-
ring fields in the motor view of the Kollmorgen setup software WorkBench.
The dynamic voltage rise can lead to a reduction in the motor operating life and, on unsuit-
able motors, to flashovers in the motor winding.
Only install motors with insulation class F (acc. to IEC60085) or above.
Only install Kollmorgen cables that meet the requirements (
9.8.1 Connector X4 AKD-Nzzz07 all variants, hybrid, single cable
Motors with single cable connection (motor power lines, motor holding brake lines and motor
feedback lines combined in one hybrid cable) can be connected to X4 of all AKD-N variants.
X4
Signal
Description
A, B, C, D
...
Feedback (
1
U
Motor phase U
2
PE
Protective earth (motor housing)
3
W
Motor phase W
4
V
Motor phase V
9.8.2 Connector X4 AKD-Nzzz07-DF/DS, dual cables
Motors with dual cables connection (motor power lines and motor holding brake lines in one
cable, motor feedback lines in a separate cable) can be connected to X4 and X5 of the AKD-
Nzzz07-DF and -DS variants.
X4
Signal
Description
A, B, C, D
...
Brake (
1
U
Motor phase U
2
PE
Protective earth (motor housing)
3
W
Motor phase W
4
V
Motor phase V
AKD-N Installation | 9 Electrical Installation
Kollmorgen | kdn.kollmorgen.com | February 2018
67