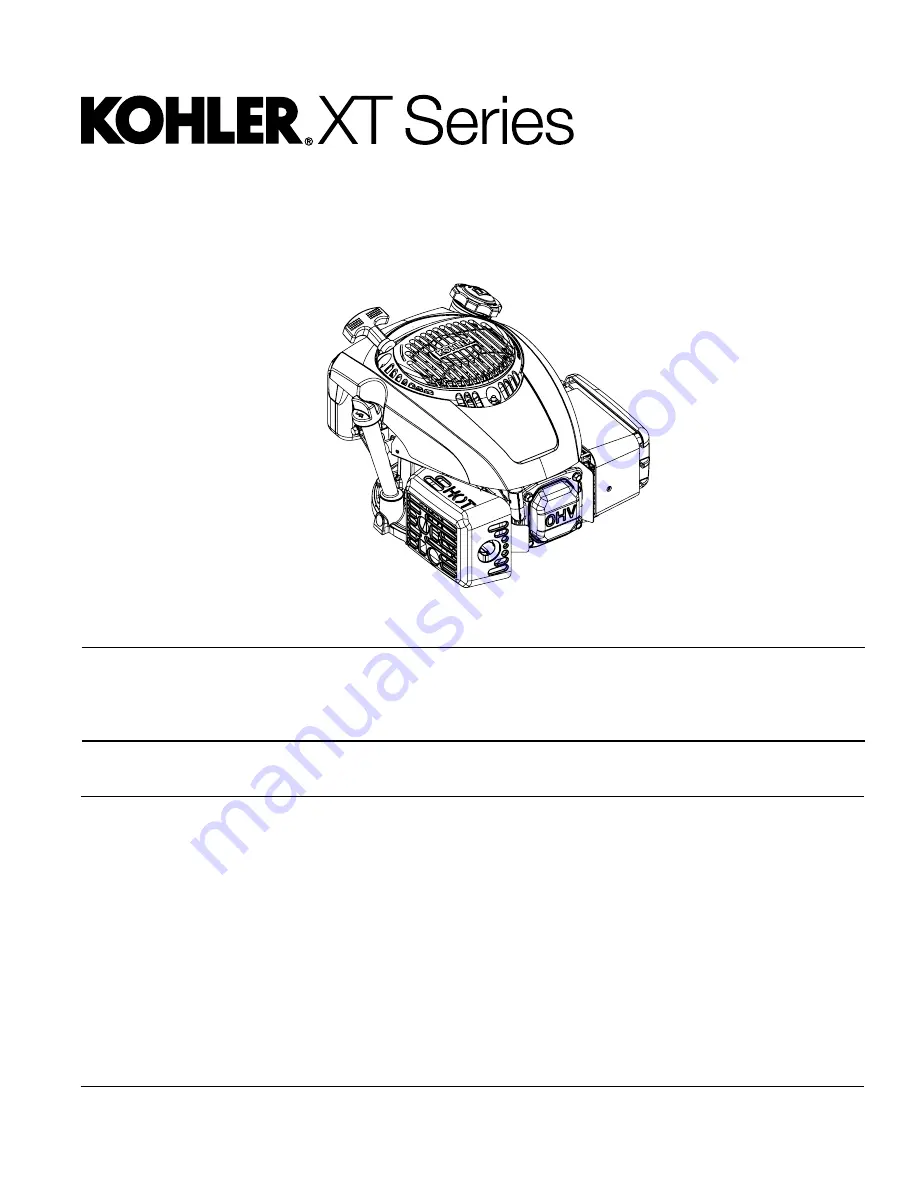
1
14 690 01 Rev. G
KohlerEngines.com
XT-6, XTR-6, XT6.5, XT650, XT6.75, XT675,
XT-7, XTR-7, XT775, XT8
Service Manual
2
Safety
3
Maintenance
5
Specifications
10
Tools and Aids
13
Troubleshooting
17
Air Cleaner/Intake
18
Fuel System
24
Governor System
26
Lubrication System
27
Electrical System
31
Starter System
33
Disassembly/Inspection and Service
45
Reassembly
IMPORTANT: Read all safety precautions and instructions carefully before operating equipment. Refer to operating
instruction of equipment that this engine powers.
Ensure engine is stopped and level before performing any maintenance or service.