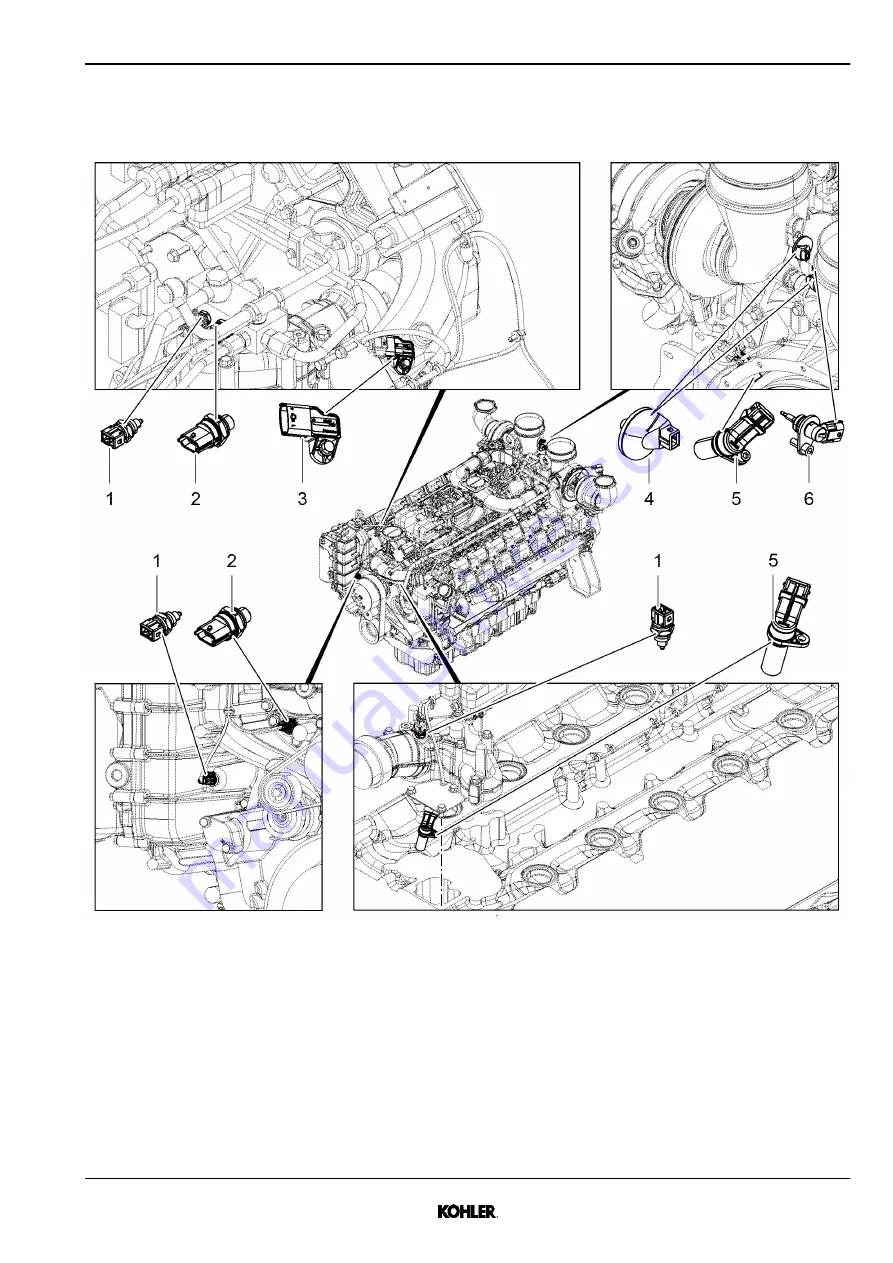
Operation and Maintenance Manual
Product description
Technical description
1.1.2 Overview of sensors
Fig. 3: Overview of sensors
1
Temperature sensor
3
Temperature sensor
5
Rotational speed sensor
2
Pressure sensor
4
Service switch
6
Temperature sensor
KD27V12 33521029401_3_1 en 2017-07-01
© 2017 by Kohler Co. All rights reserved.
13