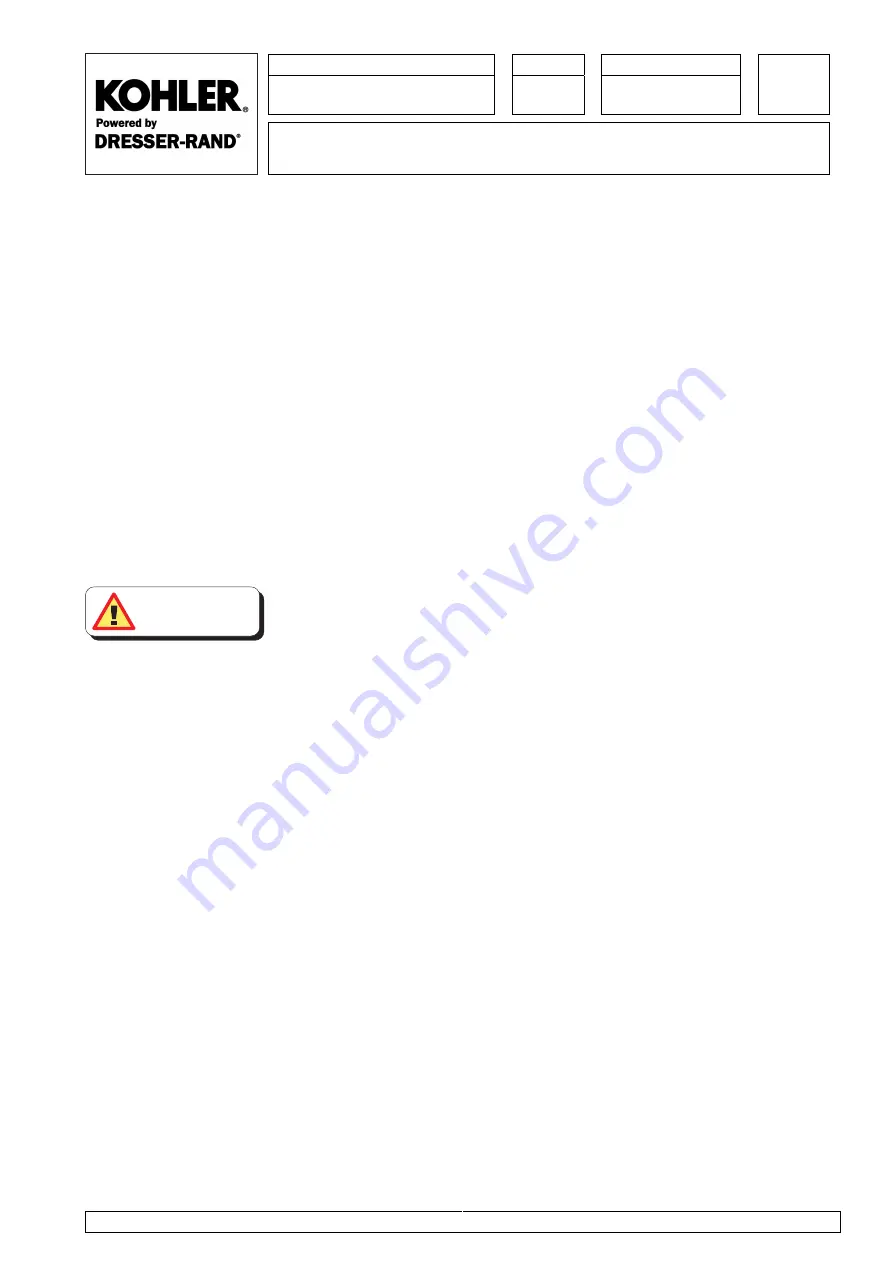
PRODUCT INFORMATION
INDEX
DATE
Dep.2
IO-C-M-00-004e
A
February 2012
GUIDE TO ENVIRONMENT-FRIENDLY WASTE MANAGEMENT
DURING PRODUCT MAINTENANCE AND AT END OF LIFE
1/5
1.
INTRODUCTION
Waste generated during the maintenance of Kohler equipment, or at the end of their useful life, demands
environmentally correct management. This guide establishes adequate environment-friendly waste management
procedures that aim at keeping the environmental impact as low as possible and at boosting waste recycling
and valorisation processes.
It is thus essential to disassemble, handle and manage the parts, components and waste removed from
Kohler
machines according to the waste management procedures that legislation prevailing at the equipment’s
operating site might provide from time to time.
Most components of the machines are ferrous and non-ferrous materials (scrap) that are usable as raw materials
in the iron and steel industry. All other non-reusable waste products will be disposed of to landfill sites. When
performing the a.m. disassembling, removal and handling operations, it is necessary to bear in mind the impact
they may have on the environment, including but not limited to contamination resulting from inadequate
arrangement of stored supplies or from ground pollution at the place where said operations are carried on.
The environmental impact that improper handling of waste products may cause further originates in machines
containing hazardous substances that must be considered throughout the operations said machines undergo.
2.
DECONTAMINATION AND DISASSEMBLY
ATTENTION
Maintenance staff shall decontaminate the machine, stripping it of all the parts that contain hazardous substances
and are classified as hazardous waste (see further below). Only if it is planned to reuse the complete engine
block is it admissible to keep it lubricated, omitting to extract oil.
The area assigned to decontamination operations shall comprise pollution prevention systems against accidental
spillage while handling the machines (sealed collection boxes) and (whenever possible) grease separation and
settling systems. Likewise, provisions shall be made to store decontamination process waste under cover and
separately in adequate containers, such as containers for batteries or sealed tanks for each type of liquid waste
(fuels, oils, coolants, etc.). Those tanks must have individual retention basins per type of waste, or similar
systems to ensure possible overflow containment.
All collected dangerous waste shall be forwarded, separately and subject to prior acceptance, to authorised
hazardous waste managers.
Decontaminated machines, which thus rank as NON-HAZARDOUS WASTE, shall undergo the following process:
disassembly and sorting of components and special waste products capable of reuse or recycling. This type of
waste includes metallic components that contain copper, aluminium and magnesium, electric parts and plastic
items.
It will thus be necessary to do the following: remove the battery as soon as possible, extract fuel and all other
fluids, materials and components classified as hazardous waste, discharging them into their respective, properly
tagged containers. Draining all the fluids must be carried on in the appropriate manner to minimise hazardous
waste generation at subsequent pressing and fragmentation processes and to make recycling easier. The fluid
removal means (funnels, drums, pumps, etc.) shall be assigned to one single duty exclusively and be duly
identified and tagged to prevent using them for other duties. For instance, gas oil extracting means shall differ
from lube oil draining equipment.
1.25
O&M_2.002211.810_A_10_2016